In the field of manufacturing, release films inhibit molded parts from attaching to a tool, and vacuum bags allow a composite material to be compressed by atmospheric pressure in the Vacuum Assisted Resin Transfer Molding (VARTM) method.
In general, dielectric sensors must be in direct contact with the material under test (MUT). However, the release films and vacuum bags inhibit contact and pose difficulties in the dielectric cure monitoring (DEA) process.
An ideally engineered sensor, like the 1" Single Electrode1 reusable sensor, has the ability to quantify cure state via thin films, and facilitate the use of DEA in a broader spectrum of applications.
Definitions
This article illustrates and discusses data for log(ion viscosity) and slope of log(ion viscosity), which specify the cure state. The plots demonstrate characteristic features like the time to a chosen end of cure, minimum ion viscosity, and maximum slope of log(ion viscosity). In a concise form, log(ion viscosity) will be denoted as log(IV) and slope of log(ion viscosity) will just be referred to as slope.
Both frequency-dependent (σAC) and frequency-independent (σDC) components are included in electrical conductivity (σ). Under an oscillating electric field, σDC emerges when mobile ions flow, while σAC emerges when stationary dipoles rotate. These two responses behave similar to electrical elements in parallel and are combined together as shown below:
σ = σDC + σAC |
(ohm−1–cm−1) |
(eq. 1) |
Resistivity (ρ), which is the inverse of conductivity, is denoted by:
Since resistivity is related to conductivity, it also has both frequency-dependent (ρAC) and frequency-independent (ρDC) components. The amounts of crosslink density or polymerization, which are measures of the state of cure, have an impact on both the movement of ions and mechanical viscosity, and thus affect ρDC. Consequently, the term Ion Viscosity (IV) was created to highlight the link between ρDC and mechanical viscosity. The following equation defines IV:
IV = ρDC |
(ohm-cm) |
(eq. 3) |
The exact definition of ion viscosity is frequency independent resistivity, ρDC. However, for ease of use, it is also possible to use ion viscosity to explain resistivity in general, which includes both frequency independent (ρDC) and frequency-dependent (ρAC) components. But it must be noted that mechanical viscosity and cure state are more related to frequency-independent resistivity, ρDC, which is the actual ion viscosity.
AC Cure Monitoring with Direct Contact
Figure 1 illustrates the way in which a 1" Single Electrode sensor is installed in a mold or press.
.jpg)
Figure 1. 1″ Single Electrode sensor in press platen. Image Credit: Lambient Technologies.
In order to ensure proper functioning, it is necessary for the tooling around the Single Electrode sensor to be grounded. It is essential to connect this ground to the chassis of the instrumentation, schematically shown in Figure 2, to create a closed circuit for the sensing current. In case an upper platen or mold is employed, it must also be grounded.
.jpg)
Figure 2. Proper grounding of platens or mold for single electrode sensors. Image Credit: Lambient Technologies.
In applications where a release film or vacuum bag is not used, the resin flows upon being heated and compressed, and gets into direct contact with the sensor. The electrical model of this resin-sensor system is illustrated in Figure 3.
.jpg)
Figure 3. Electrical model of resin in direct contact with sensor. Image Credit: Lambient Technologies.
Figure 4 depicts ion viscosity while curing a bulk molding compound (BMC) at a temperature of 130 °C. While the BMC was in direct contact with the 1" Single Electrode sensor, an LT-451 Dielectric Cure Monitor2 carried out measurements by using a 100 Hz excitation. The response is similar to the characteristic behavior of thermosets.
With an increase in temperature, there is a decrease in the mechanical viscosity of the resin, as well as a decrease in its ion viscosity. Then, the material stays at minimum ion and mechanical viscosity until the curing reaction becomes dominant and both the values increase.
.jpg)
Figure 4. Cure of BMC in direct contact with 1″ Single Electrode sensor, 100-Hz AC measurement. Image Credit: Lambient Technologies.
During gelation, there is a rapid increase in mechanical viscosity until it turns non-measurable. Once gelation is over, ion viscosity deviates from mechanical viscosity and is usually correlated with modulus until the end of cure. Since gelation is a mechanical event, and not an electrical one, the gel point is not indicated by any dielectric feature. Rather, there is a continuous increase in ion viscosity even after gelation, thus allowing the material state to be continuously measured until the end of cure.
When the reaction ceases, the ion viscosity curve becomes flat and its slope reaches zero. In fact, end of cure is a user-defined slope that is dependent on the application requirements.
AC Cure Monitoring with Release Films
A dielectric sensor in a mold with release films is shown in Figure 5. Upon closing the mold, the applied pressure makes sure there is close contact between the release film and the sensor, as well as between the composite material and the release film.
.jpg)
Figure 5. Cross section of mold with release film and dielectric sensor. Image Credit: Lambient Technologies.
Figure 6 illustrates a dielectric sensor arranged to perform cure monitoring of material within a vacuum bag. As soon as a vacuum is pulled, the bag comes into close contact with the composite, thus enabling dielectric measurements.
.jpg)
Figure 6. Cross section of lay-up with vacuum bag and dielectric sensor. Image Credit: Lambient Technologies.
A cross-section of these configurations with a vacuum bag or release film is shown in Figure 7, which depicts how the electric field from the electrode of the sensor passes into the composite through an insulating layer, ending up in the mold.
.jpg)
Figure 7. Cross section of lay-up with insulating layer, showing electric field. Image Credit: Lambient Technologies.
An electrical model of the composite-insulator-sensor system is illustrated in Figure 8. A pair of capacitors are introduced by the insulator in series between the MUT and the electrodes. These capacitors function as boundary layers, an additional element that has not been included in the model shown in Figure 3. Since capacitors convey only AC signals, DC methods cannot be employed to perform cure monitoring.
.jpg)
Figure 8. Electrical model of resin on sensor with insulating layer. Image Credit: Lambient Technologies.
When the MUT exhibits high conductivity, generally during the minimum viscosity condition, the existence of boundary layers may lead to distortion of the ion viscosity measurements. In order to reduce the boundary layer effect, it is essential for an insulating film to be thinner than the separation between electrodes.3,4,5
The 1" Single Electrode sensor covered with HTF-621, a PTFE-based release film offered by Northern Composites, is presented in Figure 9. The thickness of the HTF-621 layer is only 0.001", and it is non-conductive and chemically inert.
.jpg)
Figure 9. 1″ Single Electrode Sensor in press platen with HTF-621 release film. Image Credit: Lambient Technologies.
The ion viscosity in the presence and absence of a release film during the cure of BMC at 130 °C has been compared in Figure 10. The curves are similar to a large extent, except during the minimum ion viscosity condition, when there is a distortion in the measurements through the release film caused by the boundary layer effect. In several cases, this distortion can be mathematically corrected and the information related to the cure can be restored.
.jpg)
Figure 10. Comparison of BMC cure with and without release film, 100-Hz AC measurement. Image Credit: Lambient Technologies.
Figure 11 illustrates the way boundary layer correction — also known as electrode polarization (EP) correction — recovers the impacted data. Following EP correction, ion viscosity measured in the presence of the release film is in good agreement with the ion viscosity measured in the absence of the release film. The slight variations between the curves are mainly caused by the temperature differences during the tests.
.jpg)
Figure 11. Comparison of raw ion viscosity and ion viscosity with EP (boundary layer) correction. Image Credit: Lambient Technologies.
The correspondence between critical points detected by sensors in the presence and absence of a release film is illustrated in Figures 12 and 13.
.jpg)
Figure 12. Comparison of ion viscosity with and without release film, 100 Hz AC measurement. Image Credit: Lambient Technologies.
.jpg)
Figure 13. Comparison of slope with and without release film, 100 Hz AC measurement. Image Credit: Lambient Technologies.
The slope for CP(4) was selected arbitrarily to represent the determination of end of cure. In practice, a slope is chosen by the user based on the application requirements. Since AC measurements via a release film are correlated to the state of cure, from Figure 13, it can be seen that the appropriate slope allows the end of cure to be detected reliably.
DC Cure Monitoring with Release Films
Although DC measurement of ion viscosity or resistance is a simple technique for detecting the state of cure, it has the following drawbacks:
- It cannot measure the state of cure through non-conductive release films or vacuum bags
- Probable distortion of data, caused by electrode polarization, during the minimum viscosity condition
Conventional high-temperature release films are produced from PTFE or other similar non-conductive materials. Consequently, they serve as the capacitive blocking layers of Figure 8 and block the passage of DC signals.
Although certain low-grade release films are conductive, the conductivity increases with temperature and may not be the same from one batch to another. DC measurements can be performed through such films, but the results combine the MUT and the film’s resistivity in unpredictable ways. Moreover, the data is temperature-dependent, not reliable, and therefore not useful.
A DC measurement option provided in the LT-451 Dielectric Cure Monitor was used with the Single Electrode sensor to monitor the 130 °C cure of BMC. DC results without any release film, with a conductive release film, and with the non-conductive HTF-621 release film have been compared in Figure 14. As a reference point, data from 100-Hz AC measurements in the absence of a release film have also been plotted.
.jpg)
Figure 14. Comparison of AC and DC measurements of ion viscosity. Image Credit: Lambient Technologies.
AC and DC measurements in the absence of a release film are similar toward the end of cure. But DC measurements without any release film exhibit distortion due to electrode polarization during the minimum ion viscosity condition. Although this distortion can be corrected by using the AC data (refer to Figure 11), the DC data cannot be corrected.
As illustrated, DC measurements can be performed through the conductive release film, but it is still dependent on distortion caused by electrode polarization. The conductivity of the release film is dominant toward the end of cure and inhibits useful probing of the state of cure.
As illustrated by very high, typically constant ion viscosity at the measurement limit in these conditions, it is not at all possible to perform DC measurements through the non-conductive HTF-621 release film.
Using an appropriate sensor, AC measurements performed through a release film or vacuum bag can follow cure and offer the same information as a sensor that is in direct contact with the MUT. The ion viscosity data is distorted by the insulating layer during the minimum viscosity condition, when the material is highly conductive. However, in several cases, this distortion can be mathematically corrected by software. But DC measurements through a release film are not viable, which is a major drawback of the DC cure monitoring techniques.
Critical Points During Thermoset Cure
Curing of a thermoset occurs when monomers react to form polymer chains, and eventually a network. In general, the reaction is exothermic — produces heat — and may be further triggered by the heat of an oven or press. Plotting log(ion viscosity) is a simple method to describe how the cure advances. The behavior of a conventional thermoset with a single ramp-and-hold step in temperature is illustrated in Figure 15.
.jpg)
Figure 15. Typical ion viscosity behavior of thermoset cure during thermal ramp and hold. Image Credit: Lambient Technologies.
Initially, with the increase in temperature, the material melts or softens, inducing a decrease in mechanical viscosity. Moreover, mobile ions undergo less resistance to movement and there is a decrease in ion viscosity. The reaction is still gradual at this point.
There is an increase in the cure rate as the material turns hotter. At some point, the accelerating reaction starts to dominate; mechanical viscosity reaches a minimum value, following which the material turns more viscous. Electrically, the ion viscosity increase caused by polymerization overcomes the ion viscosity decrease brought about by higher temperatures. Initially, ion viscosity reaches a minimum value, and then increases as a result of chain extension, which introduces an increasingly higher barrier to the flow of ions.
Once the ion viscosity reaches the minimum point, it continuously increases until there is a decline in the concentration of unreacted monomers and a decrease in the reaction rate. As a result, the ion viscosity slope also decreases and ultimately reaches zero when the curing ceases completely.
.jpg)
Figure 16. Ion viscosity curve and slope of ion viscosity of thermoset cure during thermal ramp and hold. Image Credit: Lambient Technologies.
Figure 16 illustrates the four critical points that define the dielectric cure curve:
- CP(1) — A user-defined level of log(IV) to determine the onset of material flow.
- CP(2) — Minimum ion viscosity, which closely matches with minimum mechanical viscosity, specifying when increasing viscosity and polymerization start dominating the behavior of the material.
- CP(3) — Maximum slope, which determines the maximum reaction rate time and is often employed as a signpost related to gelation. The CP(3) height is a relative measure of the reaction rate.
- CP(4) — A user-defined slope that can determine the end of cure. The decreasing slope matches with the decreasing reaction rate.
The characteristic behavior of curing thermosets with the gradual increase in temperature to a hold value is shown in Figures 15 and 16. Figure 17 shows that the response is slightly different when the MUT is typically isothermal.
.jpg)
Figure 17. Ion viscosity curve and slope of ion viscosity of thermoset cure during isothermal processing. Image Credit: Lambient Technologies.
In this case, CP(1) is either meaningless or arises as soon as heat is applied, when the material flows and comes into contact with the sensor. Minimum ion viscosity is also observed at t = 0 or follows quickly since cure starts instantly. In the case of isothermal cures, CP(3) and CP(4) are theoretically the same as those for ramp and hold conditions.
References
- 1″ Single-Electrode sensor, manufactured by Lambient Technologies, Cambridge, MA USA. https://lambient.com
- LT-451 Dielectric Cure Monitor, manufactured by Lambient Technologies, Cambridge, MA USA
- Day, D.R.; Lewis, J.; Lee, H.L. and Senturia, S.D., “The Role of Boundary Layer Capacitance at Blocking Electrodes in the Interpretation of Dielectric Cure Data in Adhesives,” Journal of Adhesion, V18, p.73 (1985)
- Lambient Technologies application note AN2.16, “Electrode Polarization and Boundary Layer Effects”
- Lambient Technologies application note AN2.40, “Electrode Polarization and Boundary Layer Effects with AC and DC Cure Monitoring”
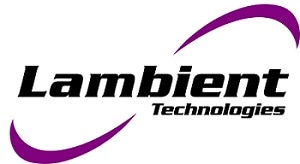
This information has been sourced, reviewed and adapted from materials provided by Lambient Technologies.
For more information on this source, please visit Lambient Technologies.