When discussing aviation assets there is one key asset: the aircraft. Today, there are around 30,000 airliners in service, employed for both passenger and freight transportation. Many individual small aircraft are included in this number. As the requirement for air travel continues to increase, all of these fleets are growing fast.

As the benefits are understood well, oil analysis is widely utilized in the aviation industry and has been for a number of years. Small planes, large planes, and even helicopters are all considered aircraft, and some major lubricated assets are crucial to these aircraft. One of these crucial assets is the engine. Engine types have a number of designs such as turbo props, turbofans, turbojets, even piston engines.
The majority of them have lubricants which are similar, but depending on the specific application, different lubricants exist. Other kinds of lubricated components in an aircraft consist of gearbox systems, hydraulic systems, and APU's (auxiliary power units). Additionally, there are also some ground support equipment types supporting the aircraft before it gets in the air, including air handler systems, gen sets, or fuel transfer systems.
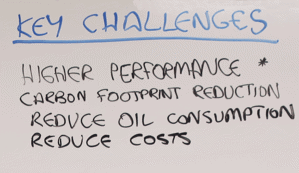
Key Challenges
Maintaining high performance for fleet safety is one of the key challenges for the aerospace industry. Oil consumption and carbon footprints reduction pressures are constant concerns, as well as decreasing cost. For many years, oil analysis has been employed to identify wear issues in addition to reliability concerns.
Now more than ever, on-site oil analysis is being considered as it can assist in each of the areas mentioned previously. One reason is that on-site oil analysis can be performed within minutes, rather than hours. The technology today is sensitive to minute trend alterations or moves in the trend. This is vital due to the unique aspects of aviation and the attention to tiny changes that could indicate early warnings.
Who Already Uses On-Site Oil Analysis?
For many years, the United States Air Force (USAF) has been performing on-site oil analysis. They have one of the biggest on-site oil analysis programs in the world. It falls under the Joint Oil Analysis Program (JOAP), and since the program began, more than 25 million samples have been tested.
The USAF possesses an extensive database and the rules/diagnostics are well understood and published. A number of militaries around the globe carry out on-site oil analysis, as do numerous commercial airlines and aircraft maintenance centers that support fleets. What is unique about on-site oil analysis or aviation analysis, is that it accounts for some of the unique conditions specific to aviation applications, particularly engine types.

As a result of continuous requests for involvement throughout the life of the systems, the original equipment manufacturers (OEMs) of those engines are heavily involved in guidance, not only at the warranty phase but after the warranty phase. The OEM guidance is crucial because there has to be traceability to investigate the cause if there are any accidents.
Something which must be considered when dealing with aviation oil analysis is lubricant formulation. Aviation lubricants are unique in that its governing body is not so much ASTM but the SAE or Society of Automotive Engineers. Their technical committees bring the airframe manufacturers, oil companies, engine manufacturers, and the aviation authorities together to agree on particular standards for reliability and safety.
SAE AS5780 is one of the major umbrella standards used. It is a widely employed standard for turbo engine and turbofan applications. It refers to lubricants which are often hindered by ester basestock or fully synthetic fluids. A number of them are utilized for gearbox applications too. There are two different duty cycles.
The typical duty cycle is known as standard performance capability, and they are looking for higher performance than capability as the industry moves towards higher performance requirements; which essentially is looking for better temperature and longer lr oxidation resistance. Other international standards which are followed in this market are the Russian GOST standards, UK standard DEF 9191, and also Japanese standards.
Lubricant formulation guides and standards compliance should be considered in addition to the fuels utilized in aviation applications. Most wide-body airliners use gas turbine based engines which combust a kerosene based type of product, such as Jet-A or JP8 for military applications. Yet, for piston engines, AVGAS is a variant which is still widely employed and it is similar to a gasoline blend.
An example is 100 LL, which is low lead. It is widely used in piston engine applications and is a leaded gasoline with antiknock compound. The filtration used on an engine is something else to consider. As these filters are extremely high performing with high efficiency micron ratings, and include chip detectors in the engine for safety reasons.
Another area of concern for oil analysis are aviation hydraulics, the hydraulics require fire resistance for prevention of fires due to accidents. Since they're designed for specific applications and usually don't do well outside of that application, phosphate esters are widely employed in those situations.
Seal performance is another thing which should be considered, but mixing these hydraulic fluids by a mineral base with a phosphate ester is not what you want. Coolant and dilution getting in or debris ingression must also be considered.
Important Tests

Some of the main things to look out for are additives, trace wear metals, and contaminants. They are tested widely throughout the entire industry. Testing is carried out utilizing elemental analysis by atomic emission spectroscopy. That can include ICP, RDE, and the testing can include a number of different methods.
Testing is crucial because it shows any early signs of abrasive wear or adhesive fretting wear in addition to contaminant ingression and the additive package in the oil. What is unique to aviation is that the alarm limits are very low. For example, one may have a condemnation limit of 1.5 ppm for chromium. Usually zero is the ideal.
Often, there will be a combined alarm system or something similar to, "six parts per million for a combination of chrome copper nickel iron combined", where the amount must not reach the limit. It is another metric for having a very low number.
Course wear debris is another parameter which is tested. The industry is aware of the limitations of spectroscopy, and the types of wear which happen may not be detected by minute wear debris. In that case, anything over five microns will typically be a requirement. There are a number of techniques for wear debris analysis.
It is known as filter debris analysis and can be measured using microscopy (either optical or scanning electron microscopy), x-ray fluorescence spectroscopy, and direct imaging particle count. Yet, a skilled diagnostician is required to review the data because it's qualitative. The test establishes fatigue bearing wear, so on occasion, there are certain wear conditions where a small buildup of particulate happens.
In other instances, a large burst of particulate happens all at once. Fatigue wear is an example of a unique particle burst production event, followed by little to no follow on debris before seizure. There are two or three body abrasive wears, which large particles quickly generate. Morphology is extremely useful in aiding the root cause analysis.
OEMs possess very detailed, distinct information available to the end user in this industry. For guidance on diagnostic documents, they focus on the shape, morphology, size, and alloy content, and engine ISO codes are generally exceptionally clean for this. It is usual to see 14/ 12/ 10 or less for a collective amount of particulate with specific focus on alarms that are metal based or ferrous.
Fluid degradation, cleanliness, and fluid contamination are other properties to consider. Cleanliness involves looking at the general cleanliness level and overall particle count. This is especially important for hydraulic systems in addition to some main engine applications. In those situations, laser or direct imaging ties to ISO 4406 or NavAir Codes. Oxidation by infrared and total acid number should be examined for fluid degradation.
Examine the water coolant for fluid contamination, deicer fluids or fuel dilution issues. Looking for overall contamination and fluid degradation concerns is important. The aviation industry is unique in that valve clearances are very small and the overall pressure of the systems range anywhere between 3,000 and 5,000 psi with exceptionally clean requirements.
Consider premature stress on the oil and coking or hot spots which happen in the engine for the case of the contamination or degradation of the oil. Electrical conductivity issues are crucial. There could be an increase or a sensor/diode that's short-circuiting if the additive is incorrect or an alteration occurs, this causes problems with the oil, and can be identified with the infrared.
Oxidation values are very low and there is a minute change for acid number. There is also something known as alien fluid. For example, a fire resistant fluid gets added into an ester base fluid or mineral base fluid or vice versa. That type of mix-up will result in slugging and will lead to a miscibility issue, which can result in problems when the aircraft is in flight.
Consider leak detection for liquids getting into the system. If substances such as deicer or glycol are present, it could be due to leaks. There could be a breather malfunction getting into the fluid systems, which are all critical things to consider. The corrosion inhibition can be affected by deicer fluid, and if water is present in the system, it is never good. This could indicate moisture coming into the system, and cause blockages and ice buildup in flight.
Finally, assess fuel dilution in hydraulic systems, as the fuel is actually utilized as a coolant for the engine. Fuel may get into the hydraulic system if there are any integrity issues.
The suggestions for on-site analysis for aviation applications are as follows: Investigate the MiniLab solutions, such as the Minilab 153 or the MiniLab EL 123 system with TruView 360 software. This enables you to develop your own diagnostic systems and alarm limits. Consider the FieldLab Series for military applications, which have XRF wear debris detection for large debris.


This information has been sourced, reviewed and adapted from materials provided by AMETEK Spectro Scientific.
For more information on this source, please visit AMETEK Spectro Scientific.