Lactose is a crystalline, white powder that has a slightly sweet taste. It is a disaccharide that is comprised of galactose and glucose, and it is commonly used as an excipient – that is a filler or binder – in the pharmaceutical industry.
In order to manufacture lactose powders, it is necessary to modify the shape, size and size distribution of particles. These particles have special characteristics in terms of flow behavior, compactability and granulability.
Lactose is commonly known as milk sugar as it is a natural carbohydrate constituent of milk. Whey is required to make lactose, and this is generally obtained as a by-product of the cheese manufacturing process. Lactose is made to crystallize by concentrating the whey, and it is then filtered, washed and dried.
Depending on how the lactose is to be used, various levels of raw purity and content may be manufactured. For example, pharmaceutical grade lactose will contain over 99.5 % lactose monohydrate and have an appropriate level of purity.
During the formulation of dry powders for inhalation or oral solid dosage forms, pharmaceutical grade lactose may require a variety of particle size distributions and appropriate modifications. Characteristics like compressibility, flow and granulability of lactose powder will depend on the shape, size and size distribution of the particles themselves.
These particular physical attributes can be adjusted as required using techniques such as milling, sieving, agglomeration or spray-drying in order to ensure that the lactose has the best functional characteristics for granulation, blending or tableting processes.
In order to ensure that the quality of lactose is high; fast and accurate particle size analysis is essential.
Particle Size Distributions of Different Lactose Qualities
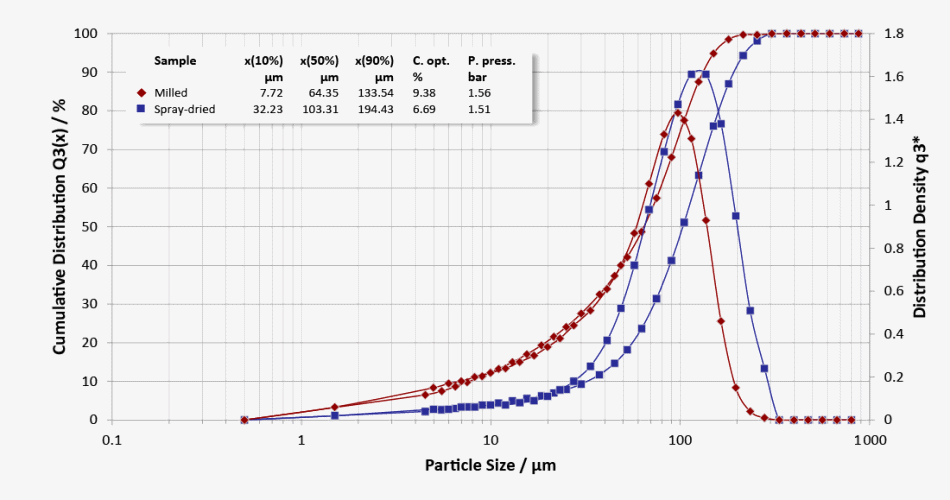
Particle size distributions of milled lactose (red curve: evident fine fraction) and spray-dried lactose (blue curve: narrow distribution)
Better Particles with Best Instruments
Laser diffraction systems like those offered by Sympatec can offer precise, reliable and efficient monitoring of the particle size distribution of all lactose powder products. They can be used for either quality control purposes in a laboratory setting, or in the process itself during high-volume production.
The HELOS sensor combined with the RODOS dry dispersion technology is an ideal solution in these settings and is able to ensure reproducible dispersion of bigger sample qualities, thus obtaining measurement results that are statistically reliable.
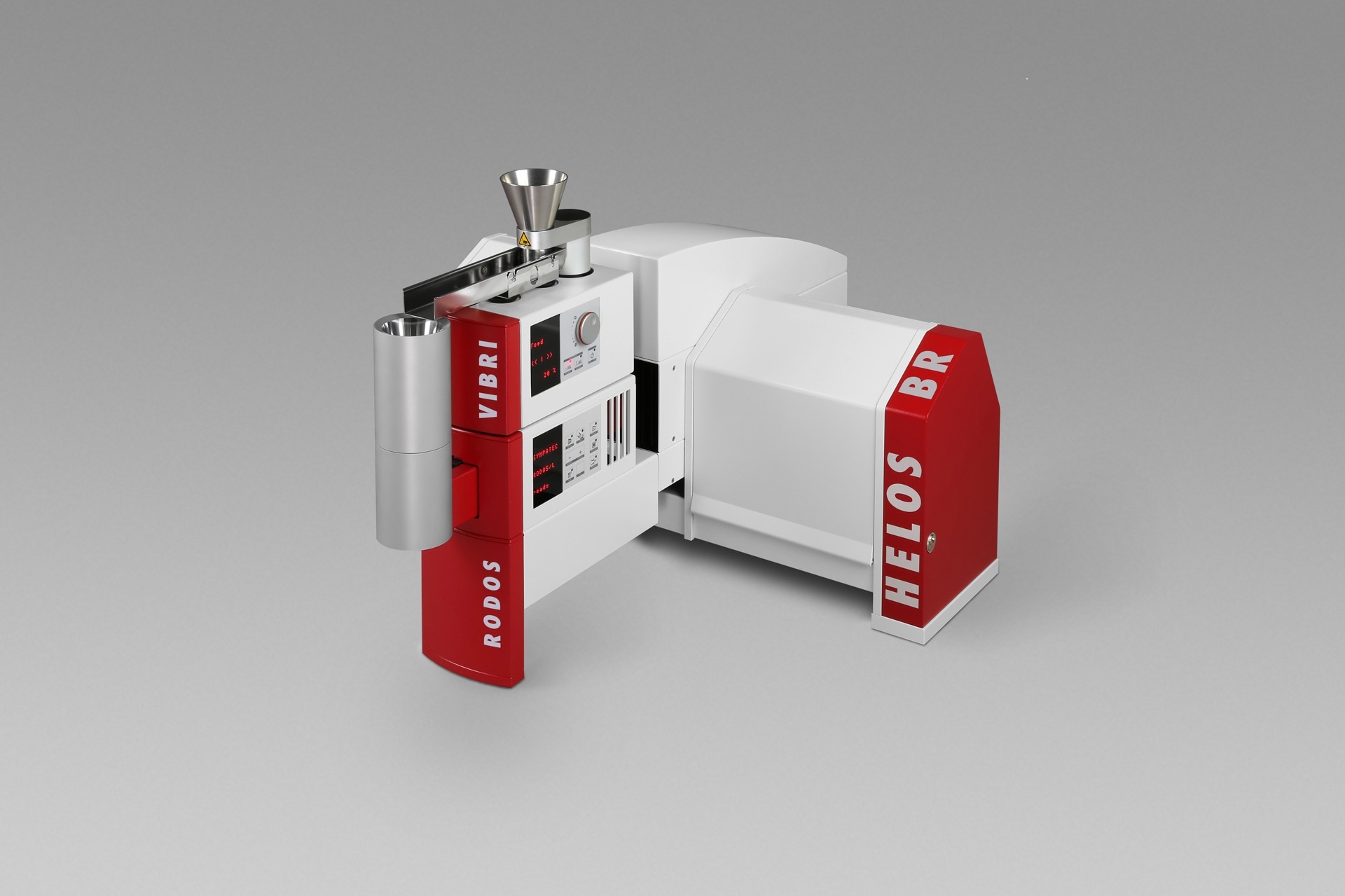
HELOS/BR with RODOS/L and VIBRI/L
This robust, dry method is able to deliver first-class repeatability and comparability of measurement results between systems as well as at production facilities across multiple locations. Furthermore, any measurement methods that have been developed for various product qualities can be transferred to other systems as standard operating procedures (SOP).
All these features combine to ensure consistently high quality and consistency between batches of product. When precision monitoring is used to ensure this consistency, it justifies consumer and business confidence in the premium quality of the products being manufactured.
Repeatability and System-To-System Comparability
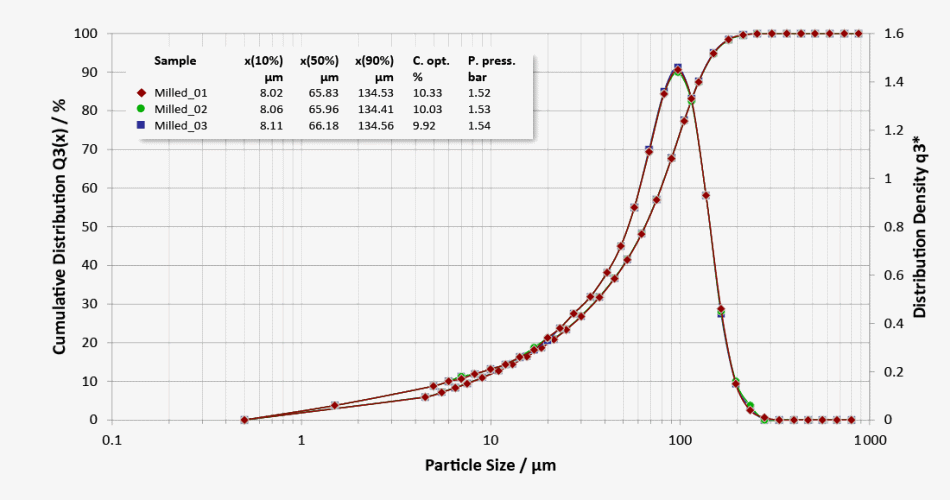
Three repeat measurements of subsamples of a milled lactose with good repeatability
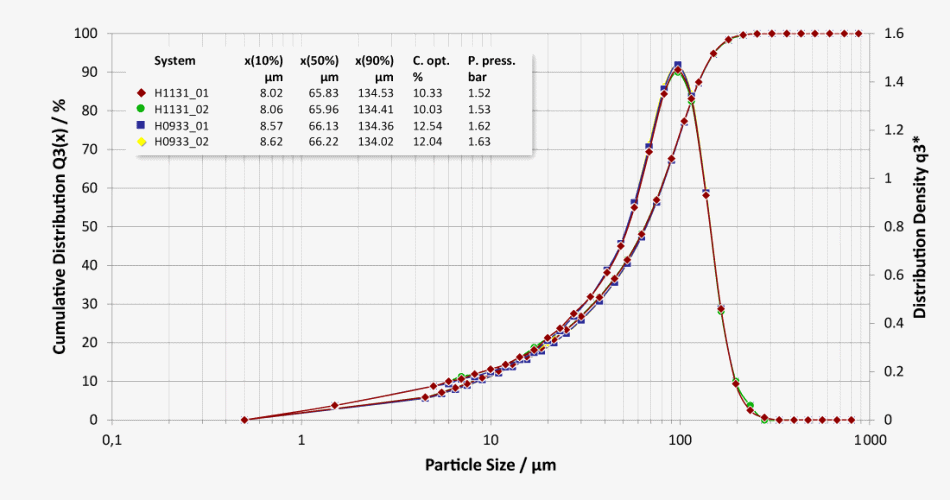
Good system-to-system comparability of a lactose batch measured on two different systems
Fast And Reliable In-Process Quality Control
The laser diffraction systems of the MYTOS family provide in-process control, e.g. during continuous or batch-based micronisation of dry powders. In combination with innovative and representative samplers, we implement in-line and on-line systems which meet GMP requirements and can also be configured for use in explosion-hazard areas (ATEX). Use of the same technologies and identical components in both laboratory and manufacturing process areas guarantee maximum comparability of results when scaling up batch sizes.
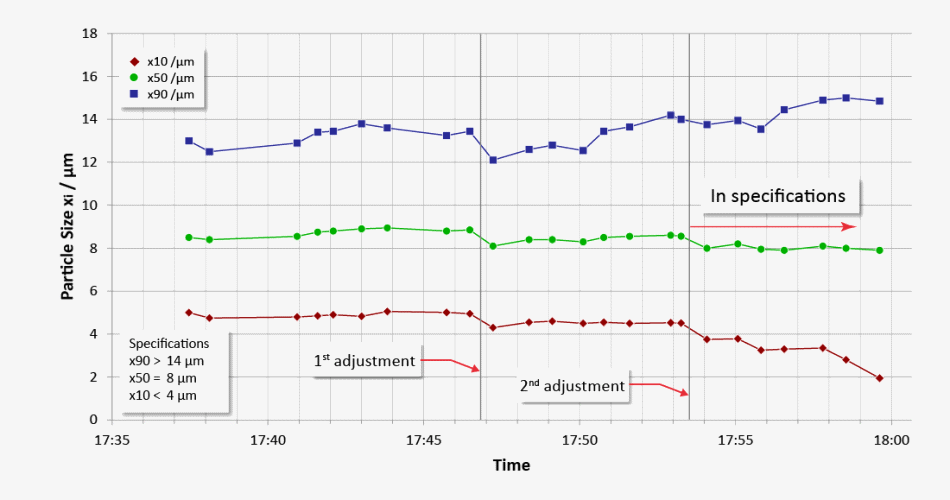
Trend display of critical values (x10, x50, x90) with real-time adaptation of air jet milling in order to satisfy the required specification
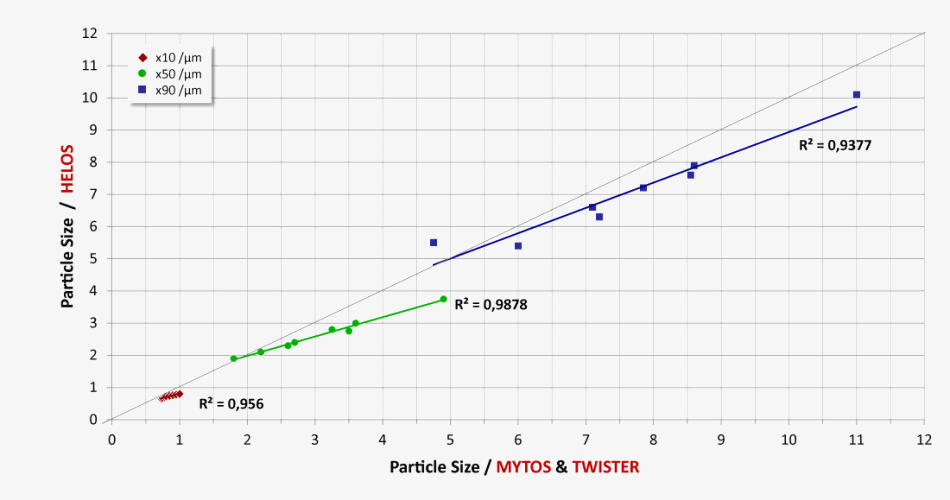
Comparability of MYTOS & TWISTER on-line measurements with HELOS & RODOS particle size analyses in the lab (n=8 different lactose samples)
These teams of experts and the expertise of the company as a whole are trusted not only by manufacturers of pharmaceutical excipients themselves, but also by global pharmaceutical manufacturers, innovative research laboratories and specialists with challenging formulations.
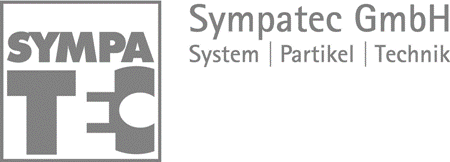
This information has been sourced, reviewed and adapted from materials provided by Sympatec GmbH.
For more information on this source, please visit Sympatec GmbH.