In general, protective coatings are applied on automotive brake rotors to minimize corrosion and rust, thus providing an aesthetic and robust look.
After being applied, the coatings are usually dried or cured in an oven. However, a considerable amount of energy and time can be saved by using induction heating for rotor finishing applications.
Induction Heating
Induction heating involves generating heat from the inner side of the rotor, thereby improving the quality of the finished coating by curing from the metal coating interface enabling any outgassing at the time of the curing process.
Apart from conserving the energy and time used in ramping up an oven, the concentrated and flame-less energy also conserves the ambient heat surrounding the component.
Cure for Brake Rotor Coatings
Induction heating can also be used for water-based and chromium-free cadmium coatings. It steadily produces a quality cure of specialty coatings by employing a special coil and power supply to maintain accurate and uniform temperature across the rotor.
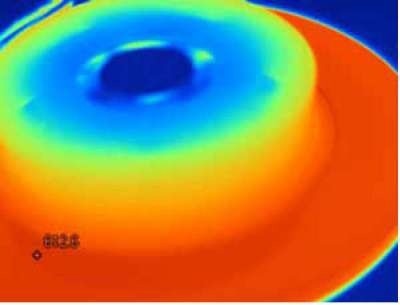
Figure 1. Thermal image shows the even temperatures on the rotor surface while keeping the center hub cool.
The heating process does not change or impact the coating during the elevated temperatures on the rotor at the time of the braking process.
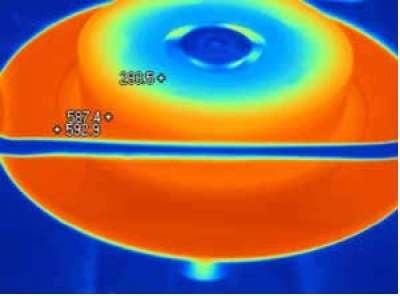
Figure 2. Thermal image shows precise, direct, and consistent heating of the rotor
Ambrell offers multipurpose induction heating systems that can be configured for the curing cycles at 575–600 °F and pre-cure at 150–250 °F for varying sizes of brake rotors.
Easy Integration
In the curing process of coatings, induction heating provides several advantages. Ambrell has deployed over 10,000 induction heating systems for various types of applications around the world.
The company designs tailor-made systems that help reduce production time and save considerable energy costs.
Ambrell offers multi-level service to brake rotor manufacturers, ranging from system design and implementation to support after installation.
Advantages of Induction Heating Systems
Induction heating systems produce a flameless concentrated heat energy, thereby making it effective and safe. They maintain the right temperature across the rotor, where each rotor has the same cure process. The system’s coils can be configured to rotors of any size.
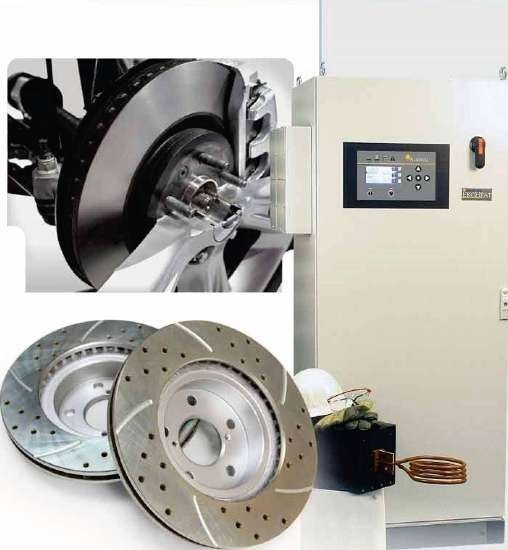
Figure 3. Precision induction heating for automotive rotor treatment
As the system avoids the need for furnace ramp up, a significant amount of energy can be saved. Moreover, faster part throughput also assists in reducing production time. The system can be easily integrated into prevalent production lines.
EKOHEAT Induction Heating Systems
In the case of brake rotor applications, the EKOHEAT induction heating systems from Ambrell offer an accurate, rapid, and energy-efficient solution.
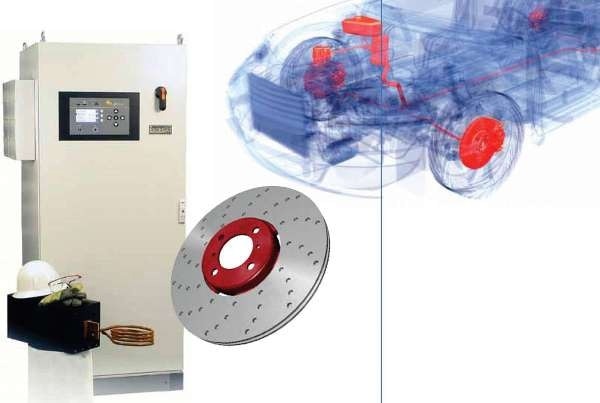
Figure 4. EKOHEAT
Following are the advantages of these systems:
- Accurate, direct, and steady heating of the rotor
- Auto-tuning feature renders it easy to heat rotors of different sizes and shapes
- Movable work heads enable the power supply to be positioned away from the manufacturing line to save valuable space
- Efficient power conversion with a power factor of more than 0.9: minimizes energy costs
- RS485 serial port enables monitoring, remote access and data logging
- Ability to be incorporated into a production line
- 100% duty cycle is suitable for automated production processes
- User-friendly display and control interface
- CE marked and produced in an ISO 9001:2008 facility
Customer Service and Solutions
Induction heating experts at Ambrell work in collaboration with customers to design a tailor-made induction heating coating curing solution to be suitable for a particular production facility.
Optimal results are ensured by testing the customers’ applications in advance and then applying the integrated induction heating solutions to the process.
Ambrell’s service department offers preventive maintenance and emergency support services to make sure that induction heating systems continue to exhibit operational excellence.
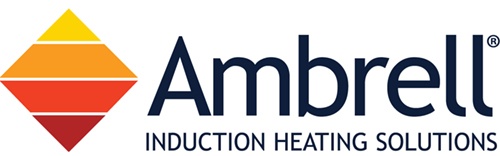
This information has been sourced, reviewed and adapted from materials provided by Ambrell Induction Heating Solutions.
For more information on this source, please visit Ambrell Induction Heating Solutions.