Sponsored by QATMJun 26 2018
.jpg)
Figure 1. Modern Damascus steel knife
Heat treatment originated in the Bronze Age and was developed further for processing iron (blacksmithing) around 800 BC, reaching a first peak with the production of Damascus steel at the start of the 10th century AD (see Figure 1).
Carbon was added to iron to convert it into steel, thus providing the alloy with new properties such as increased hardness. Several iron alloys and different elements have been examined, leading to the development of innovative types of steel appropriate for various applications. One way of altering the properties of steel is heat treatment, for example annealing. Due to the crucial role time plays in this process, temperature-time diagrams have been developed. Today, several temperature-time diagrams have been assessed to produce the best steel for a particular application. These diagrams indicate the correlation between time and heat and the respective structure (martensite, austenite, bainite) of the treated steel. Heat treatment is principally carried out in hardening plants.
Reliable, reproducible, and comparable results are obligatory in hardening shops, since the materials treated are predominantly the same. In order to ensure effective process control, it is necessary to test a large number of samples. Such a high throughput calls for a rapid and simple sample preparation process. Furthermore, the preparation should lead to exceptional sample flatness to guarantee error-free and easy surface inspection.
Materialographic Preparation Process
Due to all these requirements, the preparation method should consist of
- fast and gentle sectioning of samples
- fast mounting yielding plane surface
- fast and gentle grinding/polishing
The use of ATM’s wet abrasive cutting machine Brillant 240 (see Figure 2) provides the benefits of gentle and rapid cutting by selecting the CareCut feature, which minimizes the heat during cutting and maintains the deformation at a low mass. This enables rapid subsequent sample preparation with just a low degree of deformation and minimal or no structural changes.
.jpg)
Figure 2. Wet abrasive cutting machine Brillant 240
ATM’s modular hot mounting press Opal X-Press, when used with Epo black as a mounting compound, fulfills the requirements of optimal edge retention, high throughput, and a plane surface..
Various grinding and polishing techniques can be used for samples from the industrial field. The preparation methods detailed in this article offer a summary of the methods used in this field.
.jpg)
ATM’s modular hot mounting press Opal X-Press
Method 1
This method is a long-established one. The hardness of the heat-treated samples considerably reduces the service life of the SiC Paper, leading to relatively high costs for consumable consumption.
The preparation has been detailed in the table below.
Step |
Medium |
Lubricant/ suspension |
Speed platen |
Direction sample holder |
Single load |
Time |
Grinding |
SiC, P180 |
Water |
300 rpm |
Clockwise |
30 N |
Until plane |
Grinding |
SiC P320 |
Water |
300 rpm |
Clockwise |
30 N |
1:00 min |
Grinding |
SiC P600 |
Water |
300 rpm |
Clockwise |
30 N |
1:00 min |
Grinding |
SiC P1200 |
Water |
300 rpm |
Clockwise |
30 N |
1:00 min |
Polishing |
IOTA |
Dia Complete, 3 μm |
150 rpm |
Clockwise |
30 N |
5:00 min |
Method 2
Planar grinding using a stone provides the benefits of a cost-efficient and rapid preparation. However, investment for a special machine is required. Yet, the overall preparation time is reduced since there is no need to change the SiC papers. Moreover, it is possible to use diamond lapping disks, which have a long service life.
Step |
Medium |
Lubricant/ suspension |
Speed platen |
Direction sample holder |
Single load |
Time |
Grinding |
Stone, P100 |
Water |
fixed |
Clockwise |
30 N |
Until plane |
Pre-polishing |
Galaxy Contero H |
Dia Complete, 9 μm |
150 rpm |
Counter Clockwise |
30 N |
4:00 min |
Polishing |
IOTA |
Dia Complete, 3 μm |
150 rpm |
Clockwise |
30 N |
4:00 min |
To avoid investing in a new machine, diamond grinding disks for planar grinding can be used.These have the benefit of being standard grinding and polishing equipment.
.jpg)
Figure 3. Ferrite-Pearlite, etched with 3% Nital, brightfield 20x
.jpg)
Figure 4. Martenitic structure after heat treatment, etched with 3% Nital, brightfield 20x
Method 3
The Galaxy grinding disk is extremely stiff and thus suitable for producing plane surfaces even if the hardness of the sample surface changes.
Step |
Medium |
Lubricant/ suspension |
Speed platen |
Direction sample holder |
Single load |
Time |
Grinding |
Galaxy red |
Water |
300 rpm |
Clockwise |
30 N |
Until plane |
Pre-polishing |
Galaxy Contero H |
Dia Complete, 9 μm |
150 rpm |
Clockwise |
30 N |
5:00 min |
Polishing |
IOTA |
Dia Complete, 3 μm |
150 rpm |
Clockwise |
30 N |
4:00 min |
Conclusion
In hardening plants, the sample preparation requirements include reliable results, high throughput, and short preparation time, along with superior sample flatness for surface inspections or hardness testing. Sample preparation using SiC paper involves relatively high costs; when a grinding stone is used investment for a special machine is required. The lapping disks method allows for the use of existing machines and a long consumables service life, resulting in optimal cost efficiency and fulfillment of all necessary preparation requirements.
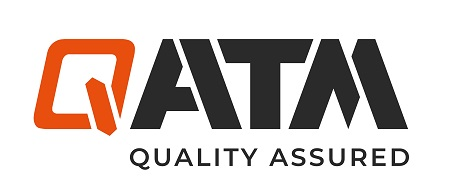
This information has been sourced, reviewed and adapted from materials provided by QATM GmbH.
For more information on this source, please visit QATM GmbH.