EV batteries need to cost less and last longer for widespread electric vehicle (EV) adoption. Until these challenges are solved, the e-mobility industry will find it hard to match the hype that’s driven by Tesla, the established automakers and a plethora of startups that are attracting investors.
According to Axios, the cost of owning an electric vehicle will be much greater than owning a traditional one until the production of EV batteries cost less than $100/kWh. Unfortunately, the EV industry is about ten years off hitting that target according to current trends.
However, there is some news that offers encouragement. EV batteries with better performance at a lower cost are just a few years away. What is more, is that the adoption of these more advanced batteries is expected to see an increase in EV sales long before 2030.
While Elon Musk suggests that greater gains in energy density are nearing, other industry players are also promoting their progress: 2020 was a good year for the electric vehicle as General Motors’ announced its lower cost Ultium batteries while Volkswagen’s introduced an affordable electric SUV.
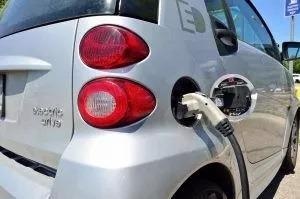
Image Credit: MTI Instruments Inc.
EV Batteries and Thickness Gauging
One of the ways that battery manufacturers can bring down the costs and enhance performance is through better thickness gauging. To appreciate why this is important, consider the fact lithium-ion batteries (Li-ion) are comprised of metal plates with lithium compounds.
The cathode contains a copper plate and the anode contains an aluminum plate. A dielectric separator between the plates facilitates electrical insulation. Although this thin layer is fabricated from relatively inexpensive materials, its significance is crucial.
If the thickness of a dielectric separator is too great, battery performance can diminish. Unnecessary dielectric thickness can even lead to the entire EV battery being scrapped.
This includes the expensive cathode because when the battery is manufactured, the plates and the dielectric separator are calendared together. The sandwich-style structure must fit inside the battery compartment, a challenging environment where space is limited.
How to Measure Battery Plate Thickness
In a recent application note, MTI Instruments of Albany, New York (USA) detailed how capacitive sensing is crucial when measuring EV battery plate thickness with nanometer stability and accuracy.
MTI is collaborating with several EV battery manufacturers to configure and test for their particular environments. MTI’s proprietary Digital Accumeasure system, along with dielectric sensing probes to assess the thickness of the separator, provides quality control departments optimal assistance when monitoring EV battery construction.
While the dielectric separator isn’t the most expensive part of an EV battery, failing to accurately measure its thickness can have costly consequences.
For EV battery manufacturers looking for cost reduction methods that improve performance, consider the importance of rapid, accurate thickness gauging. To discuss your application, contact MTI Instruments.
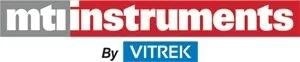
This information has been sourced, reviewed and adapted from materials provided by MTI Instruments Inc.
For more information on this source, please visit MTI Instruments Inc.