Jet engine vibration is arguably the worst enemy of a typical aircraft maintenance team. Parts which are out of balance can eventually result in a cracked turbine, fan, and compressor components, as well as general metal fatigue; and if unchecked, can ultimately lead to catastrophic engine failure.
The total vibration, however, is actually the sum of contributions of vibration from any combination of moving parts within the engine. This makes vibration analysis and balancing extremely complicated. The structural characteristics of individual aircraft only complicate the problem further. The location of the engine on the airframe or the type of engine mount used, for example, can transmit or magnify vibration issues.
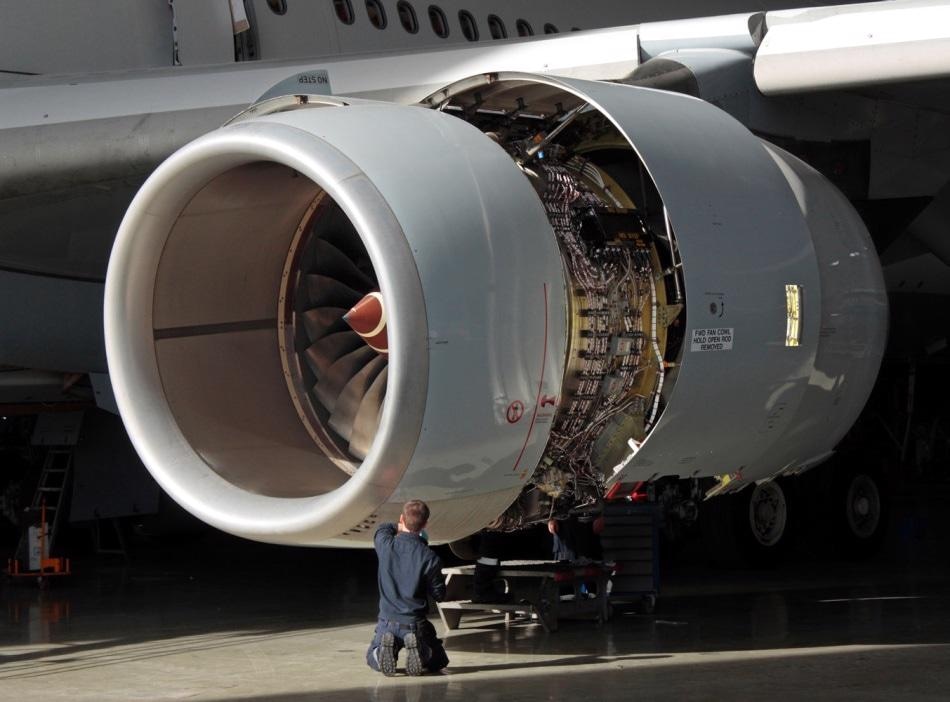
Causes of Engine Vibration
The most common cause of engine vibration is imbalance. If rotating components have an asymmetrical mass distribution, they can impose uneven centrifugal forces resulting in vibration. Sufficient testing may determine that the majority of the vibration content is caused by rotor imbalance, worn parts (e.g. a pump or bearings), or a combination of the two. Equipment from MTI Instruments is used for two main tasks—checking vibration levels and balancing rotors.
Causes of Engine Imbalance
A wide range of causes can result in out-of-balance conditions. Imbalances can be the result of the replacement of rotating engine parts such as fan blades, or from damage resulting from bird strikes or other impacts. Additionally, natural wear and corrosion can also lead to the redistribution of mass over time, and hence engine unbalance.
Engine Vibration Test Schedules
Engine manufacturers specify a schedule of maintenance that must be strictly adhered to for their engines. In addition to this, the FAA will occasionally issue directives related to engine safety. These recommendations and mandates typically include testing requirements and specify allowable limits of engine vibration.
Certain airlines or other aircraft owners may require tougher limits and a stricter schedule than the engine manufacturer. In general, engine testing should be carried out when the schedule requires, following an impact event, or with any increase in the overall vibration level.
Responsibility for the Performance of Engine Vibration Analysis
Aircraft operators are responsible for ensuring the entire aircraft is safe and meets standards. However, commercial airlines typically use one of several options when it comes to engine maintenance. An individual airline may have its own in-house maintenance team, responsible for maintaining the fleet’s aircraft and its engines.
It could also use maintenance through the original manufacturer of the engine, as part of a maintenance contract or could contract a third-party maintenance crew to manage and carry out a fleet’s maintenance needs. These providers, known as MRO (Maintenance, Repair, and Overhaul)—companies such as HAECO, Delta Tech Ops and Lufthansa Technik – may specialize in specific maintenance operations such as engine vibration analysis and balancing.
The military has their own crews to conduct maintenance and repair operations, but will also contract services that provide equipment, expertise and resources.
The Role of Vibration Analysis and Balancing in the Engine Lifecycle Management Plan
All turbine engines have vibration limits specified by the original manufacturer, and every airframe and engine manufacturer provides procedures for addressing vibration conditions which are out-of-specification. The effectiveness of these procedures can vary, and depends on the test equipment involved as well as the skill level of available personnel.
With the right tooling and training, using these procedures on an emergent basis can bring an engine within safe limits and prevent the need for an engine change. Importantly, this can result in dramatic cost savings if the latest vibration analysis and trim balance procedures are used.
Traditional methods of fan-only balancing, for example, the “three shot plot” method, require at least four engine runs to complete. In comparison, MTI Instruments’ precision balancing system can reduce vibration to the minimum possible in one run while achieving well documented, consistent, and accurate results.
Additionally, early analysis of turbine vibration can result in significant savings; an advanced, portable system can remove the need for engine replacement and removal.
MTI Instruments Involvement with Aviation Maintenance, Repair, and Overhaul
The original precision balancing and vibrational analysis systems, known as PBS, were developed in the early 1980s as the result of relationships between MTI Instruments and the USAF, NASA, Rolls Royce, General Electric, and Pratt & Whitney. Some engine OEMs specified the MTI Instruments’ PBS in maintenance documentation, leading to its purchase by aircraft operators and MRO’s soon afterwards.
MTI Instruments PBS-4100+ Workflow for Engine Vibration Analysis and Balancing
Video credit: MTI Instruments
As a result of the power and simplicity of MTI Instruments’ vibration testing and balancing systems, they soon penetrated almost all corners of the large frame engine MRO market. Since then, MTI Instruments has consistently adopted new technological advances in order to improve the functionality of their PBS, making it more compact and easier to use.
About MTI Instruments
MTI Instruments is a US-based manufacturer of highly-advanced balancing and vibration analysis systems. MTI Instruments’ portable and test cell balancing solutions are specifically designed for aircraft engine and turbine manufacturers, and are backed by 50 years of industry service.
Leading names from commercial aviation, OEMs, and Airlines, as well as the US Air Force and other militaries, use MTI Instruments’ systems to solve engine vibration problems every day.
MTI Instruments is obsessed with precision and providing innovative vibration and balancing expertise to maintenance, repair and overhaul (MRO) organizations across the world. MTI Instruments is also proud to be an ISO 9001:2015 certified company.
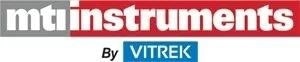
This information has been sourced, reviewed and adapted from materials provided by MTI Instruments Inc.
For more information on this source, please visit MTI Instruments Inc.