As anyone who has ever participated in a presentation on thermoplastic composites could tell, recyclability is one of the advantages of thermoplastic composites when compared to their thermoset counterparts.
However, they do not find many real world applications, even though the process in essence — that is, grinding the materials down and applying pressure and heat to make parts — is not difficult. Toray Advanced Composites is contributing to research efforts seeking to increase the economic and technological value of the recyclate and thus its applicability in real-world applications.
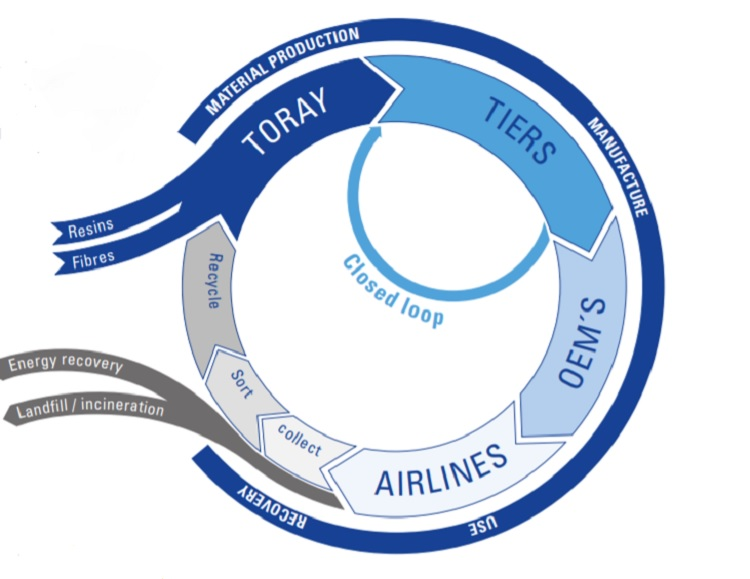
Although the mantra on recycling thermoplastic composites — merely grinding and remolding — is very true, it usually does not make a lot of sense economically. Most often, it is basically a form of downgrading: significantly shortening mechanical properties and fiber length. Toray is taking part and doing research in areas to solve these problems and make the recycling of its materials available and useful to customers. In this case, Toray concentrates on closed-loop recycling with surplus materials that are the result of the value chain as it exists today.
To inspire the industry with the possibilities of thermoplastic materials, Toray chose to spread the knowledge it has gathered with in-house projects. By providing these ideas to the industry, Toray would like to inspire and encourage engineers to keep thinking creatively.
Flow Layer Enhanced Continuous Fiber Laminate
A new format of reinforced thermoplastic laminate has been developed by Toray Advanced Composites that incorporates recycled materials and provides design and processability advantages. Toray's internal Research & Product Development department undertook this research in association with multiple graduate students who utilize this platform for their ongoing research projects.
This development is a novel material format of continuous carbon fiber reinforced thermoplastic laminates that are improved with a flow layer of discontinuous fiber, either from recycled or virgin thermoplastic composites. This construction allows designers of composite components to include more intricate features and gain from the optimized material performance of continuous fiber-reinforced laminates. This allows them to maintain a stamp forming process that is both robust and cost-efficient.
.jpg)
The enabled features cover local strengthening and edge sealing, or stiffening of the part, stiffening ribs, textures, and variable thicknesses are possible as well as local bosses to spread strains caused by fasteners.
.jpg)
Continuous fiber + recycled material core, to utilize properties when needed.
.jpg)
Continuous fiber + recycled material core, to vary material Thickness.
.jpg)
Continuous fiber + recycled material surface, to add texture, stiffening ribs, etc.
A balance is created between supply and demand of recyclate when recycling excess material (for example, nesting surplus and trimmings), and using this material as a flow layer in the end product. The smart part design allows an engineer to near a 100% “buy to fly” ratio, and lower the thickness of the base material laminate required to achieve the preferred performance. In this manner, the blanks can be customized to significantly reduce the amount of material required. The flow layer is made up of a high fiber volume fraction, long fiber reinforced Bulk Molding Compound, which can either be applied on the laminate or can be added locally before the stampforming process. The stampforming process itself is traditional: the laminate can be stampformed to shape in approximately 5-minute thermoforming cycles.
It is possible to radically enhance the mechanical performance of such tailored parts while decreasing part weight. The flow layer allows for the design of stiffening ribs in the flanges and in corners, bearing strength by the addition of bosses around the drilled holes and thickness changes in the base laminates. The inherently good interface between the laminate and reinforcing features optimizes the mechanical performance.
In addition to the obvious advantage of using less material to create a part and decrease weight, this novel way of production allows using the recyclate directly at the source where it is created. As a result, a balance is created between the supply and demand of recyclable materials and restricts the carbon footprint of the recyclate by eliminating scrap transportation. Moreover, it gives a means to a tightly regulated industry, for example, the aircraft industry, to keep on top of material traceability.
Advantages of Recycled Flow Layer Enhanced Laminates
- Improving performance to weight ratio
- Offering better performance to cost ratio
- High potential for improving buy to fly ratio
- Allowing complex composite geometries
- Balanced usage of recycled materials
Conclusion
In this technique, the unparalleled performance of continuous fiber products, either fabric or UD tape reinforced, is combined with the excellent mechanical properties and design freedom of long fiber reinforced bulk molding compound. Tailoring local stiffening, strengthening, as well as functional features can decrease the average thickness of laminate and thereby component weight. Recycling excess material from previous processes in the part as the flow layer possibly increases the degree of utilization of purchased material, the so-called “buy to fly” ratio up to almost 100%.
.jpg)
The traditional stampforming process, which is fast, robust, and cost-efficient, can be used for part manufacture, which means no expensive equipment or tooling investment is required and short cycle times can be maintained.
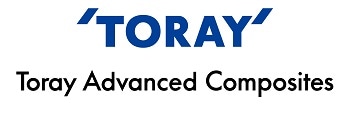
This information has been sourced, reviewed and adapted from materials provided by Toray Advanced Composites.
For more information on this source, please visit Toray Advanced Composites.