.jpg)
Gears keep the world moving. Available in a variety of shapes and made from a wide range of materials, gears are found absolutely everywhere. From the tiniest and most delicate gears used by watchmakers, to gears with a diameter of 16 meters used in mines and the cement industry, where they drive rotary kilns and gigantic mills. Whether small or big, they all have one thing in common: they must fulfill the most demanding requirements.
A company called KOEPFER, who has years of success in the gear cutting field, has proven its capabilities in a huge number of projects for a broad clientele. The second nature for the company's gear cutting experts is to satisfy the most demanding requirements. Technology used in the novel modular hobbing machine VL 4 H is the experts’ answer to the demands of high-volume manufacturing.
VL 4 H – A Modular Machine from EMAG
EMAG's modular machines are part of a successful machine series that integrates the different technologies of the EMAG Group on a standardized machine base. Whether for grinding, turning, gear cutting, or induction hardening, the proven EMAG pick-up principle guarantees efficient and highly automated production. Incorporated into each modular machine, the pick-up automation system features a parts storage unit for blanks and finished parts from which the machine is automatically loaded. This system enables very short chip-to-chip times of only a few seconds. The machine’s vertical construction not only ensures a perfect chip flow, but also prevents the formation of chip clusters, thus contributing to a consistently high quality of production.
Thanks to the compact vertical design, the machines look very attractive, both as single units and as part of an interlinked manufacturing solution. The interlinking option can be easily implemented as the transfer height between the automation systems of individual machines is consistent. Additionally, the separate energy container enables the use of the new EMAG TrackMotion automation system, which is specially developed for modular machines. The automation system located directly behind the machining area not only transports the parts but also functions as a flip-over unit, which increases the flexibility of the whole system.
Gear Hobbing and Chamfering on a Single Machine
The vertical VL 4 H hobbing machine can be configured for an extensive range of applications. The high-performance drives employed in the hob and the working spindle allow high speeds and torques, ensuring precise, fast and cost-optimized gear production. The machine permits the dry gear hobbing of work pieces up to 200 mm in diameter and module 4. By adding a sensor system for positioning, the optional measuring system for part alignment can be easily expanded. It is installed outside the machining area where it is protected from dirt and chips; it can also be extended and retracted as needed. This permits to make adjustments to the machining operations at any time and also enables seamless documentation for production quality assurance.
As the machining area of the VL 4 H is easily accessible through the large front door, it enables rapid set up times and creates an ergonomic work environment for the operator. The combination of the generously dimensioned machining area, powerful drives, tool clamping, and a working spindle that can be controlled with absolute precision enables various different gear cutting methods to be employed on the machine. For example, the CHAMFER CUT method can be employed to chamfer the work pieces directly after hobbing, with a single clamping operation. In order to carry out this, the CHAMFER CUT tool is mounted on the hob arbor of the cutter in addition to the hob. Developed by FETTE, the CHAMFER CUT method is perfect for precise and low-cost chamfering processes.
As this method does not produce any secondary burr and does not warp the material, it is especially useful for gear teeth that are honed after hardening.
Jörg Lohmann, Head of Sales, EMAG KOEPFER
In order to be effective, the workpiece needs to have a suitable shape. “We have successfully tested this machining combination in the manufacture of gears. The wheel-shaped workpieces have hardly any interfering contours, so that chamfering with CHAMFER-CUT is possible. The machining combination of hobbing and chamfering in a single clamping operation, on one machine is a very cost-effective solution for the user, as two manufacturing processes can be carried out at the same time with just one machine, and the workpiece handling between the processing steps is also eliminated. That lets you reduce your floor to floor times and get workpieces to the next production step faster,” Lohmann explained.
VL 4 H – High Degree of Freedom for the User
The latest VL 4 H from EMAG KOEPFER provides a host of possibilities to users. As demonstrated in the example, it can be used as a standalone machine for combined hobbing/chamfering, or for gear cutting. This machine can also be part of a production line, which is easy to do thanks to the advantages of EMAG's modular machines. In all aspects, the user benefits from the many possibilities that are provided by the machine.
At KOEPFER, we place a tremendous amount of value on giving our customers the optimal advice. With the VL 4 H we have now added another valuable module to our standard modular machine series, which allows us to offer our customers the best possible manufacturing solution for their application, all the way from standalone machines to highly automated manufacturing systems for large-scale production.
Jörg Lohmann
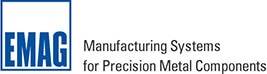
This information has been sourced, reviewed and adapted from materials provided by EMAG LLC USA.
For more information on this source, please visit EMAG LLC USA.
Gear Hobbing and Chamfering on a Single Machine