There is increasing pressure on today’s microelectronics industry to produce smaller, more reliable, more powerful devices that are also cheaper to manufacture. The packaging system is one key feature of many devices that is used to shield the device against physical damage and against environmental degradation of performance.
While hermetically sealed packages are popular amongst high-cost and high-reliability applications such as defence and avionics, a more cost efficient solution is required for industrial and consumer applications. Encapsulating the device and the interconnection system in a thermosettable polymer resin is the most common packaging solution used today.
However, the commonly used epoxy resins suffer from a dangerous problem, i.e. they absorb moisture from the atmosphere they are exposed to during storage. In the worst scenario, this can lead to an effect called ‘popcorning’ during the wave soldering process, in which the absorbed moisture is suddenly exposed to temperatures well above 220 °C, leading to a violent release of vaporised water from the plastic device package (see Figure 1).
.jpg)
Figure 1. Schematic of the ‘popcorn’ effect.
This and other related moisture absorption issues have created the need for accelerated testing of microelectronic packaging systems to prevent major problems from occurring during the manufacture or during the service of the device.
One of the most commonly used conditions is 85 °C and 85% RH originally adopted from US military standards but is now widely accepted within the industry. However, almost all the existing test procedures are semi-empirical in basis, determining the device’s functionality as the pass or fail criteria. This clearly underlines the need to understand the fundamental moisture interaction with the packing materials, in order to gain a better insight into the effect of moisture over the entire life cycle of a microelectronic device.
Surface Measurement Systems has recently developed a dedicated gravimetric moisture sorption apparatus called the DVS Resolution, which has been designed specifically to study the moisture sorption of actual microelectronics packaging devices under precisely controlled humidity and temperature conditions.
The key features of this instrument are high capacity (10 g), high sensitivity (1 µg) and extremely good long-term stability of the measured mass as well as the generated % RH.
Method
The device package used was a standard 16 pin DIL IC package with through-hole interconnects weighing approximately 1 g total weight. The sample was suspended from a sample holder in the DVS Resolution apparatus and subjected to 0% RH at 85 °C to dry the sample.
Following a certain fixed time period the humidity was increased to 85% RH. The resulting change in the sample mass owing to the loss and gain of moisture from the packing device was recorded at fixed intervals of 1 minute throughout the experiment.
Please click here if you would like more information on the instrument used in this article or a quote
Results
Figure 2 depicts the kinetics of drying under 0% RH and 85 °C. Over the duration of the drying step, the loss in mass corresponding to the diffusion of moisture out of the device package is in this case approximately linear. A least squares regression analysis of the data demonstrates that the rate of moisture loss from the device package is about 0.7 µg per minute.
Due to time limitations, the sample was only dried for a short time in this test; however, it is reasonable to expect the rate of drying to follow an asymptotic behavior as the moisture content decreases. Several factors determine the rate of moisture loss such as the package dimensions, the package material properties, initial moisture content and any heterogeneous features such as the interface between the packaging resin and the device interconnects (lead frame).
.jpg)
Figure 2. Frying Kinetics of 16 pin DIL IC Package.
Shown in Figure 3 is the moisture sorption kinetics for the 16 pin DIL IC after being exposed to a constant humidity condition of 85% RH and 85 °C, as well as the drying data shown previously. % RH is indicated by the blue line and the change in mass as a function of time is indicated by the red line.
In this case, as the humidity is stepped up to 85% RH, the mass increases quickly at first and then in an asymptotic manner later on, as the sample begins approaching equilibrium. Following the initial uptake, the rate of increase in mass almost reaches a pseudo steady state, since the diffusion into the bulk of the package is quite slow.
Considering the last 1500 minutes (~ 1 day) of data, it can be inferred from a linear regression analysis that the device package is taking up moisture at a rate of nearly 0.2 µg per minute.
.jpg)
Figure 3. Kinetics of Moisture Sorption of 16 pin DIL Package at 85% RH and 85 °C.
It is to be noted that the DVS Resolution can be programmed to generate humidities ranging between 0% and 90% RH at 85 °C with a repeatability better than 1% RH, albeit a single humidity step of 85% RH was selected for this study. Equilibrium measurements at several different humidity levels can also be recorded to construct adsorption and desorption isotherms.
Conclusion
This brief study shows the accuracy and sensitivity of the DVS Resolution, which has been specifically designed for use at 85% RH and 85 °C.
While the total uptake of moisture during the experiment is not more than 0.25% of the total weight of the device, it is believed that even moisture contents down to 0.1% have a major impact in terms of ‘popcorning’ and other device failures.
Thus, the sensitivity of the DVS ET allows moisture absorption in microelectronics device packages to be determined accurately. This will allow materials, Scientists and Product Development Engineers to relate such data to production-specific problems as well as accelerated device-testing protocols presently being used.
Acknowledgement
SMS thanks Mr. C. L. Levoguer for his contributions towards the article.
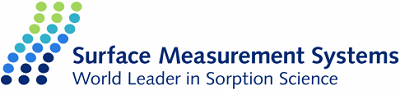
This information has been sourced, reviewed and adapted from materials provided by Surface Measurement Systems Ltd.
For more information on this source, please visit Surface Measurement Systems Ltd.