Additive manufacturing (AM), or 3D printing, is one of the latest and most sensational developments in manufacturing since the industrial revolution. The technique is mainly based upon ‘layer-by-layer’ fabrication and allows physical solid parts to be created directly from electronic data files such as computer-aided design (CAD) software.
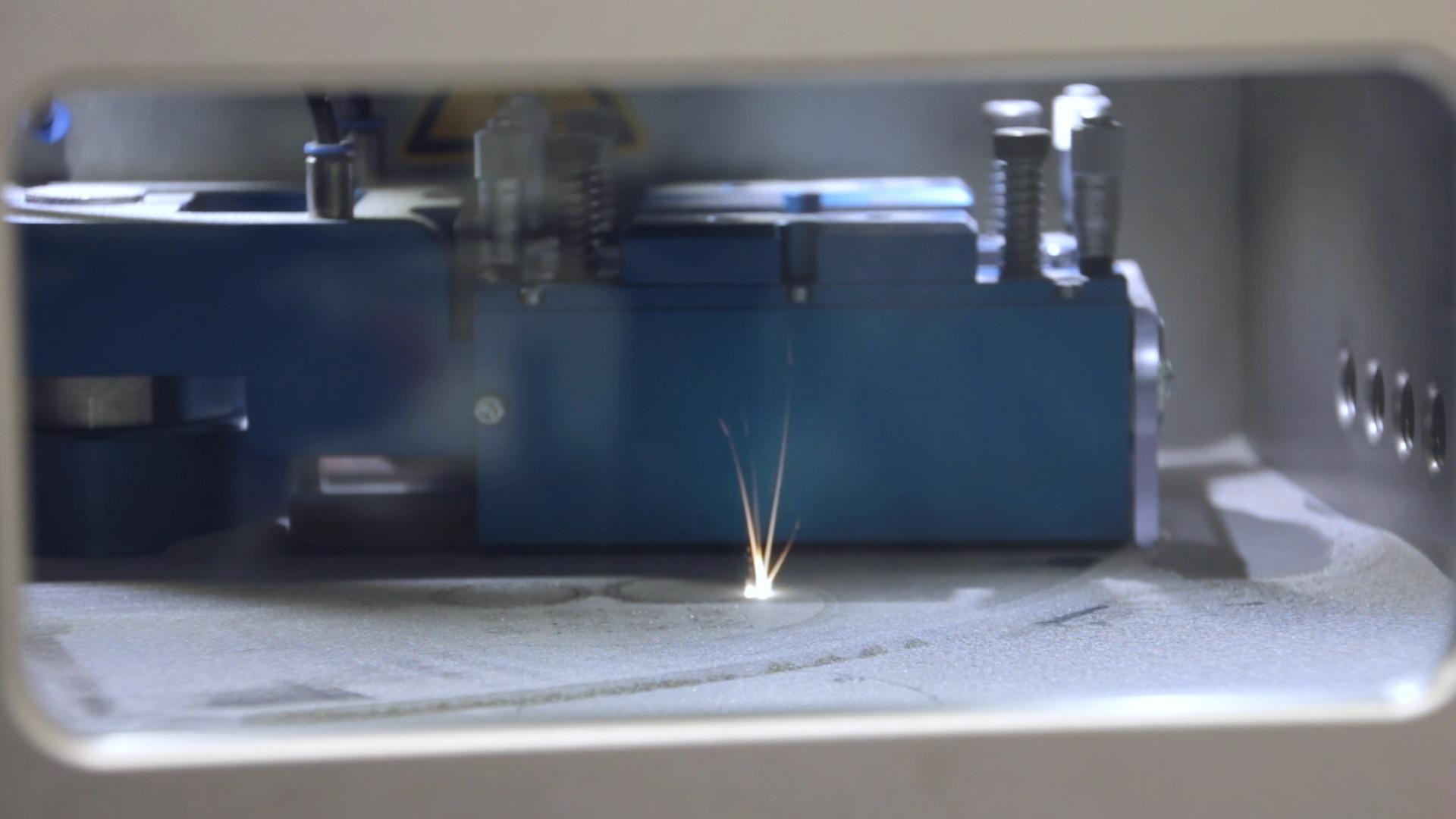
AM technology provides many design and manufacturing benefits such as design freedom in geometry, short lead time, and no tooling requirements. Parts can be created as required on-site and hence, there are great advantages for the requirements of the US-Army and Navy servicing ordinance and equipment in the field.
However, some issues still remain. There is a question of the quality of the final part (i.e., testing against mechanical failure) and the usage of consistently superior-quality metallic powder starting materials to guarantee the quality of the final component. Variation in powder density can lead to rough, porous, and mechanically weak parts.
Powder-Bed AM Methods
Powder bed fusion (PBF) processes are presently the most common AM techniques used in the aerospace and medical implant industries to create complex components with tight dimensional and surface finish tolerances as well as good mechanical strength.
Powder-bed electron-beam-melting (PB-EBM) is a comparatively new AM technology; it makes use of high-energy electron beams, as a mobile heat source, to melt and fuse metal powder particles together to create components by building in a layered-fashion. In creating each layer, the process includes powder spreading, pre-heating, as well as contouring and hatch melting. In powder spreading, a metal rake is used to evenly distribute each layer of powder. Pre-heating is applied using a single beam at a speed of about 15 m/second, with multi-pass scans, to reach a steadily high temperature across the entire powder-bed surface.
Following the pre-heating stages, the contour/hatch-melting phases occur, where electron beams, travel across the powder-layer surface tracing the model cross section contour and then lastly raster-scanning through the inside of the contour at a lower scanning speed.
PB-EBM is one of the few AM technologies that can make full-density metallic parts. In powder bed fusion processes, the density of the powder layers in the powder bed is one of the main factors together with the porosity of the particles themselves.
Defining Powder Bed Density
True density is an inherent property of a material, while apparent density takes into consideration any occluded voids within a material. Being aware of the true and or apparent density of a material feedstock is vital for powder bed formation and sintering kinetics in the AM process as well as the porosity, or lack of porosity in the end product.
Determination of tapped density and apparent density does not essentially reflect the density of the powder layer or powder bed. Apparent density mimics the loose packing state of powder, and is measured based on the ASTM B212 standard. However, a lot of the AM literature use terms such as powder bed density, bulk density, or packing density to explain the density of the powder bed during the powder bed fusion process.
The ideal way to measure the density of a metallic powder in AM is powder-bed density. Although a few have tried to study powder-bed density, no current standard is present for this measurement. The challenges are:
- To establish the actual layer density during the printing process
- To establish how to improve the applicable AM processing parameters so as to attain the maximum powder packing and achieve higher quality built parts.
An alternative measurement is the Bulk Density (BD), and this is impacted mainly by the distribution of particle shapes and sizes. BD is crucial in determining material specifications and can also obtain assurance regarding the structure of the powder bed and powder flowability. Envelope density is another beneficial parameter and this is based on the geometric volume of a sample and is convenient when characterizing the final product as it can measure the volume of intricate and irregular end products.
The AccuPyc II 1340 Helium Pycnometer, GeoPyc 1365 Envelope, and T.A.P Density Analyzer from Micromeritics allow workers to establish important density and porosity measurements needed to standardize process parameters and then qualify and approve supplied vendor raw materials, as well as a possible indicator to final product quality.
Integrating the true density from an AccuPyc measurement means that porosity can be established swiftly and easily. Both instruments used non-destructive testing techniques and when used together can specify total porosity of any metal powder.
Variations in Powder Density
There are several factors that influence variation in AM process results, and even if it is assumed that the external influences are constant. The factors that have the most effect are the laser/electron beam parameters, the process environment (i.e., excessive moisture, the presence of an inert gas), or the condition of the metallic powders themselves (particle size, particle shape, distribution, or flowability).
Flowability is mainly governed by particle morphology, and is a vital characteristic of powders appropriate for AM. Spherical powders with an ideal particle size guarantee the optimum packing density during flow and processing, which positively influences the integrity and surface finish of AM-constructed parts. This is because particles with a spherical shape can realize the maximum relative density compared to other shapes.
Powders appropriate for powder bed flow AM are usually produced by a process called gas atomization to attain the best morphology. Powders acquired for AM should be rechecked by scanning electron microscope (SEM) to expose whether it is ideal for a particular AM process, or whether it would profit from further processing to make irregular particles spherical.
Current research indicates that a higher powder packing density creates dense components with smoother as-designed surfaces. A moderately lower packing density also seems to improve fluid convections driven downwards by gravity. These strong downward flows tend to boost melt pool hydrodynamic instabilities and cause the formation of ‘balling’ defects.
Balling happens when a molten pool formed during the selective laser melting of the AM process becomes discontinuous and breaks into separated islands increasing the chance of probable mechanical defects and surface issues. Increasing the average packing density from 38% to 45% removes the discontinuous molten pool and creates a smoother surface contour.
Powder Bed Design
The way in which powder particles are firmly packed together during the powder-raking process is of the utmost importance for AM, so as to attain dense parts.
It is well established that spherical particles have the maximum packing density as compared with other forms of particles. Bigger particles have a higher packing capacity than small ones because of the relative contribution of gravity versus the particle-particle forces. Particles with a wider particle size distribution (PSD) have a better packing ability than those with a narrower PSD. Furthermore, different powder-bed fusion machines, such as EOS, Arcam, Concept Laser, and 3D Systems, use different powder-spreading methods, resulting in different powder-bed densities.
The current powder-packing density using hard or soft coaters is 47%–55%, which is like the packing capacity at the apparent density. Other 3D printers use a roller method to spread and compress the powder, which is claimed to accomplish better powder-bed density and higher quality built components. It is also true that the processing time would be considerably shorter if the powder-bed density was enhanced.
Conclusion
Additive manufacturing using metallic particles is a developing methodology. The conditions for success can be exacting and there are several factors involved. As far as metallic particles are concerned, the overriding issue is with particle size, flowability, particle shape (spheres if possible), and the achievable density as the powder is positioned in each layer before sintering or melting.
The metallic powders have to be carefully improved for application in AM. Micromeritics have a range of density and pore measuring instrumentation such as mercury porosimeters and helium gas pycnometers that are ideal for this purpose.
Download the 3D Printing White Paper for More Information
References and Further Reading
- Xibing Gong et al., Powder-Bed Electron-Beam-Melting Additive Manufacturing:
- Powder Characterization, Process Simulation and Metrology, ASME Early Career Technical Journal, 2013 ASME Early Career Technical Conference, ASME ECTC, November 2 – 3, Birmingham, Alabama USA
- Gong X, Anderson T, Chou K. Review on Powder-Based Electron Beam Additive Manufacturing Technology. ASME. International Symposium on Flexible Automation, ASME/ISCIE 2012 International Symposium on Flexible Automation ():507-515. doi:10.1115/ISFA2012-7256.
- Slotwinski J, Garboczi E, Stutzman P, Ferraris C, Watson S, Peltz M. Characterization of Metal Powders Used for Additive Manufacturing. Journal of Research of the National Institute of Standards and Technology.2014; 119: 460-493. doi:10.6028/jres.119.018.
- Paul A. Webb, Volume and Density Determinations for Particle Technologists, February 2001
- G. Jacob,. et al., Measurement of powder bed density in powder bed fusion additive manufacturing processes, Measurement Science and Technology, 27, 2016, 115601, pp12
- QuyBauNguyena, et al., Characteristics of Inconel Powders for Powder-Bed Additive Manufacturing, Engineering, Volume 3, Issue 5, October 2017, Pages 695–700

This information has been sourced, reviewed and adapted from materials provided by Micromeritics Instrument Corporation.
For more information on this source, please visit Micromeritics Instrument Corporation.