Heat can be recovered from compressed air in a cost-effective way provided the various steps are synchronized and the temperature needed for the recovery is achieved in the cooling water discharge. Some situations which use cooling water from heat exchangers are:
- drying of sludge at 40 to 50 °C
- pre-heating of hot water and supply air at 30 to 50 °C
- hot water forward flow at 40 to 60 °C
- building heat forward flow at 60 to 85 °C
The factors which determine the efficiency of heat recovery include:
- Usable temperature: the ΔT between the source of waste heat and the consumer or heat sink must be 5-10 K at the least, and the greater it is, the more efficient the transfer.
- Heat quantity and output: the energy recovered from the heat source must be appropriate for the process which is intended to consume it so that no more heat generators will be required at peak demand.
- Continuous utilization: as long as high capacity utilization is possible, even blower/compressor systems which have a low waste heat output can achieve worthwhile heat recovery.
- Physical distance: the source of waste heat and the heat sink should be positioned as near to each other as is feasible to cut down losses during transport and associated costs.
- Coordination of operating times: if the heat sink and heat source run simultaneously the waste heat can be sucked up as efficiently as possible, but if this cannot be done, a heat accumulator will achieve the purpose better.
- Operating time and service life: the longer the recovery system operates, the greater the cost savings and the better the utilization of the capacity available.
- Investment costs: these are linked to heat transport, heat storage and similar factors.
- Reliable supply: if a workflow depends upon waste heat at a sensitive point, a backup system to generate heat must be put in place to prevent failure in case the waste heat supply is disrupted for any reason.
Methods of Heat Recovery
Exhaust air can be used to heat rooms if it comes from air-cooled blowers, turbo blowers or compressors which have acoustic hoods. The AERZEN unit comes with an exhaust fan fitted on the exhaust air louver so that the cooling air can be used for the compressor stage, the silencer and the pipes under the hood, while the exhaust air from the oil cooler is directed to room heating at the same time. That is, the waste heat which is at about 30 to 60 °C is first concentrated at the exhaust duct, and then allowed to flow into the required rooms via the air ducts. The temperature control of the room is achieved by flaps which move in accordance with specified temperatures. The discharge-side gas pipe can be used still better to recover heat because 85% of its electrical energy is contained as heat. To recover this, a small heat exchanger is set up in the downstream pipeline on the discharge side, down from the compressor.
.jpg)
Image Credit: Aerzen
Wastewater Treatment
In plants that treat wastewater, several types of compressors and blowers are used, including turbos and Delta Hybrid compressors, which result in the air discharge temperature reaching a maximum of 140 °C. This avoids having to use a condensate trap. These plants use the greatest amount of electrical power in cities and municipal areas, which means that they need to look into better energy optimization on an urgent basis in view of the global energy crisis and the looming threat of increasing energy prices in the future.
One possible solution is to use heat exchangers which operate at low differential pressures of less than 30 mbar, thus ensuring that the blower station uses only slightly more, less than 2% of the operating energy, for this process while saving many times as much energy by its use.
Heat recovery systems can also be used to support the sludge drying more efficiently by being designed to ensure that cooling water returns from the heat exchanger at over > 70 °C at the highest heat-transfer rate.
.jpg)
Image Credit: Aerzen
An Annual Load Duration Curve and Partial Load
An annual load duration curve is plotted to help target the highest percentage of heat required while designing a heat recovery system that works well at partial load operation. For instance, the graph is derived from a heating system may have to run at peak capacity only a few hours in the whole year. If the heat recovery system is designed properly to meet 15-25% of power requirement, it can recover 50-75% of the heat required. Each situation must be studied on its own merits.
.jpg)
Operating hours of the consumer per year. Image Credit: Aerzen
Available Heat Quantities
In order to recover an optimal amount of waste heat, the heat available must be quantified. This will depend upon the usable temperature difference, the mass flow, volume flow, available period and the specific heat capacity of the medium used for heat transfer.
Features of the Aftercooler
The aftercooler is designed to transfer heat effectively while not losing pressure significantly. It operates by the flow of compressed medium through the pipes of the cooler, while cooling water flows in other pipes in the opposite direction to provide a counterflow. The pipes are arranged in louver fashion so that heat can be transferred easily from one to the other.
Variants include permanent or removable pipe packs, pipes which are smooth or ribbed, and composition of stainless steel for compressed media at high temperatures while copper/nickel pipes are built to carry seawater.
Some available accessories include a cyclone separator, an automatic condensate drain and kits to fit on a flange or a counter flange.
.jpg)
Aerzen's design tool lets you quickly find the best heat exchanger for your system. Image Credit: Aerzen
Explanations of the Type Designation
.jpg)
.jpg)
Image Credit: Aerzen
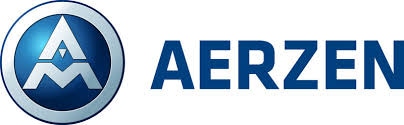
This information has been sourced, reviewed and adapted from materials provided by Aerzener Maschinenfabrik GmbH.
For more information on this source, please visit Aerzener Maschinenfabrik GmbH.