With time and money tighter than ever, waterjet shops across the globe are looking for ways to maximize the productivity and profitability of their waterjet systems without spending too much on capital investments.
Some helpful insights on how to increase waterjet productivity and minimize waste without high expenditure were recently provided by waterjet industry veterans Jeff Schibley and Bradley Schwartz of Jet Edge.
According to Schibley and Schwartz, waterjet productivity can be increased in several ways, including X-Stream pressure pumps that can reach up to 90,000 psi (6,200 bar), mirroring programs that use two cutting heads to cut large parts twice as fast, multiple-head systems that can include over a dozen cutting heads, and nesting software that can maximize parts per sheet or plate.
Ancillary equipment such as abrasive removal systems, chiller and closed loop systems, garnet recycling systems, dual pressure valves, pneumatic drills, and height sensors can be added to waterjet systems to increase their productivity.
All of these productivity enhancements serve to increase a waterjet shop’s profitability as well as protect the planet by minimizing water and power consumption and material waste.
X-Stream Pressure Pumps
For many years, the standard operating pressure for most waterjet shops was 60,000 psi (4,100 bar). However, in the last five years, X-Stream pressure cutting technology has been used in the waterjet world.
X-Stream pressure waterjets can increase cutting speed by up to 50% using pressures exceeding 90,000 psi, depending on the material. By cutting faster, X-Stream-powered systems use less water, abrasive and power, and reduce operating costs as much as 40%.
Increasing pressure is where we can see tremendous efficiencies in the abrasive waterjet cutting process. By pressurizing to higher pressures, we get faster acceleration of the abrasive and we get more efficiency in the cutting process.
Jeff Schibley, Great Lakes Regional Manager, Jet Edge
.jpg)
A great example is NASCAR’s Michael Waltrip Racing (MWR). Since upgrading its waterjet intensifier pump to an X-Stream pressure pump, MWR has seen major productivity improvements, and its waterjet operating hours have reduced from 60 to 65 hours per week to 40 to 50 hours per week, saving on labor and overhead.
We've been seeing, across the board, a 35% improvement in cutting speed, plus we are using about 25% less garnet abrasive, and we have reduced our costs by 30%. As an example, our spindles, which are one of our more complicated steering parts and cut from 2" 4140 steel, used to take 50-55 minutes to cut at 60,000 psi. Now we are cutting them in 30-44 minutes. Before we got the waterjet, it used to take three or four hours to rough cut them on a band saw. I also should note that about the same time we upgraded our pump, we changed suppliers for our spindle blanks. They use a much harder material that requires a slower cutting time. The X-Stream offset the increased cutting time. Another good example of a reduction in machining time would be our upper control arm plates that attach our front suspension arms to the chassis. These are cut from 1.5" thick steel and took about 1 hour and 25 minutes to cut two with the double heads and the old 60KSI pump. We can now cut two in about one hour with the double heads and the 90KSI pump.
Nick Hughes, Technical Director, MWR
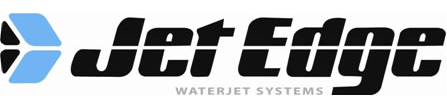
This information has been sourced, reviewed and adapted from materials provided by Jet Edge, Inc.
For more information on this source, please visit Jet Edge, Inc.