Interview conducted by Courtney Garner, MAJun 4 2020
AZoM spoke to Ken Ameika, the Global Director of the PBS Products Division for MTI Instruments, about how to increase the efficiency of engine trim balance in aviation using the PBS-4100+. Ken has two decades of experience in shock/vibration measurement serving the aerospace and energy generation industries.
How important is vibration analysis and engine trim balance in aviation?
If the engine is out of balance, it will vibrate in a fashion similar to how a bad tire or an imbalanced tire would react when mounted to an automobile. An imbalanced tire will result in vibration and wear. In an imbalanced aircraft engine, one would experience passenger discomfort and under more extreme circumstances, poor engine performance, lower fuel economy, and possibly engine damage. In the aircraft engine world, a well-balanced engine is critical for both reasons of safety and efficiency. Vibration reduction and engine balance are accomplished via the trim balance process.
Measuring and Balancing Engine Vibration with PBS 4100+
How do you carry out an engine balance operation?
When you look at an aircraft engine, you will notice there is a fan in the forward section. In the center of the fan, behind a cute little artistic "swirl", lies a cone-shaped spinner. Within the structure of the spinner, one would find a feature containing precisely located holes or a ring with clip features. Within these holes or clip positions, precisely specified weights may be fitted into strategic locations.
The weights, when placed optimally will offset or compensate for an intrinsic imbalance within the engine. The process of installing weights to overcome an imbalance is referred-to as "trim balancing".
The placement of balance weights into precise positions is the key to success. Instrumentation must measure vibration of a running engine and correlate the vibration with the fan position as it is turning. The instrumentation will then analyze the vibration levels and prescribe a "balance solution". The balance solution is akin to a doctor's prescription: "Place one or more weights into the following positions in the spinner."
How often should vibration check and balancing be performed?
There are a range of instances that would necessitate a vibration check and possible rebalancing. For example, any time that a maintenance event occurs to the fan or to the low pressure turbine of the engine. If any damage occurs, when a fan blade is replaced or blended, a balancing operation is generally mandatory. Another example is as the engine ages; vibration increases; thus requiring a re-balancing.
Could you give our readers an overview of how a common balancing method, the three shot plot, is used to balance an engine?
In the advent of the turbine engine, engine balancing was a crude affair. The "three shot plot" method is the original scheme to balance an engine. Established in the 1960s, the three shot is a crude approach which; contrary to the name, requires five engine surveys or "runs". A "run" is defined as bringing an aircraft to a place where it is able to be brought to its full operating power setting and then brought back down to an idle power setting, measuring vibration levels over the full operating range.
The three shot plot process requires a baseline run to establish the initial state of the engine, followed by three additional engine runs, where the placement of a known weight is installed each time, in 120 degree position increments. With each weight placement; an engine run is conducted and the vibration levels are plotted on a sheet of graph paper.
At the conclusion of the process, utilizing three weight placements-with each engine run, a crude approximation would be established to identify where to place weights to balance the engine.
Following the three shot approximation, a fifth run, known as the "check run" is required to validate whether the balance approximation is effective.
I'd like to stress that the three shot procedure yields an approximation. Frequently, additional vibration survey runs are required to refine the solution using the method.
What are some of the challenges associated with using the three shot plot method?
Consider this: Each of these engine runs requires a multiple personnel working as a team for hours. Each engine run requires a mechanic (AMT) to install weights. Two people on the flight deck. Two or three people as ground support personnel.
To start and operate an aircraft at power requires the plane to be moved to a specified location designated for such operations.
We estimate each "shot" of a three shot balance requires three hours. Hence, to perform a three-shot balance; requiring five runs consumes two shifts, at minimum, utilizing multiple personnel.
Another downside, is that the affected aircraft is on the ground for nearly a full day losing revenue to being out of commission.
Could you give an overview of the PBS-4100+ and how it differs to using the three shot plot method?
With the PBS-4100+ equipment, the balance process is reduced to TWO engine runs. The crew will perform a baseline run (run #1) and then PBS-4100+ will immediately prescribe a balance weight solution, allowing an immediate check run (run #2).
Utilization of the PBS-4100+ eliminates three of the runs required using the three shot plot method. As a result, we have heard from our customers, that a vast reduction of personnel time and aircraft ground time is realized. The solution prescribed by PBS-4100+ is high resolution, by comparison: The weight solution to be installed is precisely calculated. Hence, vibration levels of the engine may be reduced substantially utilizing minimal balance weight, compared to the three shot approximation.
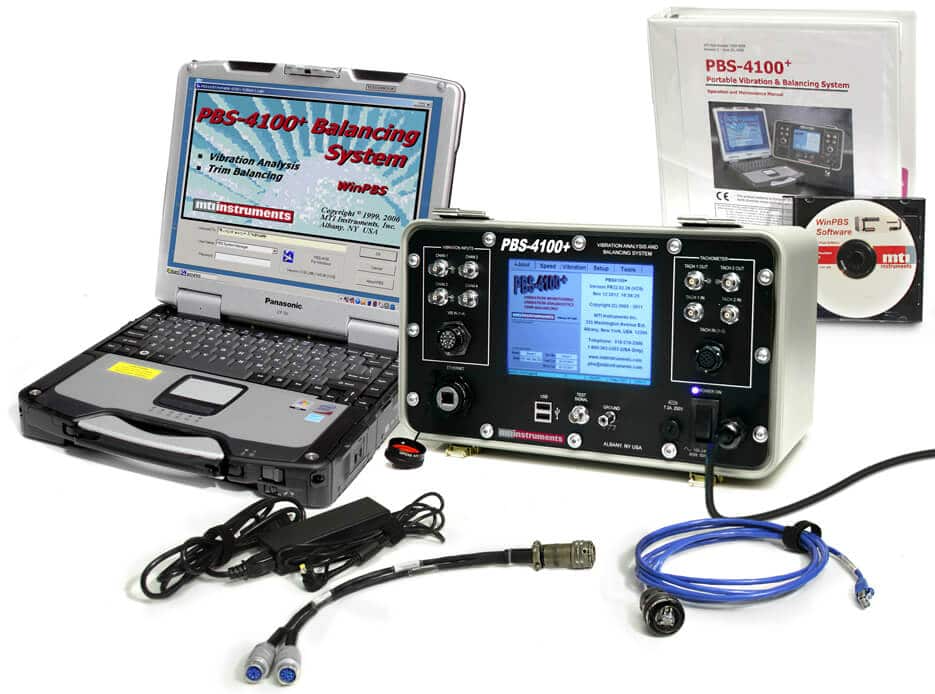
Image Credit: MTI Instruments
What is the difference in cost between using the three shot plot method for engine balance, and using the PBS-4100+?
Costs savings must be viewed using three different metrics: aircraft availability, manpower, and fuel burn.
A top concern to consider is aircraft availability. Using the three shot plot method, the aircraft is removed from revenue service for 24 hours - that's 24 hours that that aircraft is not generating income. Using a PBS-4100+, the same task may be performed in six hours -- or less -- from start to sign-off.
Now consider staffing. From modeling and other sources, this can be accomplished with two crew members and an AMT mechanic. Supporting the aircraft, we estimate at least two ground support personnel are required to manage the movements on the airfield. Accounting for three hours per engine run, we conclude that this series of operations is something in the area of 75 man hours per engine, plus fuel cost for the three shot approximation. Using the PBS-4100+, with only two engine runs, labor burden is reduced to 30 man hours.
Finally, consider fuel: Elimination of three engine runs reduces fuel burn - and carbon footprint of the process by 60 percent, at minimum. It is noted that running an engine at full power requires multiple engines to be operated, lest one risks damage to the landing gear.
Adding all cost savings; accounting for aircraft utilization, personnel, fuel, and lost opportunity; using a PBS-4100+ instead of a three shot approximation can result in savings of 75% - 80% with a superior result.
MTI has calculated a number of ROI estimates that would suggest that even moderate usage of a PBS-4100+ would pay for itself within months.
Which sectors within the aviation industry is the PBS-4100+ tailored to?
Any sub-group of the aviation industry benefits; the military, commercial carriers, the freight carriers, even business jets will benefit greatly. It is notable the PBS-4100+ family already is an established market leader in all these segments.
About Ken Ameika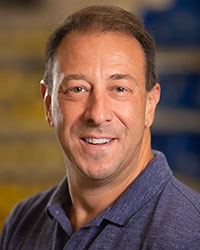
Ken Ameika is the Global Director of the PBS Products Division for MTI Instruments. He has two decades of experience in shock/vibration measurement serving the aerospace and energy generation industries.
Disclaimer: The views expressed here are those of the interviewee and do not necessarily represent the views of AZoM.com Limited (T/A) AZoNetwork, the owner and operator of this website. This disclaimer forms part of the Terms and Conditions of use of this website.