Dillon McDowell, Applications Scientist at Olympus Scientific Solutions Americas, talks to AZoM about XRF as an effective screening tool for RoHS substances.
Can you tell us why the Restriction on Hazardous Substances (RoHS) directive was established in the EU and how it impacts manufacturers around the world?
With the increasing presence of electronic devices in today’s society, electronic waste (e-waste) is being produced very quickly. Recently, the EU established a new set of rules to promote both the proper disposal of e-waste and to reduce the health and environmental risks associated with the increase in e-waste production. RoHS is one of those new rule sets aimed at reducing specific hazardous material from entering e-waste streams by restricting their use in electronic equipment. These materials include heavy metals (lead, mercury, cadmium, etc.), polybrominated flame retardants (PBB and PBDE), and phthalates. RoHS prevents specified electronic products from being imported, manufactured, or sold in the EU that contain (or whose components contain) these materials above certain levels. The regulation also puts forward specific testing, documentation, and verification obligations on both the manufacturer of these goods and on importers and distributors as well. The first set of regulations was enacted in 2006 but were later recast in 2011 (often referred to as RoHS 2), with the intention to phase in various types of electronics under the regulation over the course of several years.
What techniques are traditionally used to monitor these substances?
Historically, verification of material has been done through laboratory testing techniques. However, because of how diverse the list of restricted substances is, multiple techniques now have to be used. For example, heavy metal analysis is typically done via ICP-AES, polybromide flame retardants are tested via GC/MS, and hexavalent chromium is tested via UV-VIS.
Ultimately, no single analytical technique exists that can test for the complete range of RoHS substances, and laboratory testing can be time consuming and costly to do the full screening. Consequently, organizations are beginning to rely more heavily on screening techniques to identify risky material so that they can focus their lab testing only where it will best identify potential non-compliance issues.
Why has XRF been recognized as an effective screening tool for RoHS substances?
Handheld XRF offers the best combination of speed, reliability, and versatility of any RoHS screening technique. XRF testing can be done in seconds, enabling producers to make actionable decisions immediately, rather than wait several hours or days for laboratory results. XRF can screen for multiple RoHS elements simultaneously in a variety of materials, all using one device with minimal sample prep. Finally, it is completely nondestructive, meaning it can be performed at any point in the manufacturing process — even on finished goods.
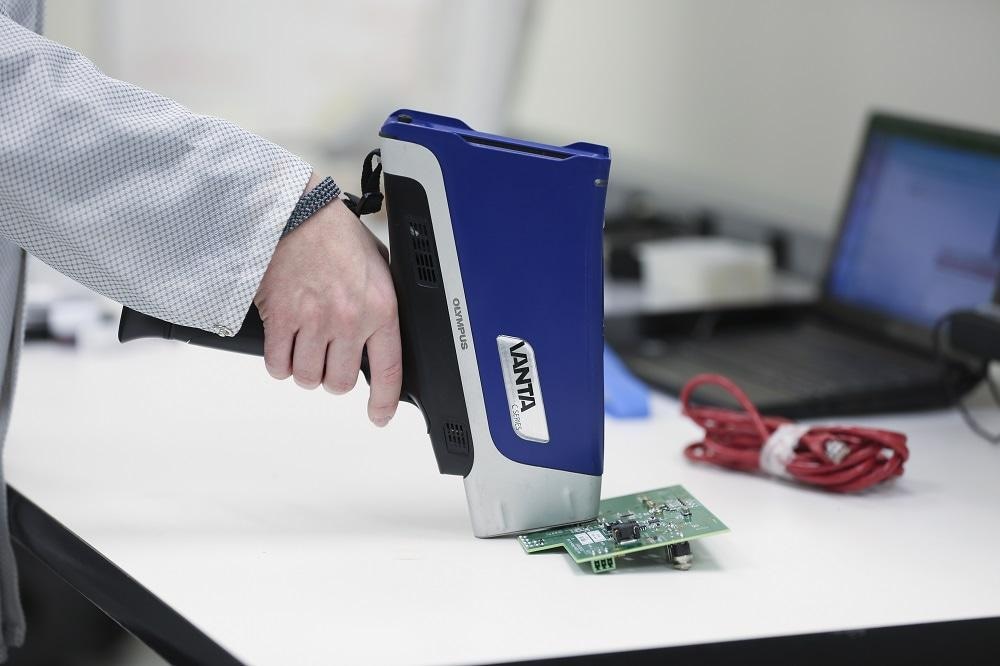
Medical device manufacturers are one of many industry sectors responsible for monitoring RoHS substances. How has the Electrotechnical Commission (IEC) helped develop global testing methods, and where does XRF spectrometry fit into the resulting standards?
Medical devices are the latest class of devices to fall under RoHS 2, and they are not the last. By 2019, nearly all Electrical and Electronic Equipment (EEE) will fall under the RoHS requirement. To that end, the IEC has established testing guidelines that were developed in coordination with EU regulators to ensure best practices for compliance. While they are internationally recognized standards, they are identical to the EU standards for RoHS compliance. These IEC standards establish codified methodologies to analyze for restricted materials and also provide recommendations for establishing a reasonable testing plan (RTP) within manufacturing organizations and their supply chains. One specific IEC standard, IEC 62321, provides testing methods specifically for RoHS and includes guidance on XRF screening, including testing methodologies and appropriate action levels for specific material types.
Why has XRF seen such a wide uptake in popularity at all levels of the supply chain?
Handheld XRF provides an excellent combination of speed, reliability, and low cost compared to other testing techniques. It can generate results in seconds, enabling organizations to quickly test large amounts of material and pick out potential risks for further testing. It can measure, either directly or indirectly, most RoHS materials at levels well below actionable limits. Finally, testing can be done with little sample preparation, reducing both cost and potential testing errors.
Laboratory testing will always be required to meet some testing obligations, but XRF can reduce the amount of lab testing needed and the costs associated with it. All these aspects are combined in a flexible instrument that can be used at any point in the supply chain and requires minimal training to operate.
Understanding handheld XRF results is critical for meeting compliance criteria. What has Olympus done to make screening easier and faster?
RoHS guidelines can be tricky to navigate, so our analyzers make the process simpler by providing a clear indication of “Pass/Fail” based on the IEC guidelines. This way, even if your operator isn’t knowledgeable about current guidelines, the analyzer will inform them how best to interpret the results according to IEC 62321. Additionally, the analyzer can identify the family of material being tested, be it a polymer or an alloy, and automatically adjust so that it reports such determinations based on specific material types. Finally, our analyzers possess tools that enable automated report generation as well as fast data uploads to computer or network systems for better tracking.
Import safety and border security for government agencies is under constant pressure to ensure what comes in and out of any given region is regulated properly. How has XRF helped make testing a practical solution?
Import and border agencies process millions of goods every day, so a tool that maximizes throughput in verification is essential. Handheld XRF is one of the few tools that offers that kind of throughput while also being effective in screening for multiple substances. In the United States, for example, the consumer product safety commission (CPSC) has recognized XRF as a valuable tool in screening for hazardous substances (similar to ROHS). In addition, regulators in the EU have issued enforcement documents recommending handheld XRF as part of their “first steps” in import screening.
VantaTM analyzers are the latest development in the Olympus handheld XRF analyzer range. What's different about the Vanta analyzer and how has it made the screening process easier?
Sensitivity and productivity tools are what give Vanta analyzers an edge when it comes to compliance screening. The analyzer utilizes our proprietary Axon™ technology for revolutionary sensitivity and stability. This translates to excellent accuracy and limits of detection for nearly all sample types. Users can be confident that the first test and the last test of the day yield the same results. Finally, the analyzer has optional Wi-Fi and Bluetooth® capabilities, along with cloud connectivity, making it easy for organizations to sync results to internal QC systems for fast and reliable report/certificate generation. All of these features are packaged in a lightweight, handheld system with an easy-to-use touchscreen and intuitive user interface that can even be customized to suit an organization’s specific needs.

How do you see the screening directives developing over the next decade, and how will XRF evolve with it?
The last two decades of hazardous substance regulations the world over have seen increases in scope as well as decreases in acceptable levels of regulated substances. There is little indication that this trend will slow in the coming years, so the screening directives associated with them will follow suit. There is even the potential for XRF screening to become required rather than merely an option. In fact, some industry leaders are already requiring it of their suppliers. As such, organizations that are adopting XRF screening into their compliance practices today will likely be better positioned for future regulatory developments. XRF technology will also continue to develop along with the trend for tighter regulations, and the Vanta analyzer is the next step in that development. The analyzer’s improved speed, sensitivity, and reliability give organizations the capability to help meet these changes.
Where can our readers learn more about the Olympus range of XRF products?
Visit Olympus-ims.com for details on Vanta analyzers, XRF, and our complete product line.
About Dillon McDowell
Dillon McDowell is an Applications Scientist at Olympus Scientific Solutions America, specializing in using X-ray fluorescence (XRF) and other analytical technologies in alloy, precious metals, and regulatory (RoHS and consumer product safety) applications. Before joining Olympus, Dillon was a research assistant at Northeastern University’s Nanomagnetism Research Group. Dillon has a BS in physics and MS in mechanical engineering from Northeastern University and his work has been published in the Journal of Material Chemistry C.
Disclaimer: The views expressed here are those of the interviewee and do not necessarily represent the views of AZoM.com Limited (T/A) AZoNetwork, the owner and operator of this website. This disclaimer forms part of the Terms and Conditions of use of this website.