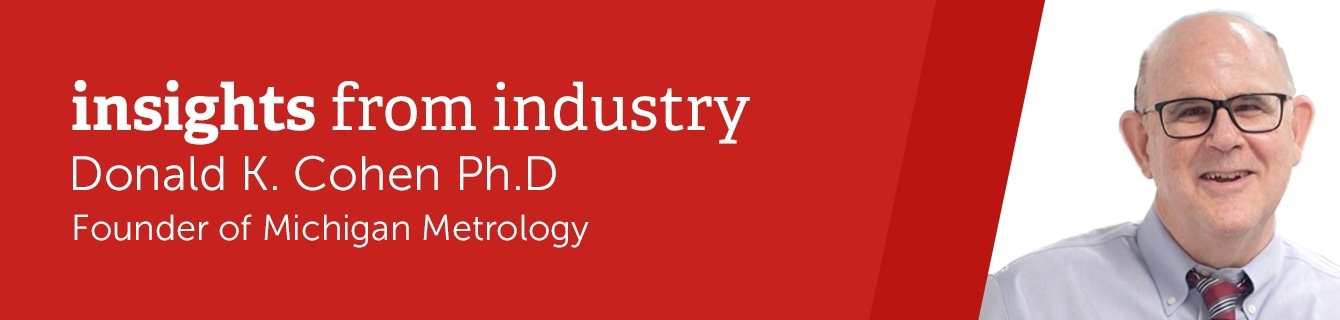
Dr Don Cohen of Michigan Metrology/Bruker talks about how his experience in the world of friction and wear has seen him strive to make better and longer-lasting products in the automobile and medical industries.
First can you tell us a little bit about the history of tribology? How long has it been around?
It started a million years ago when the first cave person knocked two stones together and suddenly there's tribology because the minute people begin rubbing stuff, they are already studying tribology friction. They soon realised that lubrication was a good idea as they could put water on things and see smoother transit. Tribology is a fundamental effect that humans have been involved in. In a historical sense, the cave people started with stones and stone tools and the formation of stone tools, which were all about tribology friction. Banging stones together was ultimately to create fire by using friction.
Tribology: In Pursuit of Longevity
Tribology: In Pursuit of Longevity from AZoNetwork on Vimeo.
In a more modern sense, at least in the history books, people always go back to the Egyptians and they show pictures of the Egyptians moving these huge stone statues and stone blocks and they're obviously figuring out a lot about friction, how to move something that large. They started to uncover the issues of sliding friction and they were able to mitigate the sliding friction by using lubricants. There are sketches of people pouring lubricants, usually a fluid, an animal fat or something underneath the stone in order to move it. They eventually realized if they put stuff on rolling elements that rolling friction would be a lot lower than sliding friction so ancient man really has been dealing with tribology since time began.
Da Vinci was the first one to draw two surfaces rubbing against each other what did he discover about tribology?
Da Vinci was one of the pioneers as he began to systemize and study what we call the laws of friction. Of course, they're not really laws like Newton's laws of gravitation. They're just empirical observations that when you rub bodies together there is a certain behaviour and that the larger the force between those objects, the higher the frictional force. Da Vinci also observed something that was strange and it was what he called the extent of the object and it didn't seem to affect the frictional force. If I took a block and put it on its flat wide side or if I took the same block and put it on its narrow side, the frictional force was the same and that was an odd thing that the frictional force didn't appear to depend upon the extent of the object and how much it was touching the surface. DaVinci’s two laws were:
- the areas in contact have no effect on friction
- if the load of an object is doubled, its friction will also be doubled
This led to a lot of uncertainty in friction and understanding the science until a Frenchman, Guillaume Amontons (1663-1705), rediscovered and redeveloped these laws of friction. At this time, there was a lot of misunderstanding, or a variety of understandings, I should say because it turns out they all were right as to the sources of friction. Two sliding objects, one against the other, which causes the friction, and some people thought, "Well, it has to do with the surface roughness so that as one surface is sliding over the other, these little mountains and valleys interact and cause some kind of, say, interference so that there's a resistance force." Other people thought more of the friction was coming from adhesion between the surfaces, and it really didn't matter what the surface roughness was. If you have surfaces that are very, very smooth, the frictional forces tend to come from adhesion. If you have surfaces that are very, very rough, then indeed the frictional forces can come from one object sliding over another and peeling into one another, and then in the middle of all that is where you get interesting science. This wasn't really understood until about 60 years ago, that's how current this field is. The real key people in the field, Bowden and Tabor, basically came up with a new idea. The argument was that maybe friction is about something related to the true area of contact and maybe adhesions, so it connected both ideas of surface texture and adhesion, and it turned out they're pretty much right. This launched the revolution in friction and tribology, along with new technology such as scanning electron microscopes and stylus profilometers, that allowed us to look at the surface texture in more detail.
How did this new technology help?
These scientists were able to look at the surfaces now in greater detail and realized that this made some sense. That when you bring two surfaces together trying to understand their frictional interface, what's the real area of contact? They realized that once I know the real area of contact, multiply that by some type of adhesion between those areas of contact then I can get a handle on where the friction is coming from. It turned out that model worked out quite well. If you take the extremes, if the surface gets super, super smooth, then the real area of contact is very, very large and the friction gets large. On the other hand, if the surface gets very, very rough, the initial real area of contact could be very small because little mountains are sitting on top of each other. But at that point, you're not in this adhesive mechanism, you're more in a ploughing mechanism where one surface is ploughing into the other, so at very rough surfaces, the friction could also get larger. Actually, there are three regimes when it comes to friction and surface texture. If it's too smooth, you can have high friction, too rough you can have high friction. At some optimum surface texture, you get a minimal amount of friction.
How does this relate to current challenges?
The challenge that industry has had over the years is that different surfaces behave differently. What's happening now in the current nano world is that an all new world of physics is opening up in what we call nanotribology. Because now, when we get to a scale where the objects are so small that the forces of interaction, the adhesion forces, the capillary forces, act in such a way that our basic laws of friction are not valid. We're talking about the friction that one might experience in these microelectronic mechanical structures. This opens up a whole new field in using scanning electron microscopes, atomic force microscopes, optical profilers, and other types of devices to understand tribology at the nano level.
How has your customer base and their demands changed over the years, or have they?
Yes, they have definitely changed. I have two major markets I deal with: the automotive, of course, and also medical, a lot of medical stuff. On the automotive side, the thing that's driving it more than anything is that people just demand warranties that go forever. I mean, if you think about this, a good example is a spark plug, when we used to have real spark plugs. We used to change spark plugs regularly. It was no big deal to change spark plugs. You don't change spark plugs anymore. That's how all the components are going. We want all our car parts to never have to be changed. We don't want them ever to break. We don't want things to wear out. We don't want things to start making noise. The quality demand that we have on our automobiles is enormous.
That's driving our industry more and more. Not just the quality but also the perception. It's going to work. Like for example the brake industry. The car is going to stop. That's not the issue. The issue is, how does it feel when it stops? How does it sound when it stops? That's the issue. The consumer is driving for such a high degree of quality that my company is affected by that, because people are driving for not only, say, how does a new part sound when it's used, but how long will that part last? Both the initial, if you will, tribology, and then the wear rate and how long will it wear.
What about your medical clients?
The same thing could be said for the medical industry as well, because we're becoming these bionic creatures. We think nothing of it to just replace a knee, like it's no big deal. I’ve got to get a new tire, I’ve got to get a new knee, and then go run around on that new knee for 20 years. The drive is to get replaceable parts and to make them easy to install. Quite literally, the delivery, and the need to make them last forever, are driving the need to understand surface finish, and are coming face-to-face with tribology to optimize wear, the surface textures, surface coatings, or even just base material and/or design. The consumer living longer and wanting to drive cars that don't breakdown keeps me in business, I guess.
How does tribology relate to longevity in modern automobiles?
We call warranty reliability, this is a huge issue because the number of parts in a car is enormous. When you think about this, every car that's built is not tested. It's built and it's shipped and you buy it and you expect it to last for hundreds of thousands of miles. Compare that to Bruker lab equipment. We build our microscopes. We test them to death. We are careful about assembling them. We ship them. We build them back in the field. We're very careful about testing them. After we're happy with them, then we let the customers use them. Our equipment costs hundreds of thousands of dollars. A car costs 30 grand along with all the parts in it. Can you imagine? You just turn the key and you go and you expect it to go forever. That's the difference.
Every component in a car has major engineering behind it — you would not imagine the kind of things I've seen. One of the strangest is the visor. Visors are very important technology and there are people that spend their career pretty much working on the visor in your car. We're looking for the relationship between light and the visor, the feel of that visor, whether that visor makes noise when it moves, whether it stays where you put it. That tribology in itself has made careers for a number of people because the mechanism on a visor has all the tribology you ever want to hear about. You have sliding surfaces. You want a certain amount of friction. You want the friction to not make any noise when it moves. You want it to leave it in the position where you place it, and when you're done with it, be able to move it out of the way, and of course it should last for 200,000 to 300,000 miles. And that's just one part of a car. The issue of noise for cars under warranty is enormous. When it comes down to it, most of my time is spent helping people solve problems related to either squeaks, leaks, friction, wear, appearance or adhesion. That's pretty much all the issues that I get involved in. Squeaks are noise. Noise is a phenomenal problem in the auto industry. We take for granted how much we hear. Noises affects our perception of the quality of that car.
What about components wearing out? Can you give an example?
Of course, we don't want things to wear out, so we must study wear. Probably one of the more interesting applications of wear is in sensors. Our cars are filled with sensors and as we move more and more to this electrification of the automobile and the internet of things, we have sensors everywhere. Sensors are usually involved in something moving relative to something else. They can be very basic, like a little mechanical object sliding against the resistor, to more advanced, like MEMS devices with different structures on them. They're still moving and we're still worrying about friction, but on the nanoscale. Once again, it's all about friction and it's all about wear; how these things wear out because as the sensor wears, unfortunately, it will give us a false signal.
That brings me to a case that I worked on years ago. One of the car manufacturers had a very major recall because their cars were running out of gas, and these were brand new very expensive cars. Customers were driving down the highway and the gas tank would read a half tank, and all of a sudden, the car would stop and they couldn't understand what happened. It turned out the sensor was failing. It was telling them they had gas when they didn't. But when you run out of gas in the middle of a highway at 70 miles per hour, it's not a good thing and the government gets involved. I walked into a meeting with the NTSA people and everyone was screaming at each other to try and get to the bottom of the problem. It turned out there were a lot of issues, people were blaming it on the gasoline affecting the sensor and the sensor manufacturing. The gas tanks in those days were moving over from steel to plastic so they also thought the plastic was causing problems. It was a serious recall project and that was the first one I really cut my teeth on. I was able to see when the big leagues get involved how much they throw at a problem. It came down to a wear issue, and the sensor was wearing out prematurely. It took a lot to solve the problem, including literally building brand new cars off the line with sensors of different designs and then driving them around town on these special courses 24 hours a day, taking the car apart after every 5,000 miles and analyzing the sensor. This is the kind of stuff that goes on in Detroit day in and day out, and most people don't realize.
People are living longer and need medical devices that will last 20 years, how has tribology contributed?
In the medical field, a lot of issues with friction come up. This is phenomenal stuff when you think about it. In the last, say, 50 years, the amount of what we call non-invasive surgery that goes on instead of opening them up and getting inside their heart has radically increased. They actually feed catheters through your arteries. Well, that's a big challenge from a tribology point of view. They take a very thin wire and they feed that wire through your arterial system. That wire has a very smooth surface finish, as well as other characteristics. I've seen this and this blows you away. It's not like our arterial system is one straight tube, it's a very circuitous path. This wire has to go in all kinds of weird directions and not pierce through that artery. Then you get that wire through your body into your heart and that's just a guide wire. Now, you slide a conduit over that wire. All that sliding, that's serious tribology. You want to make sure that there is obviously as little friction as possible, both on the metal guide wire on the inside, if you will, the lumen of that tube, and the exterior, which is sitting on your vessel wall. The actual physics that goes on in development of those surfaces, their surface texture, as well as the chemistry of the material, is phenomenal. The friction coefficients that these guys quote blow you away at how small it is, which as I'm getting older I'm glad to know because I might need these things.
Have you got any other examples where medical devices have got to last a long time?
Okay, a routine problem that happens in the medical industry quite a bit is a particular application where there is an electrode that's used in some kind of electrotherapy device. It's implanted in somebody's body. It might be a heart implant or something, but it's an electrode. The electrode has to have a very particular surface texture on it so that it basically becomes integral to the muscle tissue. For the first phase of this project, we actually experimented with different surface textures and different specifications until the customer figured out what specification they need. Then they go into production. Then yeah, routinely, once a month or once every six weeks, I'll get a series of parts to measure before they release a lot into production. We've kept this history of measurement and data analysis a number of years, so they can tell whether they're drifting or not in their production and correlate that to the performance of the device.
What about joint replacements that might have to last 20 years?
You hear about it all the time in the news where you get recalls in the implant industry. A good example might be a hip implant. All of a sudden, the hip implant material is not bonding well to the bone and it becomes loose, and that's not a good thing. A lot of times, that relates to the basic surface roughness of the part, and there's a spec again on the surface texture. It is usually a pretty straightforward measurement. Give me a good part, give me a bad part. Only need two. If they're really, really good and really, really bad, I only need two. Then you make a measurement of those. It's usually pretty obvious that one's not the right texture. Again, they might have met a spec but the spec was just improperly developed and then you start to get into lawsuits.
Are the FDA involved in these medical device issues?
Yes, with medical devices, it's always going to be the case. A lot of materials are polymeric materials used in different devices, a lot of plastics in the body. A company will go through the development process and they will determine a measurement protocol for that material, and that gets published with the FDA when they get approval for their device. Then they have a way of going back and saying, "Okay. This is the surface roughness and here's how it's measured for this particular device." They have to do that and they will prove it, and then over time, they monitor it to make sure they're meeting their spec.
Going back to cars. What is the future for the automotive industry from a tribology perspective?
The result of all this transportation stuff, it really comes down to material science, and that's where Bruker fits in, in understanding and helping optimize material science. Where the industry is going and why it cycles of course is because of the economics. Not everyone buys a new car every year and like I say, we're trying to make cars last forever. As we drive more and more towards safer driving, which I think is probably the key issue, we are heading into a new whole world of electrification and smart cars. I'm starting to see people who used to be material scientists and they're still material scientists but their business card says “material science electrification.” They're involved in the materials of electrification. That could be anything from the batteries to the motors to whatever because it’s clear we're moving towards an electric vehicle. Someday just as mechanical watches have been superseded, we're going to have electric cars, and that makes a lot of sense. When the fundamental problems in electric cars are solved, basically the range, battery storage and all that, it makes the most sense in the world to have electric cars.
I don't know if you've ever seen these stats, but if you look at a mechanical car, everyone is crazy to get to 60 miles per hour in four seconds. A Tesla does this in two and a half seconds right out of the shop. This is part of being a direct drive car. You've cut the acceleration in half and made that powertrain totally different. We can't beat that. There is no doubt we're going electrical. Along with electrification there's going to be a lot of material challenges. The battery storage issues we see a big application there. The other thing that's happening big time in the auto industry, which I'm very excited about along the lines of electrification is more the internet of things concept. The idea that our cars are getting so smart now with artificial intelligence is mind-blowing. This means the autonomous vehicle everyone is talking about is very close. Driving a car is going to become very safe. That's very exciting to me.
The idea that our cars are already talking to each other on the road to avoid accidents, the amount of money and lives that will be saved is a very exciting development. Imagine a day where we don't have too much mechanics in the car. I mean if we think about how crazy the car is today, it's been so highly engineered it's phenomenal. You start with this simple, internal combustion engine with a piston and a ring and the thing slides up and down and it connects to connecting rods, which connect the push rods and you got all these little mechanical things going on, it seems like a mess. In order to optimize that it has taken 150 years, and the mechanical engineering and the material science involved is phenomenal. Now we have electronics to control all this mechanical gadgetry, get into transmission and forget about it. Then of course the alternative is you just replace it with some electric motors, direct drive right on the wheels so no transmission and less moving parts. We are heading towards electric cars. I think there's no doubt, I just don't know when, and economically it will take a while but we're going to get to that electrification and that will again drive materials studies and testing. What we're finding is that the majority of cost of build materials for a car is electronics. When you think about all the electronics and how many processors are in a car, how many sensors are in a car, it all comes back to Silicon Valley technology.
Learn about the instruments in Don’s Lab
About Donald K. Cohen Ph.D
Dr. Cohen has an undergraduate degree in Physics from the University of Michigan – Dearborn and graduate degrees in Physics and Optical Sciences from the University of Arizona. Early in his career, Dr. Cohen worked with IBM on optical disk drive development. He later joined WYKO Corporation as Product Manger and finally Vice President, developing 3D surface texture metrology instrumentation. In 1994, Dr. Cohen established Michigan Metrology,LLC to help engineers and scientist solve problems related to “leaks, squeaks, friction, wear, appearance, adhesion and other issues”, using 3D Surface MicroTexture Measurement and Analysis.
Disclaimer: The views expressed here are those of the interviewee and do not necessarily represent the views of AZoM.com Limited (T/A) AZoNetwork, the owner and operator of this website. This disclaimer forms part of the Terms and Conditions of use of this website.