It is crucially important to prevent spillages and leaks caused by component failure in the power generation, chemical, and oil and gas industries. A vital element of guaranteeing safe plant operation is a comprehensive and reliable positive material identification (PMI) program.
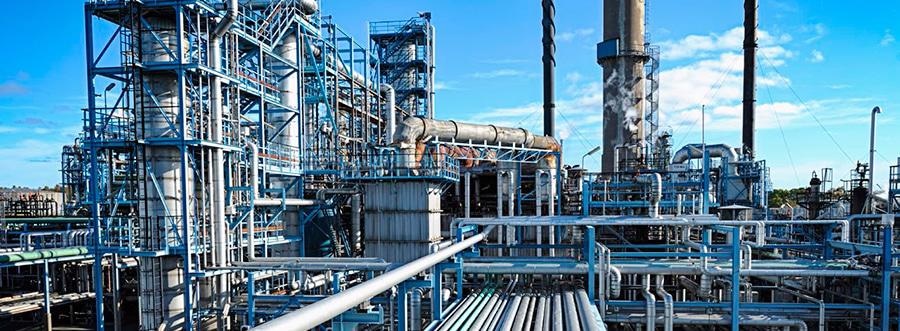
Offering a cost-effective way in which to maintain plant safety by preventing component failures, handheld X-ray fluorescence (XRF) analyzers are perfectly suited for simple, fast PMI measurements.
In order to run a PMI program which is successful, it is crucial to adapt to the industry's specific challenges. Inspection equipment in the oil and gas industry faces significant challeneges, there is a risk of damage which results from harsh conditions. As a result of a typical plant’s scale, short measurement times (without any compromise on reliability) and traceability are also crucial to success.
Instant Grade and Composition Identification
In the oil and gas industry, screws, connectors, welds, solder, and pipes must all be made of the alloy appropriate for their application. As a result of corrosive substances, mechanical stresses, and high pressures and temperatures, the safety of an entire vessel or pipeline can be jeopardized by using the wrong kind of alloy in any one component.
Every component is tested in a comprehensive PMI program prior to the operation starting. They are also tested when needed or as an aspect of in-service inspections – for instance, when a certificate is missing.
Shown in Figure 1, XRF technology can identify alloy types in a matter of seconds. The relative abundances of metals are revealed by XRF spectra, and these are subsequently checked automatically against a pre-loaded library of grades and alloys. Quick decision-making is enabled by this approach, which saves time on PMI inspections.
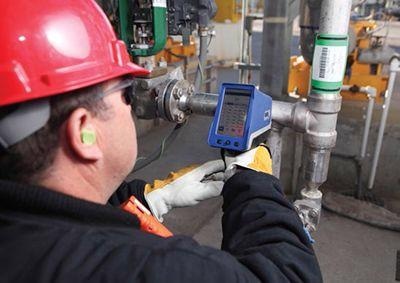
Figure 1. XRF technology enables fast, convenient PMI measurements of pipes and other components.
XRF analyzers’ sensitivity also makes them ideally suited for the detection of trace elements. Consequently, XRF can be used in different applications, like corrosion inspection.
As an example, the presence of trace elements like copper (Cu), nickel (Ni), and chromium (Cr) in carbon steel may indicate corrosion in hydrofluoric alkylation units. Alternatively, significant accelerated/non-uniform corrosion can be exhibited by carbon steel with low (Si) content, as a result of the known sulfidation corrosion process.
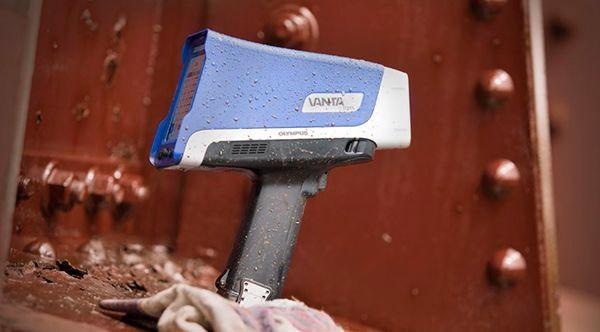
Figure 2. The Vanta XRF analyser is designed for harsh industrial conditions.
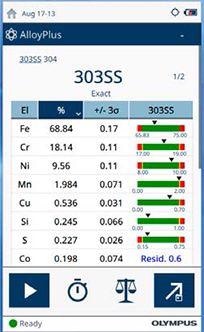
Figure 3. The Vanta analyzer’s precise, reliable readouts make it easy to determine the composition of an alloy.
Traceability and Reliable Report Generation
The traceability of measurements is an essential challenge when inspecting large structures (such as long pipelines) and plants. Even if measurement results can be quickly generated, PMI inspections can become time-consuming and laborious when you have to collate the data into detailed reports. The risk of human errors in report generation is also increased by the vast quantity of measurements involved.
In order to improve measurement traceability and simplify the creation of inspection reports, advanced XRF analyzers are equipped with cloud storage, Bluetooth, wireless connectivity, and GPS. Time is saved and the risk of errors are reduced when reporting, courtesy of the combination of timestamping on all measurements and GPS. Automated data sharing and archiving is enabled by simple internet access.
Dealing with the Elements
For inspection equipment, the working conditions in industrial plants can be difficult. If unsuitable equipment is used, damage resulting from shocks, drops, dust, or water is highly likely. Furthermore, as a result of the plant’s layout, it can often be necessary to inspect locations which are difficult to access.
XRF analyzers are perfectly quipped to deal with the difficult conditions of oil and gas plants, as they are designed for damage-resistance and portability. The devices are lightweight and can consequently be carried in one hand, or stored in a holster which is worn on a belt. XRF analyzers are made highly suitable for in-service testing by additional features like cooling fans, detector shutter protection, a design made to pass a drop test, and IP ratings.
Designed for Industry
The requirements for an efficient and reliable PMI program for oil and gas plants is met by the Evident Vanta XRF analyzers, shown in Figure 2. The rugged, drop-tested design, as well as its IP64/65 rating ensure that customers receive a return on their investment, as the risk of damage is reduced.
Together with quick, accurate, and repeatable results as demonstrated in Figure 3, the features described above highlight its suitability for a PMI program which helps to avoid the failure of parts, and ensures profitability and plant safety.
Vanta XRF Analyzer Bundles
PMI Bundle
Vanta VCR model with a wireless connectivity dongle, belt holster, preinstalled cooling fan, 5-megapixel sample camera, beam collimation, aiming camera, rhodium X-ray tube, and 3 CRMs for QC/QA testing and documentation.
Hot Surface Bundle
Vanta VMR model with wireless connectivity dongle, belt holster, preinstalled cooling fan, 5-megapixel sample camera, beam collimation, aiming camera, rhodium X-ray tube, and hot alloy surface kit for detecting low concentrations of Cu, Ni, Cr, Si, and other elements in hot steel tubes.
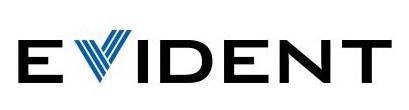
This information has been sourced, reviewed and adapted from materials provided by Evident (XRF / XRD).
For more information on this source, please visit Evident (XRF / XRD).