The Omniseal® RACO® spring-energized seal is a polymer sealing solution from Omniseal Solutions that has been a critical part in the aviation, space and oil and gas industries for over 60 years, excelling in conditions where extreme tight performances are required - either in very high (500°F/260°C) or very low and cryogenic (-450°F/-268°C) temperature environments. Typical examples include applications that have contact with cryogenic fluids such as liquid oxygen, hydrogen or nitrogen. Throughout 60+ years of successful use, the RACO® seal design has not changed very much although it still continues to evolve and be developed to meet customer and market need, representing a state-of-the-art solution in the sealing industry.
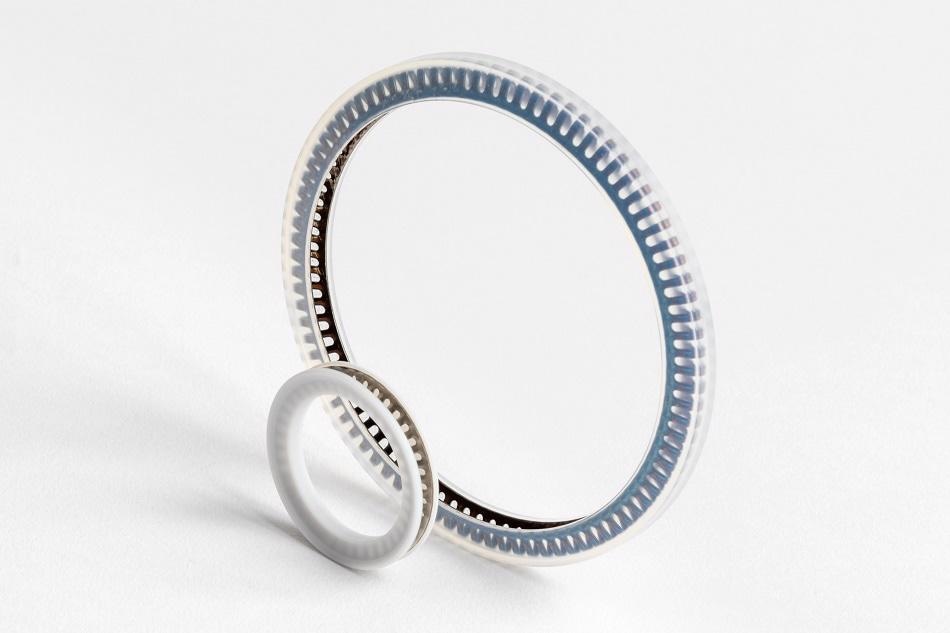
Omniseal® RACO® Polymer Seal
Omniseal® RACO® Spring-Energized Seal Origin
The Omniseal® RACO® polymer seal was engineered with a specific spring type that grants continuous spring contact along the entire sealing lip, and a jacket design manufactured from proprietary polymer materials. Initially, the seal was created to improve performance over soft elastomeric seals and hard metal gaskets in applications involving cryogenic liquid propellants in various rocket engine programs that had repeatedly failed. The RACO® name is trademarked by Omniseal Solutions for various countries, and continues to be used on most space applications with challenging requirements, particularly those requiring leakage lower than 10-3 sccs when measured at LH2 temperatures.
Omniseal® RACO® Spring-Energized Seal Unique Design
The RACO® seal is a very high load and resilient spring with a spring load that averages about 8 N/mm of circumference. Depending on the application, the load may increase to 15 N/mm and even higher to 18 N/mm of circumference. Why is such a high load needed? This is to support the jacket material in circumstances where temperature goes very low and the material tends to shrink, with an extreme potential effect of losing contact with the counter surface and resulting in severe leakage. To prevent this dangerous situation, the polymer seal is engineered to keep the lips in place and balance shrinkage.
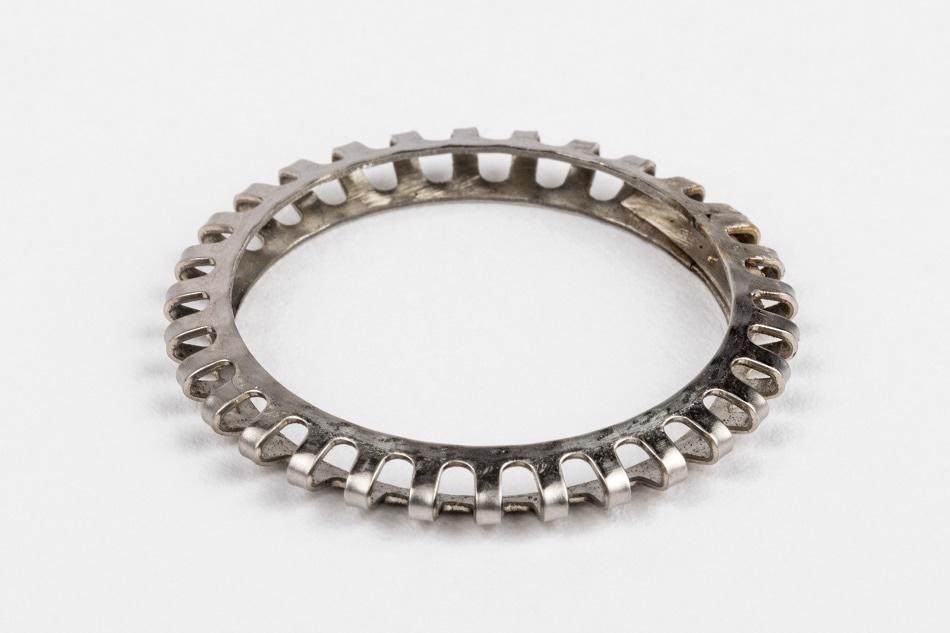
Omniseal® RACO® Polymer Spring Design
There are other alternatives in terms of sealing capability for cryogenic conditions such as spring-energized metal c-rings; however, they have loads of up to 800 N/mm of circumference. Having these high loads make installation quite complex, requiring numerous bolts with high strength to keep the flanges closed and the metal seals in place, increasing both the total cost and the weight of the equipment.
Omniseal® RACO® Spring-Energized Seal Application Use & Evolution
The Omniseal® RACO® seal is typically used for static applications or for slow angular movement and can be manufactured for internal or external pressure. The seal can be adapted to almost any existing groove dimension. This aspect has been recently improved in which the seal can be used for relatively small grooves, with a diameter as small as 18 mm. On the upper scale limit, it is virtually non-existent and more linked with the machined polymer jacket, with manufactured examples exceeding 2 meters – in the case of the LOX tank of NASA Space Launch System – and available machining capabilities for jackets up to 3 meters.
Other recent manufacturing improvements include the laser welding of the spring that improves the quality of the sealing solution in regards to low leakage performance. Manufacturing process has also followed market evolution and the RACO® seal is cleaned according to the most stringent standards such as those required by the space market (IEST-STD-CC1246E) with no particles having a size above 300 micron and NRV (non-residual volatile) level lower than 2.7 mg/0.1sqm.
Many of the typical applications where the RACO® seal provides the most critical value is within the space market for static sealing in launch vehicle propellant tank feedlines, valves or turbo pumps, especially using fluids such as LOX or LH2. Since the seal is designed to handle cryogenic and high temperatures, it is also effectively used in the oil and gas industry for cryogenic ball valves or swivels for marine LNG loading arms and is also manufactured in large diameters.
The Omniseal® RACO® spring-energized seal has provided over 60 years of service, being a critical part in historical milestones, starting with the Mercury program, to the Apollo and Space Shuttle missions, and up to the Artemise (SLS) program.
Omniseal® RACO® Spring-Energized Seal Case Study: Launch Vehicle Fuel Tank
The Omniseal® RACO® seal is used in launch vehicle applications such as fuel tanks because the sealing in these areas are critical due to the presence of liquid oxygen or hydrogen, which are easily ignitable. Any small amount of leakage can create a hazardous situation and lead to a potential explosion of the entire launch system.

This information has been sourced, reviewed and adapted from materials provided by Omniseal Solutions.
For more information on this source, please visit Omniseal Solutions.