The Challenge: Measuring Material Cure Through Insulating Layers
The main question that companies battle with in large-scale manufacturing of automotive, aerospace, marine and wind power components is how to provide a quick and clean release of finished parts from molds. Companies that work with thermoset materials, such as epoxy fiberglass prepreg, carbon fiber, or Kevlar prepreg treat the issue with the use of release films that facilitate part removal.
Another process that can be used is Vacuum Assisted Resin Transfer molding (VARTM). During this process parts are fabricated in a vacuum bag in order to allow atmospheric pressure to compress the composite into an open mold. Nevertheless, the electronic insulation of release layers and vacuum bags complicates the measurement of cure state.
Some manufacturers try to tackle this issue by characterizing cure off-line with time-intensive laboratory methods such as differential scanning calorimetry (DSC), but it proves to be ineffective in manufacturing. However, it is still useful for manufacturers to have a measurement system in place. Such a system can ensure optimization of production processes and improvement of throughput, while at the same time ensuring the strength and stability of the finished parts.
Both AC and DC techniques can provide a measurement of cure state. Still, DC signals can’t pass through insulators, so DC measurement cannot be used in manufacturing processes leveraging vacuum bags or release films. On the other hand, AC signals can penetrate insulators; they make a cure monitoring system based on dielectric cure monitoring (DEA) ideal for vacuum bags or release films manufacturing processes.
The Solution: A Monitoring Method Based on AC Signals
A system based on AC measurement, such as DEA, is the only choice for cure monitoring for manufacturers who produce advanced thermoset components using vacuum bags or release films. AC measurements made through a release film have the same sensitivity as measurements with direct contact, which makes DEA suitable for the purpose.
Consequently, even without direct contact, AC measurements can detect crucial occurrences that characterize thermoset cure, such as:
- Flow front or resin contact
- Minimum viscosity
- Time of peak reaction rate, which may be related to gelation
- User defined end of cure
The information provided regarding DEA can help manufacturers to complete parts more quickly, to minimize the waste of raw materials and to improve throughput. Manufacturers can also gather important data provided by DEA and use it to meet requirements for strength, thickness, and robustness of the finished parts.
Probably the most important help that DEA can provide is to detect when the cure process has fallen through, either as a result from a fault in the material itself, or due to issues with the mold. Manufacturers can eliminate discrepancies in the end product when they receive an early warning of the potential issues. Therefore, they can make course corrections before a large amount of raw material and man hours are wasted.
With DEA, tests done during the curing process provide exact details on the rate of cure. For instance, to maximize efficiency, manufacturers of aerospace parts or wind turbine blades must ensure that components are completed according to the exact specifications. Dielectric cure monitoring minimizes guessing and provides certainty. The same test can be easily repeated for every individual batch without slowing down the manufacturing process.
Dielectric cure monitoring through insulating layers eliminates the need for time-consuming workarounds to monitor cure state inside a vacuum bag or when there is direct contact beneath a release layer. Only an AC-based solution, such as DEA can measure cure in such environments.
Dielectric Cure Monitoring: How it Works
.jpg)
Detailed view of reusable dielectric sensor suitable for manufacturing
Dielectric analysis is a technique used to investigate the processing behavior, along with the physical and chemical structure of polymers by measuring their electrical properties. The main advantage of dielectric analysis is that it allows the testing of materials in a wide variety of conditions – in a laboratory, at the QA/QC bench, or on the manufacturing floor. No other method is so versatile.
Dielectric cure monitoring can be conducted in an oven, on a hot plate, in a press or mold, in an autoclave or in the actual part that is being developed or manufactured. When embedded in a part or in a large mass of material, the dielectric sensor can directly measure the effect of an exotherm on the rate of cure.
On the contrary, DMA is constrained to laboratory conditions. If the sample is liquid, it must be tested in a special cell or impregnated in some kind of a matrix. Solid samples must be prepared with a particular geometric configuration. Similarly, DSC is also limited to a laboratory, and a sample is confined to a tiny DSC pan.
When composites are manufactured, parts are usually cured using a fixed recipe for temperature and time. To illustrate it better, the process is similar to baking a cake at 175° C for 30 minutes - at the end of that time the cake may or may not be fully baked. A possible way to test if the cake is ready is to stick a toothpick into it; then, if the cake is not fully baked, it must stay in the oven longer and a test needs to be done again later. If it is not possible to test the cake, the only option is to leave it longer in the oven, for example for 60 minutes, but that poses the threat of burning it.
Currently, dielectric cure monitoring is most frequently used to confirm the consistency of parts. For example, the nominal cure of an automobile body panel made of SMC might look like the one shown in Figure 1.
.jpg)
Figure 1. Typical dielectric cure data for sheet molding compound
A nominal panel can provide a comparison of the cure of every panel. Results for each panel can be recorded for statistical quality control. Deviations beyond the defined limits show a drift in the curing process; information from the cure is available to correct the problem, therefore, the quality of parts is ensured.
For highly critical parts, such as complex aircraft or spacecraft components, every step of the manufacturing process is documented. The documentation of the steps is done in order to record that the given part is made in accordance to the specifications and to be able to analyze it in the event of failure. Many manufacturers measure the temperature of a part in order to infer the progress of cure, but it proves to be a very indirect and inaccurate method.
Dielectric cure monitoring is a sensitive way to examine cure state. It is valuable for its ability to document the steps, unlike other techniques that do not have the ability to observe cure state in manufacturing and in real time.
The most immediate benefit of this is connected to productivity in manufacturing, particularly for high value components, such as wind turbine blades. These blades, often more than 50 meters long, are fabricated in a mold. The thickness of the blade, which affects the rate of cure, and the exotherm, both vary along its length.
To determine the cure time before the blade is removed from its mold, manufacturers use experience and guesswork. However, if the blade is removed too soon, when not stiff enough, this can cause cracks; reducing the blade later than necessary reduces throughput. Dielectric sensors can be installed in the mold at strategic locations, for example, every five meters along its length.
Dielectric cure monitoring can determine when the cure along the entire part has reached the desired level, and only at that time would the wind turbine blade be demolded. As a result, profitability increases even if a factory ships as few as one or two more blades a week.
Conclusion
Dielectric analysis is a powerful and effective testing technique that is very sensitive to the curing behavior of thermosetting materials. The availability of reusable sensors and low-cost instrumentation make dielectric analysis a cost-effective technique for routine testing of thermosetting materials.
Dielectric cure monitoring reduces the time and effort needed to obtain comprehensive and accurate data about cure; it takes much less time than traditional laboratory techniques. As a consequence, an organization can save time and money, and can rely on actual results.
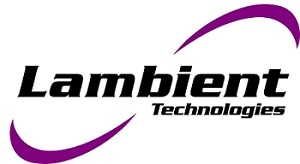
This information has been sourced, reviewed and adapted from materials provided by Lambient Technologies.
For more information on this source, please visit Lambient Technologies.