The metal industry is reliant on accurate analysis for quality control purposes, but this often comes at a significant cost to these companies. This is especially true of the analysis of nitrogen at low detection limits, as this is a crucial and challenging task. This process has usually relied on a company’s investment in a mid to high range optical emission spark spectrometer (OES) or an expensive combustion analyzer.
These systems have been relied on in the past as they were the only ones that could accurately measure nitrogen at low detection limits. This high level of analytical performance has been provided by high-level, high-cost OES analyzers, but identifying the exact level of nitrogen is essential to ensure safety and quality in cast iron and steel production.
.png)
Safety-critical Nitrogen Analysis
For foundries faced with the high cost of the required analysis equipment, these costs must be recovered elsewhere, as they must analyze nitrogen levels in their casting process.
Identifying the levels of nitrogen, as well as other elements, present in iron and steel is vital to ascertaining the product quality, behavior and safety of the metal. Often used as an alloying element in duplex and stainless steels or in nitration of the metal, an excess of nitrogen (especially in low alloy steels, steel and iron castings) can cause inconsistent mechanical properties and surface damage such as pin holes and fissures, all of which can be dangerous.
This means that keeping nitrogen levels low is an important part of process control for foundries and steel works, which in turn requires quick and accurate analysis at low detection limits. For example, in iron casting the critical analysis range for nitrogen content is between 40 and 140 ppm. When present in up to 100 ppm nitrogen has a beneficial effect by increasing the strength of the material, but between 100 and 140 ppm pinhole formation can begin and this makes effective OES monitoring necessary.
This may be the case for a company that produces welding studs and must monitor nitrogen levels extremely closely. Excess nitrogen can lead to porosity, and as these products are used for welding, porosity in the studs could be dangerous. Nitrogen levels would want to be kept at below 120 ppm to ensure the company delivers safe products.
Verification to this level of detection would require investment in high-priced, high-end OES analyzers or an expensive combustion analyzer. This also carries with it accompanying operational and maintenance costs, and these must be met by operators, as it isn't an option to forgo nitrogen analysis.
Innovation in Analysis – Low levels at Low Cost
These issues have led Hitachi High-Tech to create the FM EXPERT. Ideal for the metal industry, it’s the first low-cost OES analyzer that allows nitrogen analysis at low detection limits. With a lower detection limit of 30 ppm it is the best equipment on the market in terms of analytical performance to price ratio.
The FM EXPERT is an excellent option for foundries looking to introduce cost efficiencies into their processes, and actively addresses the key aspects of OES nitrogen determination:
- Optimized argon flow management in the spark stand
- Spectral range transparency, including deep UV
- A new plasma view angle for a high level of analytical performance
The launch of the FM EXPERT is just the latest step in Hitachi High-Tech’s ongoing mission to provide companies with analysis solutions that meet their diverse needs. They are committed to providing companies with the tools they need to add value to their operations through cutting edge analysis. By making something as important as accurate nitrogen analysis affordable, the FM EXPERT is not just the right analysis choice for foundries, it is the right business choice too.
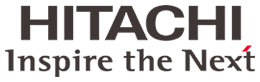
This information has been sourced, reviewed and adapted from materials provided by Hitachi High-Tech Analytical Science.
For more information on this source, please visit Hitachi High-Tech Analytical Science.