Process engineers in one of the Rocky Mountain states were concerned about detecting the release of hydrogen fluoride (HF) gas at one of their plants. This was part of a series of upgrades within the plant and looked at the accidental release of HF gas. For those who don’t know, HF is a common catalyst within petroleum refining alkylation processes for the production of octane-boosting additives in gasoline products.
The engineers take great pride in their local community and the petroleum refinery is located near a major city that is considered to be a regional hub for its affluent economy, including oil and gas production and refining.
Maintaining a safe working environment is considered to be a priority for the process engineers who work there. The presence of toxic, flammable and combustible gases requires the plant to utilize very reliable safety monitoring equipment with advanced sensor technologies.
The refinery has a crude oil capacity of more than 50 Mbpd, and crude oil is either sourced from local suppliers or via a pipeline from Canada. The plants refined products are primarily distributed to the eastern slopes of the Rocky Mountain region, including Denver, Eastern Wyoming and Western Nebraksa.
.jpg)
Figure 1. The potential presence of hazardous toxic, flammable and combustible gases requires to employ a highly reliable safety monitoring system.
The Problem
Alkylation is a conversion reaction that forms alkylates from isobutanes and is often performed in many refineries for use as octane-boosting additives in gasoline. The process requires a strong acid to act as the catalyst. In the case of this refinery, and many others, the catalyst of choice is HF.
HF poses two safety hazards in these processes. The first, is that large amounts of hydrocarbons are processed, which are both flammable and explosive. The second is through the accidental release of HF, which can then form HF gas clouds and pose a threat to both the employees and the local community.
The US Occupational Safety and Health Administration (OSHA) and the Environmental Protection Agency (EPA) regard HF to be a highly toxic chemical. If released into the atmosphere, dense vapor clouds of HF can form that over near land and can travel great distances, especially if it is a windy day. As a strong acid, HF can cause serious burns, as well damage the eyes, skin, nose throat and respiratory system.
The Solution
To help solve the HF gas detection concerns, the plant engineers contacted a manufacturer with the requirement of a highly reliable HF gas monitoring solution, that would also ensure the highest amount of protection with the highest uptime available and no maintenance.
The manufacturer's team recommended gas monitoring system with four individual enhanced laser diode spectroscopy (ELDS) open-path HF gas detection sensors to create a complete detection perimeter around the processing area. The open path gas detector (OPGD) shown in FIG.2 uses ELDS to detect specific toxic and flammable gases. If a leak does occur, the sensor recognizes and analyses the HF (and other) gases’ harmonic fingerprint. This harmonic technology enables precise gas recognition and eliminates the risk of false alarms, even under harsh environmental conditions.
.jpg)
Figure 2. A gas monitoring system composed of four individual enhanced laser diode spectroscopy (ELDS) open-path HF gas detection sensors was recommended to surround the alkylation unit’s processing area.
False alarms are a serious problem for many gas and flame detection technologies, and can result in plant downtime – which often comes with its own complications of extensive investigations and regulatory reporting. False alarms also lead to a lack of confidence from the employees if they happen frequently. This can breed a culture of apathy that may not take any swift measures if there is a real emergency.
Class 1 eye safe lasers in ELDS can penetrate thick fog, heavy rain and snow, which is beyond the capability of conventional open path infrared (OPIR) detectors. With its automated self-checking safety integrity feature, there is no need for the usual OPIR checks and recalibrations, that usually require the need for a qualified technician. The harmonic fingerprint detection also means that ELDS sensors are immune to sensor poisoning and interferent gases.
.jpg)
Figure 3. Multipoint harmonic fingerprint illustration.
The refinery plant engineers reported that the new HF gas detectors were easy to install, commission and operate. They also feature Bluetooth wireless technology and advanced smart diagnostics. No physical intervention is required for interrogation, troubleshooting or for downloading event logs.
With a response time of 3 seconds, ELDS technology provides a quick response to the presence of gaseous HF compared to other detector technologies. ELDS gas detectors also feature separate receivers and transmitters, that are certified for use in explosive atmospheres and detect HF over distances from 5 to 120 meters.
ELDS gas detectors are made of high-grade corrosion resistant 316 stainless steel which helps to ensure longevity in industrial scenarios. Unlike conventional point detectors, HF corrosion is less of a concern because the detector arrangement enables the components to be located away from the high HF concentrations near any potential leak source.
ELDS detectors are suited for onshore, open and enclosed environments, including the cold winter temperatures in the Rocky Mountain region and extreme high temperatures of the Middle East. Heated optics allow for use over a wide temperature range between -67 °F and 140 °F (-55 °C to 60 °C). ELDS detectors are also suitable for use in hazardous areas approved to CSA, UL, Class 1, ATEX, IECEx, EAC and INMETRO standards.
Results
The process engineers at the refinery continued to be satisfied with the performance of the OPGD whilst monitoring HF. No missed events or false alarms have been recorded since the OPGD was installed and set to work. It is appreciated by the engineers, that the detection system requires almost no maintenance and it is expected to provide a high cost saving in terms of operational maintenance, compared to other HF gas detection technologies.
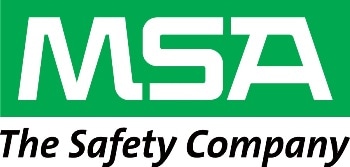
This information has been sourced, reviewed and adapted from materials provided by MSA - The Safety Company.
For more information on this source, please visit MSA - The Safety Company.