Brazing is the process of combining two metals using a filler material that melts, flows, and wets the surfaces of the metals at a temperature lower than the melting point of the metals. A covering gas or a flux material is used to provide protection against oxidation of the metal surface and the filler material during the process.
Why Induction?
Torch
The most extensively used brazing method is torch brazing, which requires skilled brazing operators. Yet, finding an experienced operator for the process is challenging for many manufacturers. In addition, torch brazing increases safety and regulatory concerns in production facilities because of its open flame.
Furnace
Another common form of brazing is furnace brazing. Present-day manufacturing companies are looking for ways to reduce production cost, to improve production efficiency, and to replace space- and energy-intensive furnaces without compromising on the quality of the product.
Induction
The above-mentioned problems can be overcome by employing induction brazing as it minimizes energy costs, avoids the need for an experienced operator, implements a lean production process for higher quality parts, and reduces the equipment footprint.
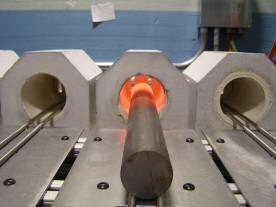
Induction brazing
The following are advantages of induction:
- Efficient heating
- Repeatable, precise heating
- A cooler, safer work environment for employees
- Quick heating
- Extended life of fixturing enabled by precise heating
The Fundamentals of Induction Heating
Induction is a repeatable, fast, efficient, precise, non-contact process for heating workpieces made of electrically conductive materials including semiconductors such as graphite, silicon carbide, and carbon, or metals such as copper, brass, steel, and aluminum. Non-conductive materials, such as plastics and glass, are heated by heating a metallic susceptor by induction which transfers the heat into the non-conducting material.
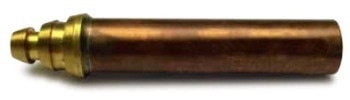
Induction brazing a brass mixing nozzle onto a twin feed copper tube for an oxyacetylene torch nozzle assembly. 6 kW at 380 kHz for 36 seconds to 732 °C (1350 °F)
Typically, an induction heating system includes a power supply, a copper coil (the inductor), and the workpiece to be heated. An electromagnetic field is formed by generating an alternating current in the coil through the power supply. The electromagnetic field in turn generates a circulating current or an eddy current in the workpiece. The eddy current passes through the resistive material of the workpiece and produces heat.
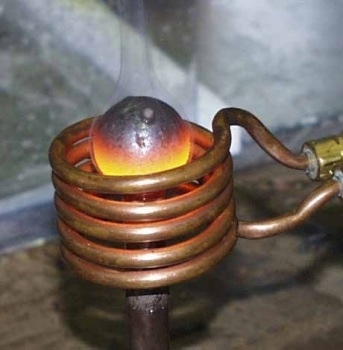
Steel-to-steel brazing of part of a regulator used in the oil industry. 200 kHz at 8 kW for 9 seconds to 732 °C (1350 °F)
The water-cooled coil is positioned around or adjacent to the workpiece. The necessary heat is produced by the induced current that passes through the workpiece. The flow of the induced current in the workpiece is positioned close to the turns of the coil. The workpiece can be precisely heated either partly or entirely with careful coil design. With the help of sophisticated solid-state induction power supplies, integrated microprocessor control systems, and a consistent positioning of the workpiece in the coil, induction allows repeatable, precise, and efficient heating processes.
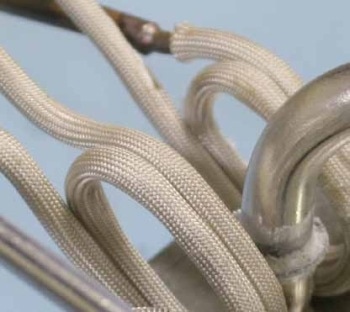
Replacing torch brazing with induction for an aluminum manifold application
The factors below have to be taken into account during induction heating:
- The type of metal used to make the workpiece determines the required heating rate and power. The higher resistivity of iron and steel enables them to be heated easily; however, more power is required for heating metals with low resistivity, such as copper and aluminum.
- The important parameters that determine the required power are the type of material, size of the workpiece, required temperature, and time to temperature.
- The operating frequency of the induction heating system governs the size of the workpiece. In the case of smaller parts, higher frequency (>50 kHz) is required for efficient heating, while for larger parts, lower frequency (>10 kHz) is required to achieve greater heat penetration.
- Certain steels exhibit magnetic properties. Hence it is essential to take the hysteretic properties and resistivity of those metals into account during induction heating. Steel loses its magnetic properties upon being heated beyond the Curie temperature (500–600 °C). However, the heating technique is provided by eddy current heating at higher temperatures.
- With higher temperatures, radiation and convection losses from the heated parts are an important parameter. Insulation techniques are usually used for reducing heat losses and the power supply from the induction system.
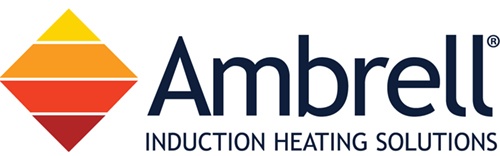
This information has been sourced, reviewed and adapted from materials provided by Ambrell Induction Heating Solutions.
For more information on this source, please visit Ambrell Induction Heating Solutions.