Chillers are employed across various industries for eliminating heat from facilities or from processes. Some examples include chemical processes that need a steady supply of chilled water for their processes or commercial brewing operations that maintain the temperature of the entire brew houses close to 0 °C.
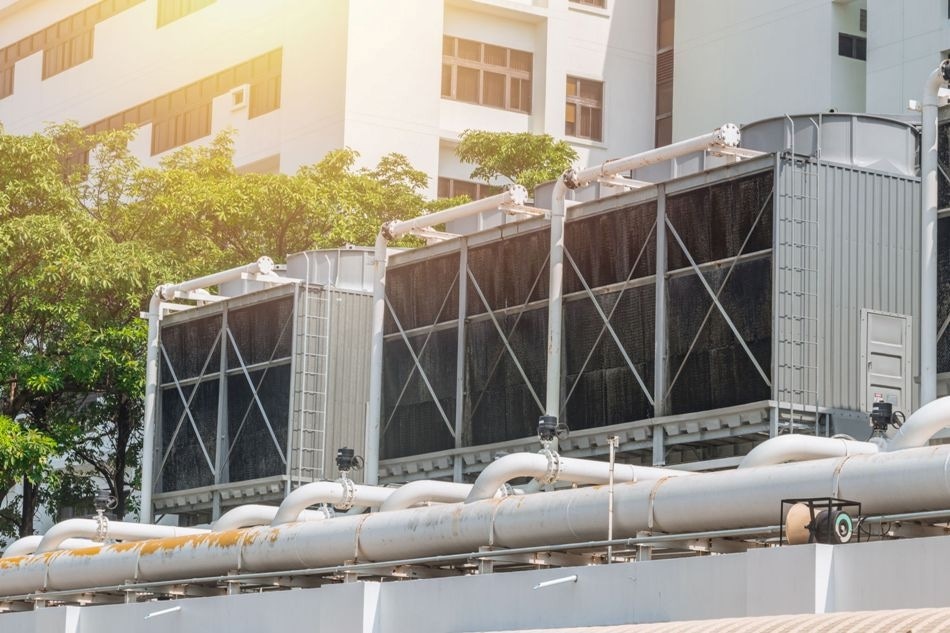
Typically, chillers operate either by vapor compression or by the refrigeration/absorption cycle. Nowadays, the absorption/refrigeration cycle is not extensively used in industry, hence this article focuses on chillers that operate using the vapor compression technique. This technique involves the absorption of heat by the refrigerant liquid, which causes it to boil and transform from the liquid to the gas phase. The gas is then compressed back into a liquid as the heat is eliminated from the process.
Ask the Expert: Chiller Oil Analysis
Similar to a home air conditioner, the heat that is removed is normally removed outside of the facility and hence, there is a net heat transfer from the medium being chilled to the environment.
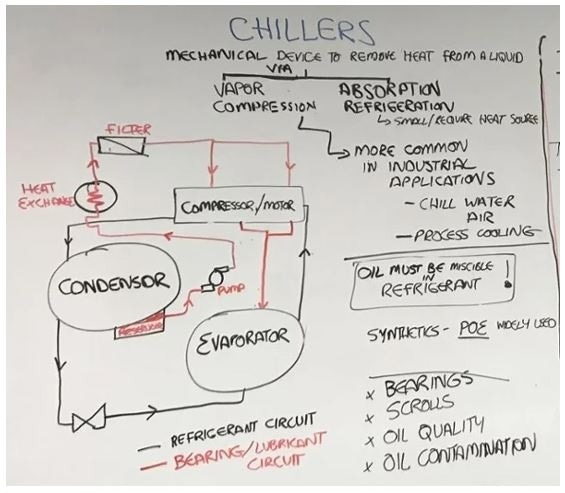
As these systems are usually sealed, refrigerant can't escape. Therefore, it is reasonable to ask, does one need oil analysis on a sealed system? The brief answer is yes. The fluids in these systems still have to be circulated around and compressed by scrolls and pumps. What needs to be monitored is the condition of the bearings and other moving parts in the components that drive these systems. In particular, Spectro scientific is interested in monitoring the scrolls, the bearings, oil contamination, and oil quality.
One unique fact about compressors is that the lubricant should be miscible in the refrigerant that drives the system. Generally, the manufacturer will suggest lubricating oils that are compatible with its chosen refrigerants and systems. The latest ozone-friendly refrigerants often need synthetic oils. Polyol ester lubricants have turned out to be relatively common in chiller systems.
Why Monitor?
Oil condition - The miscibility of the lubricant in the oil can be affected by oil condition. One must check to ensure that it is the right type of oil and it is in good condition.
Oil contamination – In case the oil is contaminated, it can negatively impact the chiller efficiency. Specifically, water contamination can cause the efficiency of the chiller to decrease.
Wear – As discussed, the bearings and the scrolls are the key components to monitor. Wear debris or excessive contamination can be indicative of bearing failure. If detected early, it can be repaired before the system stops working. Early intervention is usually less expensive and it avoids costly downtime.
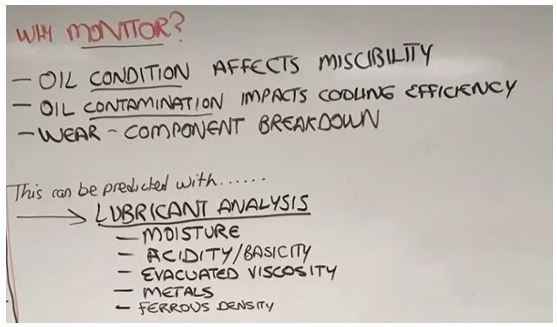
What are the Recommended Specific Tests?
Moisture - Water contamination can decrease the chiller efficiency and it can also result in corrosion and freezing problems. By ensuring that the oil is dry, several problems can be avoided in the future
Acidity/basicity – It is recommended to run a test for Total Acid Number (TAN) for chlorinated refrigerants like R-22 or Freon. For ammonia-based systems, it is recommended to run a test for Total Base Number (TBN). TAN can impact the miscibility of the lubricant in the refrigerant.
Evacuated viscosity (40 °C) - The resistance of a fluid to flow under the force of gravity is referred to as kinematic viscosity. It is the most important physical characteristic of a lubricant. If the viscosity is off in a chiller system, it can denote that the separator is not working properly.
It can sometimes be hard to measure the viscosity in chiller systems since the refrigerant dissolves in the lubricant and often has to be outgassed before obtaining an accurate viscosity measurement. This can take several hours. Luckily, this is not needed if the Spectro Scientific MiniVisc 3000 is used. The MiniVisc’s split capillary design enables lubricants to outgas as the measurement is being done.
Metals - Elemental analysis of metals can establish the source of any contamination enabling the user to diagnose the source of the problem more effortlessly.
Ferrous density - A sharp increase in the size of ferrous particles or a sharp increase in ferrous wear is usually indicative of abnormal wear situation that is getting worse. Monitoring ferrous particles enables maintenance personnel to intervene before a failure turns out to be disastrous.
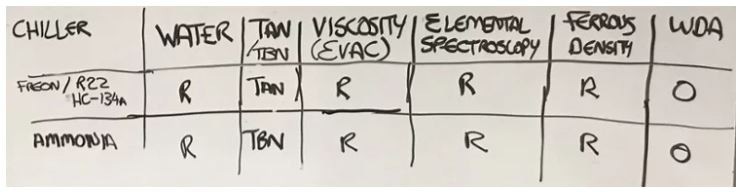
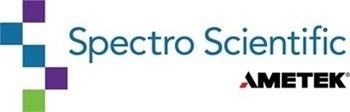
This information has been sourced, reviewed and adapted from materials provided by AMETEK Spectro Scientific.
For more information on this source, please visit AMETEK Spectro Scientific.