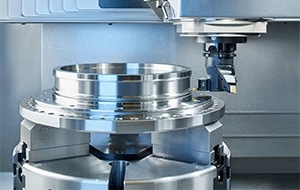
The commercial vehicles market has been experiencing continuous expansion recently, particularly in Europe. The industry association ACEA estimates that around 2.08 million new buses, vans, and trucks were approved in the EU in the past year. This represents more than 12% growth from the previous year. Especially, demand for heavy vehicles, weighing over 16 metric tons, was quite high. However, where manufacturers are concerned, this positive advancement goes hand in hand with a rising technological challenge.
The customers are demanding mobility solutions that are more precisely suited to their areas of operation. For instance, more efficient traditional drives and alternative drive systems are both becoming more and more essential. The indirect outcome is that product cycles in production are becoming progressively shorter; in several plants, the number of part families being manufactured is also increasing. The example of the VMC 450 MT illustrates the implications for the manufacturing technology used. This vertical turning/milling center from EMAG Leipzig Maschinenfabrik offers an unmatched level of versatility. A wide range of huge and complex chucked parts can be machined on it in rapid alternation — enabled by keeping setup work to a minimum.
Presently, commercial vehicle manufacturers are encountering various extremely different challenges: demands by policy makers for lower CO2 exhaust emissions, innovative vehicle technologies, and rising sales figures. Consequently, the production situation in many companies has been transforming for many years now. For each engine model, the market cycle has been getting shorter (and each new model brings new part families that have to be machined on the same machines as before), while simultaneously the number of parts that must be produced in parallel is growing. Where machine users are concerned, this means the production systems need to be set up faster for new parts. This leads to an increase in the total amount of preparation work and a decline in the overall equipment effectiveness.
This is why we've been seeing our customers make a transition in recent years. The trend in commercial vehicle manufacture is moving away from rigid production lines. Instead users are looking for highly flexible solutions that can be set up quickly for many different parts and then provide results with consistently perfect quality.
Georg Händel, Manager of Heavy Parts Technical Sales, EMAG Leipzig
Growing Success on the Market
As a result, high quality, minimum idle times, and maximum flexibility were significant priorities for EMAG Leipzig when developing the VMC MT series. These universal turning/milling centers for machining large chucked parts weighing up to 500 kilograms and measuring 600 millimeters in diameter have evidently enjoyed growing success since their introduction on the market in 2013 and have been used by both supplier companies and OEMs.
Large hubs, planet carriers, differentials of commercial vehicles, agricultural machinery, and brake components, to provide just a few examples, can be machined rapidly and efficiently on the machines in the VMC MT series. Why exactly are a growing number of customers opting for this solution? “With these machines, we have been able to optimize all critical productivity factors to the utmost extent. This combination is extremely unusual for the machining of large chucked parts. What's more, the machines can be configured precisely for nearly any requirement. Not surprisingly, that wins over the customers,” Händel said, referring to the key features of the EMAG design:
- The VMC MT series is basically a classic turning machine with a remarkably powerful main spindle with direct drive — the ideal basis for high precision heavy machining.
- The powerful turning/milling spindle is also directly driven. It can be used for milling, drilling, and turning procedures in addition to multifunctional technologies.
- The tool magazine has up to 80 tool posts. That, along with the integrated tool management system, enables customers to prepare the machine for a range of different parts and also to place many twin tools in the magazine, which are then instantly available for the automatic tool changer if one of the tools in use wears out. The tool magazine can also be restocked during operation.
- The machine has a large side door for automated workpiece loading, which can be done using a gantry or a robot, according to the customer's preference. Manual loading for smaller batch sizes or for setup is done through the front loading door.
- There are several complementary measuring systems for end-to-end quality management. For example, a radio transmission probe checks the quality of the workpieces, while a laser measuring bridge checks the quality of the tools.
- The overall design of the VMC series is aimed at achieving a minimum footprint, ease of maintenance, and maximum overall equipment effectiveness.
Tailor-Made Solutions for the Customer
This combination really comes into its own, particularly with complex parts. Consider planet carriers: The part is machined in two operations (OP 10 and OP 20) with a total of up to 15 different tools. Two VMC 450 MT machines, which are interlinked using a robot, are used for this. “FLEXline” is the name given to this entire system by the design engineers at EMAG Leipzig. A vital benefit of this system is that the two machines are used in parallel and are independent of each other. The completed parts from OP 10 are positioned in intermediate storage within the FLEXline.
This deliberately creates a parts buffer which guarantees that the FLEXline as a whole continues to produce even if the OP 20 machining of the total batch takes slightly longer than the OP 10 machining. This enables the idle OP 10 machine to be set up for a new workpiece without halting the process.
This ultimately reduces the downtime of the FLEXline to zero during a batch change.
Georg Händel
Proven EMAG technology brings additional increases in productivity. For example, the highly dynamic axes with their short travel distances also reduce non-productive time and accelerate the production processes.
Universality Increases Market Potential
High machining quality, low non-productive times, quick part changes—with these advantages, the experts at EMAG Leipzig see a significant market potential for their machines.
The VMC MT can be used for both prototype manufacture and full-scale commercial production in the range of 60,000 to 80,000 units per year.
Georg Händel
Händel added, “In either case it offers users a whole new level of efficiency in the machining of large chucked parts. And ‘24/7’ and ‘Industry 4.0’ are not foreign to the designers of the machines, but rather clear objectives for the EMAG FLEXline. That is advantageous for manufacturers of agricultural machinery, the aerospace industry, and machinery manufacturers in general. For us there's no doubt: the flexibility and universality of the VMC MT series will continue to gain more and more favor in the market.”
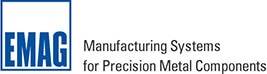
This information has been sourced, reviewed and adapted from materials provided by EMAG LLC USA.
For more information on this source, please visit EMAG LLC USA.
Universal Solution for Large Chucked Parts

The quality of the workpieces is checked by a radio transmission probe

The VMC 450 MT Turn/Mill Machine from EMAG: the specialist engineers develop specific manufacturing scenarios for different workpieces—from a manually loaded stand-alone machine to the “FLEXline” with multiple interlinked machines.

View of machining in the machine's interior: the process features high precision and short idle times.

For end-to-end quality management, there are several complementary measuring systems. For instance, the quality of the workpieces is checked by a radio transmission probe, and the quality of the tools by a laser measuring bridge.

Loading can be done manually, with TrackMotion using a robot, or with a gantry.