Firms dealing with advanced composite materials, such as fiberglass or carbon fiber reinforced pre-preg, have the chance to optimize their research and development and quality control/quality assurance functions while helping to ensure the reliability of finished components at the same time. Instead of relying on laborious, off-line laboratory testing, companies can leverage dielectric cure monitoring solutions to monitor cure in situ and in real-time.
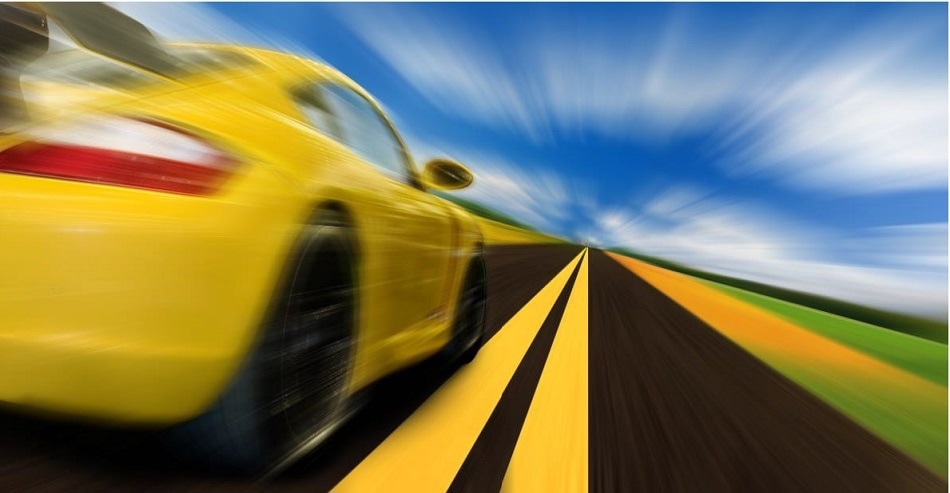
Modern automotive components: made possible with advanced composite materials.
Dielectric cure monitoring is the only mature testing method that enables users to obtain critical data on curing thermosets in real time, over the course of the entire cure. Dielectric cure monitoring, also referred to as dielectric analysis (DEA), can speed up R&D processes by eradicating the need for more time-consuming and less precise forms of testing.
It can also speed up the transition from R&D to quality control and quality assurance by providing QA/QC teams with solid data which they can base their work upon — helping to guarantee the reliability of completed products.
The Problem: Poor Visibility into Cure State
Manufacturers of advanced composite materials, and organizations that use these materials in end products, share the challenge of how to determine when the degree of material cure meets pre-set requirements.
Nowadays, most organizations view optimization of cure as a research and development function. Companies often approach this process by curing samples at various pre-defined temperatures and comparing the outcomes as part of the R&D process.
Armed with the data they gather from these efforts, R&D teams can collaborate with quality assurance and quality control experts to establish how to achieve specific results in material cure. This ensures that finished parts will meet specifications.
However for many companies, meeting particular specifications for material cure remains an inexact and error-prone process. In the absence of methods that examine cure in real time, labor-intensive laboratory testing, such as dynamic mechanical analysis (DMA) or differential scanning calorimetry (DSC),must be performed. This work involves repeatedly stopping and restarting the cure process to determine how long it takes for the material to cure at a given temperature. This adds needless delays to the development process.
For example, a company may want to develop a process to complete the cure of a sheet molding compound (SMC) part in less than three minutes. Its R&D group would define the ideal characteristics of the end product in terms of strength, toughness, surface finish, rigidity, or other properties. Then the team might cure the material for a set amount of time, stop the cure, and perform laboratory tests such as DSC or DMA to determine the degree of cure after a given amount of time at a given temperature. Once this is complete, curing can resume.
This process has to be repeated numerous times to gain enough data to determine whether finished parts made with the material will perform as expected. Materials left to cure too long could become brittle; those taken out too soon may not be strong enough to meet specifications.
Either way, manufacturing throughput and efficiency are reduced. There is also the potential for significant wasted expenditures, both in terms of energy and equipment usage, if thermosets are cured longer than needed.
Companies working with advanced composite materials, such as fiberglass or carbon fiber reinforced pre-preg, can optimize both their R&D and QA/QC functions while at the same time helping to ensure the reliability of finished components. Rather than depending on on laborious, off-line laboratory testing, companies can leverage dielectric cure monitoring solutions to monitor cure in situ and in real time.
The Solution: A Simpler, More Precise Cure Monitoring Method

The cure of thermosetting materials can be easily measured with dielectric analysis.
Dielectric cure monitoring is widely used in the manufacture of SMC, epoxy molding compound (EMC) and bulk molding compound (BMC) to characterize curing behavior. By measuring the cure of the sample under actual processing conditions, the material quality can be determined before it is used in production.
Likewise, out-of-spec material can be soon identified and corrections can be made to the manufacturing process before additional material is produced. Testing can also be done on raw material paste prior to moving on to further steps in the compounding process. DEA can also be used for process development, process monitoring, and automated process control of production molding operations.
A single test done during the curing process offers exact details on rate of cure with dielectric cure monitoring. For example, an SMC maker must guarantee customers that cure can be completed to specifications in a pre-defined amount of time. With dielectric cure monitoring, there’s no guessing—the company will know for sure. The same test can be effortlessly repeated for every individual batch without slowing down manufacturing.
With this information, QA/QC teams can confirm that materials will perform as expected when cured at a certain temperature. This is critical for SMC makers, whose materials are used to make automotive and marine components. Why?
This is because the SMC may degrade between the time it leaves the manufacturer and the time it is used by, for example, an auto maker to make parts. It may age prematurely from storage at elevated temperature or styrene in the resin can evaporate while it sits on the shelf, affecting cure time— as well as the quality of the finished part.
In fact, the end quality of parts fabricated from thermosetting resins, compounds, and pre-pregs can be drastically affected by both batch-to-batch material variability and by the change in characteristics brought about as materials age.
Dielectric Cure Monitoring: How it Works
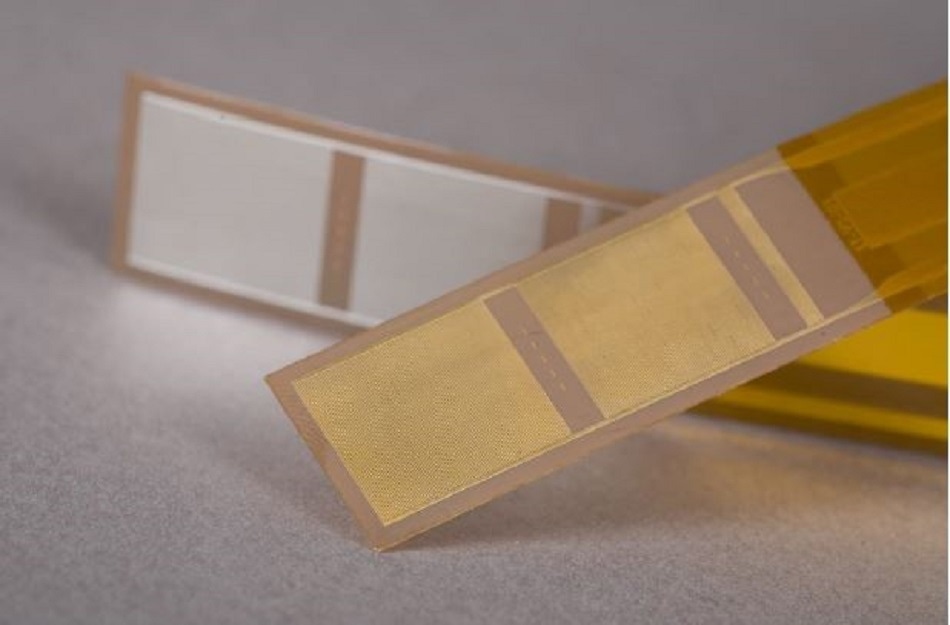
Detailed view of dielectric sensors.
Dielectric analysis is a method for investigating the processing behavior and physical and chemical structure of polymers via the measurement of their electrical properties. One advantage of dielectric analysis is that it allows material tests in a wide variety of conditions, in the laboratory, at the QA/QC bench, or on the manufacturing floor. No other technique has this versatility.
Dielectric cure monitoring can be performed in an oven, on a hot plate, in a press or mold, in an autoclave or in an actual part being developed or manufactured. When embedded in a part or a large mass of material, the dielectric sensor can directly measure the effect of an exotherm on the rate of cure.
However, DMA is confined to a laboratory. If the sample is liquid, it must be tested in a special cell or impregnated in a matrix of some kind. If the sample is solid, it has to be prepared with a specific geometric configuration. DSC is similarly limited to a laboratory, and the sample confined to a tiny DSC pan.
During the production of composites, parts are typically cured using a fixed recipe for temperature and time. This process can be compared to baking a cake at 175°C for 30 minutes — at the end of that time the cake might or might not be done. The baker must stick a toothpick into the cake to test it. If it is not done, then it has to stay in the oven and be tested again later. If testing the cake isn’t possible, the only option is to bake it longer, maybe for 60 minutes — but then it might burn.
Dielectric cure monitoring is now most often used to confirm that parts are made consistently. For example, the nominal cure of an automobile body panel made of SMC might look like Figure 1.
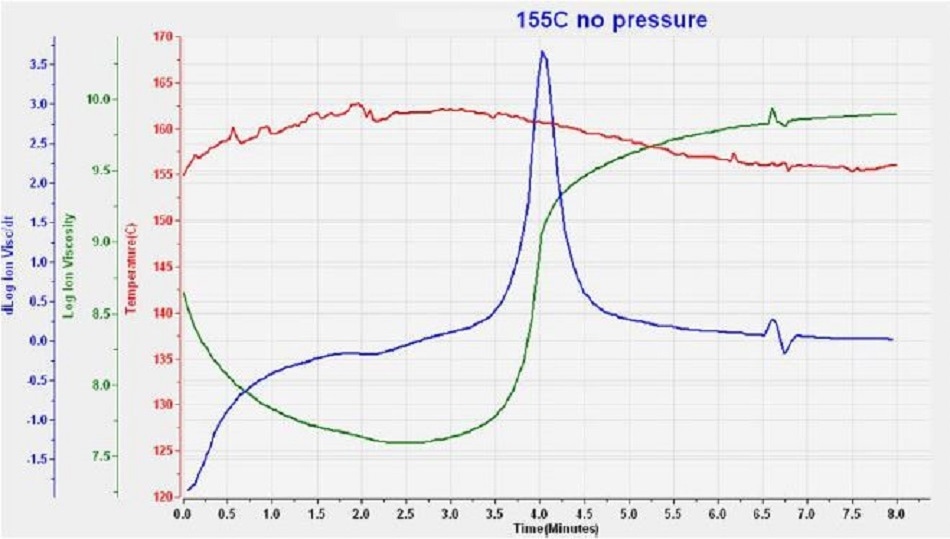
Figure 1. Typical dielectric cure data for sheet molding compound.
The cure of every panel can be compared with a nominal profile. Results for each panel can be noted for statistical quality control. Deviations beyond defined limits show that something in the curing process has drifted and information from the cure is available to correct the problem. In this way, part quality is guaranteed.
For extremely critical parts such as composite aircraft or spacecraft components, every step in the manufacturing process is documented, both to record that the part is made according to specification and for analysis in the event of failure. Many manufacturers record temperature of the part as a very indirect and inaccurate way to infer the progress of cure.
Dielectric cure monitoring is a sensitive probe of cure state. So dielectric cure monitoring is valuable for documentation as no other method can observe cure state in manufacturing and in real time.
Productivity in manufacturing can benefit most immediately from dielectric cure monitoring, especially for high value components like wind turbine blades. These blades, often more than 50 meters long, are made in a mold. The thickness of the blade, which affects the exotherm, and the rate of cure both vary along its length.
Manufacturers use experience and guesswork to determine cure time before removing the blade from its mold. However removing a blade too soon can cause cracks because the blade is not stiff enough, and removing it later than needed reduces throughput.
Dielectric sensors can be installed in the mold at strategic locations, or perhaps every five meters along its length. Dielectric cure monitoring can determine when cure along the entire part has reached a desired point, and only at that time would the wind turbine blade be demolded. Because of this improved efficiency, if a factory ships even as few as one or two additional blades a week, profitability increases.
Conclusion
Dielectric analysis is an important and effective testing method that is very sensitive to the curing behavior of thermosetting materials. The availability of reusable sensors and low-cost instrumentation make dielectric analysis a cost-effective method for routine QA/QC testing of thermosetting materials.
With dielectric cure monitoring, the time and effort required to obtain comprehensive, accurate data about cure is much less than with traditional laboratory methods. This means your organization can save money, save time and stop guessing.
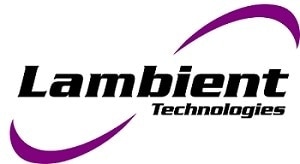
This information has been sourced, reviewed and adapted from materials provided by Lambient Technologies.
For more information on this source, please visit Lambient Technologies.