Insulating hot surfaces on exhaust systems and engines continues to be a major safety and operating issue for equipment and vehicles that are engine powered.
.png)
Firwin Hard Coat™ Insulation on Manifold and Turbo - Mining Vehicle
The advantages of applying thermal insulation covering to engine manifolds, turbochargers, and other hot exhaust components are varied, from protecting electronic components, wiring, and hoses from malfunction due to excess heat, to the protection of employees from burns, to keeping exhaust heat at the required level for optimal catalyst performance, to sound attenuation.
Although removable thermal insulation blankets have traditionally been the preferred insulation choice, recent developments in rigid insulation have allowed equipment packagers and designers to enjoy more variety when choosing a medium to use when insulating their exhaust components and engine. Firwin Corporation’s Hard Coat™ insulation is one such example of the next generation of rigid insulation.
Featuring a lightweight and durable exterior, the product is commonly applied to components such as exhaust piping, elbows, turbochargers, and exhaust manifolds. Dissimilar to removable insulation blankets, which are wrapped around an exhaust component or engine and fastened with a fastening system (frequently stainless steel lacing wire), Hard Coat™ insulation is a permanent insulation specifically applied to the component that the customer wishes to insulate.
The direct application means that the insulation material is totally enclosed and protected from exterior elements. Therefore, the risk of equipment fluid and oil leaks seeping into the insulation material is eliminated, thereby stopping the possibility of a fire hazard.
The defense and marine industries are among those that have adopted Hard Coat™ type insulation instead of removable insulation blankets. The underground mining industry also utilize this method because the protection of insulation material from hydraulic fluid or engine oil leakage is a top priority.
For certain high-temperature applications where safeguarding for oil leaks is a priority, space is at a premium, and an insulation product is required, Hard Coat™ insulation is a definite option, and may be more economical in the long run.
Paul Herman, President, Firwin Corporation
Therefore, how does one choose which insulation solution is best for them? Brett Herman, Firwin Corporation’s vice president of engineering and customer service, explains that there are several factors to consider when choosing between removable insulation blankets and Hard Coat™ insulation.
He asks, “Does the customer require removable insulation? Are there space constraints? Is the application such that there is the potential of fluid seeping into the insulation material, thereby posing a fire hazard?”
.png)
Removable Insulation Blankets on Vehicle Exhaust Piping.
.png)
MineWrap™ Removable Insulation Blankets Covering Exhaust and Catalyst of Mining Truck.
Both technologies have their own specific benefits and weaknesses. When compared to standard silicone-impregnated insulation blankets, the rigid outer surface of Hard Coat™ insulation makes it more resistant to damage from fluid leaks and less prone to tears or punctures. The surface also increases the durability of Hard Coat™ insulation compared to blankets.
Additionally, Hard Coat™ insulation is often more compact than insulation blankets, as the insulation is formed directly on the particular component. The non-insulated component is disassembled and shipped to Firwin, where the Hard Coat™ insulation is applied through a proprietary process. The component is then delivered back to the customer once it has been insulated.
The compactness as a result of this process can be crucially important in engine compartments where space is frequently in great demand. “While permanent insulation such as Firwin Hard Coat™ has its advantages, there are drawbacks as well,” explains Paul Herman.
He continues, “It cannot be removed should a part require servicing. The coating must be applied at our factory. It is also more expensive up front than traditional insulation blankets.” Removable insulation blankets therefore have important benefits for several applications. They require no additional tools or installation training, as they are designed to be easily installed.
An important factor is that they can also be removed in a simple manner which is a major advantage if equipment requires periodic inspection and maintenance. Hard Coat™ requires parts to be shipped to a factory but removable insulation blankets are frequently designed remotely utilizing digital photos, measurements, and drawings.
The resulting design of the blanket is retained as a pattern, which can be used as a reference in the future if the same part requires an insulation blanket. Firwin Corporation has an extensive library of patterns for a wide range of exhaust system components and engines.
Therefore, the redesign process is more efficient, and sections for replacement can easily be manufactured if any element of the insulation blanket becomes damaged. Even though removable insulation blankets can be prone to absorbing leaked flammable fluids within the insulation material, careful material selection and design can reduce the chances of this occurring. Firwin’s MineWrap™ blankets designed for underground mining are a good example of this.
Lastly, insulation blankets usually provide better sound absorption than Hard Coat™ materials, along with being more able to resist vibration. The following chart illustrates the different benefits and weaknesses of Hard Coat™ compared with removable insulation blankets.
As with a great number of technologies, the material selection depends on the particular application. Firwin in-house and field personnel are trained to help clients in selecting the most appropriate insulation system for their specific application.
Hard Coat™ vs. Removable Insulation Blankets
.png) |
.png) |
Permanent application to the component. It cannot be reused and removed. |
Blankets can be reused and removed which is perfect for equipment requiring periodic maintenance. |
Ideal for use in applications in rugged environments due to solid outer surface which is not prone to tearing. |
Standard removable insulation blankets have a silicone impregnated outer surface which means they may puncture or tear. |
Components must be disassembled and shipped to Firwin to be coated. |
Removable insulation blankets are remotely designed from photos, measurements, and drawings. Therefore, components remain with the customer. |
Ideal for applications with limited space as coating conforms tightly to the component. |
Applications with limited space can make blanket installation and proper fastening a challenge. |
Prevents fluids from igniting on exhaust and hot engine parts due to complete encapsulation of the component. |
Some seepage can occur under the blanket even though blankets can act as a shield to stop fluids from reaching exhaust and engine components. |
Zero risk of fluid igniting the insulation material. |
Possibility to design the blanket with a stainless steel inner liner to stop fluids from seeping into the insulation material. |
Non flammable. |
Fire retardant. |
Lead time of three weeks. |
Usual lead time of two to three weeks which can usually be expedited if needed. |
Six to 12 times more expensive than standard removable insulation blankets, but have a longer life span. |
Various costs depending on the material make-up of the blanket, but less expensive than Hard Coat™. The application and frequency of removal both impact lifespan of product. |
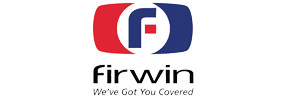
This information has been sourced, reviewed and adapted from materials provided by Firwin Corporation.
For more information on this source, please visit Firwin Corporation.