With RICE NESHAP rules not far away, selective catalytic reduction (SCR) systems are often regarded as the preferred technology for reducing noxious emissions caused by gas and diesel engines. SCRs provide a cost effective and reliable way to reduce harmful emissions, particularly Nitrogen Oxides (NOx) and bring them within the acceptable regulatory levels.
How They Work
Selective catalytic reduction systems work by converting nitrogen oxides into water (H2O) and diatomic nitrogen (N2). When released, both H2O and N2 are harmless and they are safe for the environment. The method for performing this conversion is to combine the NOx and a ‘reducing agent’, typically ammonia (NH3), which makes a contact with the catalyst in order to produce the reaction that splits the NOx into H2O and N2. SCR systems are capable of reducing the NOx level by 70% to 95%, based on the specific application.1
SCRs and Insulation Blankets
The catalyst block inside the housing has to reach an optimum operating temperature, typically between 674 °F and 836 °F 2 so as to allow the SCRs to function properly. Various other factors may reduce the exhaust temperature to less than this optimum range, for instance, ambient temperature, length of exhaust piping, the site of the SCR system (indoors vs. outdoors), etc. These high operating temperatures can also cause safety concerns for workers who are operating close to these systems even beyond this optimum range.
.jpg)
SCR System, without Insulation Blankets
Due to these reasons, removable insulation blankets often go along with SCR systems. Insulating both the SCR housing and adjoining piping helps maintain the exhaust temperatures and enables the catalyst to operate optimally. Ambient heat, which can be a problem in enclosed spaces such as an engine room, is lowered as well, providing a safer environment. Finally, since the insulation is removable, it allows simple access to components for repair and maintenance.
Challenges
The geometry and shape of the SCR systems can be rather complex. Instead of being one continuous surface, the SCR systems are mostly made of panels connected at various angles and / or different levels.
.jpg)
.jpg)
An abundance of access points, test ports, protrusions, etc. and structural bracing increase the complexity. This poses a challenge while designing removable blankets that will be easy to install and fit properly.
.jpg)
SCR System with Removable Insulation Blankets Installed
Firwin’s Senior Designer, Jon Miles says, “Ensuring a proper fit is essential when designing removable insulation blankets for SCR systems, both from an aesthetic and functional point of view. You certainly don’t want any gaps between blanket panels for heat to escape, and you want the final product to look good and not like a bunch of blankets thrown together”, said Jon. “You also want to make sure that the final product is simple to install. This means that the size of the individual blanket panels should not be too large, and that it should be intuitive, even to a novice, which blanket is intended for which location”, added Jon. “We try to design the insulation blankets so that they can be installed by 1 or 2 people in 1 shift. And we typically will provide an installation diagram to guide the customer as to which parts go where.”
.jpg)
SCR Installation Diagram
Putting It All Together
Removable insulation blankets are often considered as a vital component of an SCR system. Both SCRs and their adjacent exhaust piping usually become quite hot. Insulation blankets that are properly designed and installed can help protect personnel, reduce the ambient heat to an acceptable level, and ensure that the internal exhaust temperature remains sufficiently high in order to allow for optimal catalyst performance and to meet regulatory targets.
References
- http://www.cormetech.com
- http://en.wikipedia.org/wiki/Selective_catalytic_reduction
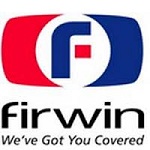
This information has been sourced, reviewed and adapted from materials provided by Firwin Corporation.
For more information on this source, please visit Firwin Corporation.