Cement-bound materials are an essential staple of business, industrial or residential buildings, traffic routes, arenas and infrastructure projects. In fact, it would be impossible to imagine contemporary architecture being what it is without these cement-bound materials providing core stability as part of their construction.
As a permanent, versatile binder for plaster, concrete, screed or mortar, cement remains one of the most important and commonly used building materials in the world.
When water is added to cement, it turns into paste. This then hardens through hydration and turns into durable cement stone. Given the importance and centrality of cement to the building industry, cement manufactures face especially important challenges such as assurance of consistent, grade-specific quality as well as energy and resource efficiency.
The main ingredients to cement - and the ones that are responsible for its hardening properties – usually give their name to the different types of cement; for example: Portland cement clinker, pozzolanic cement, granulated slag, burnt shale, fly ashes, silica fume or limestone. As well as these standard cements, each of which has different consistencies, there are a range of more specialized cements for specific applications. These include cements which are fast setting, have high sulfate resistance, low hydration heat or low alkali content.
Grain Size Distributions of Cement and Raw Meal
.png)
.png)
Measuring results Q(x)-SD-diagram: several measurements, reproducibility
The cement’s grain size distribution is the most important aspect of its quality and uniformity, next to the chemical composition of the raw materials themselves. Grain size distribution in this instance is a result of the component’s grinding fineness, and if the cement’s chemical composition remains constant then it is only this grinding fineness that can determine its strength class. That is to say, the higher the grade of fineness, the faster the solidification and the higher the cement’s compressive strength after 28 days.
Additionally, secondary components like ground inorganic or mineral raw materials can improve cement’s physical characteristics due to their specific grain size distribution. The separate grinding of single components, or grinding additives, can improve the cement’s properties in terms of water retention capacity, workability, strength or swelling and shrinkage.
Measuring Results - High Resolution and In Real Time
.png)
Measuring results Q(x)-S-diagram: several measurements with different fine content
.png)
Measuring results Q(t)-diagram with calculated Blaine-values: Trend diagram with characteristic values during type changes from fine to coarse products
Monitoring and controlling the grinding grade is an essential factor in maintaining cement quality and production efficiency. This must be done during the grinding process from raw material to raw meal, and also during fine grinding of burnt clinker with additional core components or additives.
Energy consumption accounts for around half the production cost within the cement industry. This occurs mainly during burning and grinding. Quick and accurate control of cement grinding and material testing means that not only can manufacturers avoid cost and energy intensive overgrinding, but they can also accommodate cement grade changes within a short space of time within one plant, and with minimal amounts of out-of-spec material.
Traditional procedures used for measuring fineness (such as sieving or using the Blaine device to determine the powder’s specific surface) can only deliver single values, even after time-consuming analyses. Laser diffraction analysis however, evaluates the whole grain size distribution in high resolution without the need for operator involvement.
Using laser diffraction, grinding grades, content that is too high, varying content (less than 2 µm) or coarse content can be detected promptly and reliably. Used alongside a powerful dry dispersion, laser diffraction can offer unparalleled sensitivity and reproducibility across the whole range of particle sizes, allowing for user-independent measurements in mere seconds.
Better Particles with Best Instruments
Laser diffraction systems from Sympatec can cover the complete spectrum of particle size analysis within the cement industry. As pioneers in the field of dry particle measurement technology, they are a respected and established leader in the international cement industry, providing a range of product and process specific installations to a wide range of clients.
.jpg)
HELOS/BR with RODOS and VIBRI/L
Dry measurement can offer high sample throughput with minimal preparation of samples and very little cleaning effort. Its use within applications in quality laboratories (off-line), integrated installations within laboratory automations (at-line) or the real time measurement of particle size distribution during grinding and screening (on-line) guarantees the best product quality with prompt intervention in the production process where required.
This, coupled with robust instrument design and professional system maintenance by qualified service staff is key to ensuring that systems can provide quality and value for a long period of time. Whether within internationally operating cement producers or smaller providers of speciality cement products, Sympatec is a leading provider of turnkey ready cement plants and automated laboratory systems, as well as being a leading manufacturer in original equipment for the integrated laser granulometry.
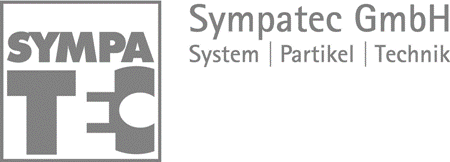
This information has been sourced, reviewed and adapted from materials provided by Sympatec GmbH.
For more information on this source, please visit Sympatec GmbH.