Fourier-transform infrared (FTIR) spectroscopy is a simple technique used in oil analysis. It is specifically used for detecting degradation, dilution, or illegal additives in different types of oils.
FTIR spectroscopy uses the interaction of invisible infrared radiation and matter. This produces useful molecular data and enables rapid identification of chemicals without the need for consumables or extra chemicals.
In general, the technique can be applied to liquids, solids, and gases, as well as industrial oils. It is a well-established technique and is used by legal authorities, drilling companies, automotive industries, and even at F1-racing events.
Why Are In-Service Lubricating Oils Tested?
In order to readily evaluate the performance of a lubricant, testing and diagnosis of in-service lubricating oils are very important. This is particularly vital in order to extend the life of engines and prevent abrupt and unexpected damages to the engines.
Lubricating oils decrease friction and thus protect the moving parts of the engine from corrosion and wear. In addition, the oil in diesel engines should suspend soot particles resulting from partial fuel combustion to prevent depositions.
Performance reduces considerably if the lubricant is saturated. Furthermore, the analysis of in-service lubricating oils gives information about engine-related functions to detect harmful operating conditions or component failures.
Advantages of FTIR in Oil Analysis
The low cost of modern FTIR systems, together with the potential to achieve high-quality data within a few seconds, has made this method quite popular.
Particularly in routine analysis, there is a greater demand to achieve rapid results during regular monitoring of in-service lubricants. In this regard, FTIR has already started to slowly substitute many conventional physical and chemical analysis techniques that are known to be both tedious and time-intensive.
As a result, the ASTM had implemented a standard practice E2412 called “Standard Practice for Condition Monitoring of Used Lubricants by Trend Analysis Using Fourier-Transform Infrared (FTIR) Spectrometry” demonstrating the increased use of FTIR spectroscopy in this domain.
.jpg)
Figure 1. ALPHA II FTIR spectrometer (left) equipped for oil analysis and autosampler AIM3300 (right) prepared for measurement.
The Possibilities of FTIR Spectroscopy
Figure 2 shows a brief outline of where users can find the exact required information in an FTIR spectrum of used oil.
.jpg)
Figure 2. The spectrum above shows the difference spectrum of a used-oil versus a new-oil reference. The areas (as marked) are used for the determination of the compounds.
Here, the colors denote the spectral region of, for example, oxidation products (about 1700 cm−1) or water bands (about 3500 cm−1). Since the spectral properties obviously differ from each other, the chemical components can be easily determined even in mixtures.
Why FTIR is so Easy to Use
As stated earlier, used lubricating oil can be described as a complex mixture containing a large amount of various components, including compounds extracted from the original base oil formulation as well as additives, contaminants, and oil degradation by-products. Determining the trace concentrations of these contents in the presence of the additives and base oil is the challenge of the analysis.
In FTIR spectroscopy (see Figure 2), the spectrum of the additives and base oil can be subtracted from the spectrum of the used oil sample to achieve a differential spectrum that only shows variations in the oil.
This way, the variations in the oil caused by additive depletion, buildup of degraded by-products, and contamination levels can be observed more readily.
Digital data handling makes it possible to store various reference FTIR spectra of oil samples on the hard disk and subsequently compare them to their respective used oil sample at a later date. This enables the condition of the lubricant to be trended at varying sampling time points while it is in-service.
Traditional Analysis Methods
At times, lubricants are traditionally tested using outdated techniques, such as testing for water content with a “sizzling” test, which involves placing the lubricant on a hot plate.
Obviously, techniques like viscosity tests, TBN and TAN analysis (D4739 and ASTMD2896), or even gas chromatography produce better and more consistent results; however, they need more preparative effort, chemicals, or simply demand a great deal of time.
Degradation Processes
All types of lubricants are subject to degradation while in use. There are three classes of reactions integral to the oil degradation process.
Reaction with Oxygen
Organic lubricants are subjected to high pressures and temperatures in the presence of oxygen. This inevitably results in the formation of carbon-oxygen bonds that later create carboxylic acids. During combustion, an array of by-products like carbonic acids, carbonates, aldehydes, ketones, and esters are also generated.
Reaction with Nitrogen
Oxygen and nitrogen react at high pressures and temperatures to produce nitrogen oxides (NOX). Such products can lead to increased acidity, thickening, and sludge formation because of the development of higher molecular weight compounds.
Reaction with Sulfur
Sulfate by-products are formed when sulfur-containing compounds in fuels react with oxygen, during combustion. While high-quality fuels display very low sulfur content, this degradation increases based on regional and country supply.
Application #1: Oil Quality Testing
As stated before, all types of lubricants will experience degradation while in use. Shear-thinning and increased oxidation are the most common signs of base oil degradation. Oxidative degradation takes place when reactions occur with oxygen in the environment where a lubricant is present.
Shear-thinning can be described as a physical breakdown of the oil caused by temperature and pressure conditions to which the lubricant is exposed. As a result of these and other degradation processes, the lubricant is unable to offer enough lubrication for mechanical moving engine components. Therefore, test methods to evaluate the levels of degradation by-products are important to establish the oil condition.
Application #2: Oil Dilution by Fuel
Due to piston ring wear, fuel leaks or an improper fuel-air ratio, fuel residues get into the oil. While combustion residues mostly contain long-chain hydrocarbons with high boiling and combustion points, fuel leakage consists of lighter materials.
Therefore, in both cases, the growing fire hazard potential makes it very important to determine the presence of (diesel) fuel in engine oils. Considering the fact that both lubricating base oil and (diesel) fuel stocks are extracted from crude oil distillation cuts, they are quite similar in physical nature and chemical composition. In spite of that, FTIR provides exclusive datasets for a fast, consistent, and simple analysis (see Figure 3).
.jpg)
Figure 3. The quantitative determination of gasoline fuel in oil is shown in the upper spectra. 1% (blue), 2% (red), 4% (pink), and 6% (green) of gasoline are added to an oil sample for calibration.
Application #3: Water Content
With respect to the quality of fuels and lubricants, water is a relatively infrequent contaminant due to the operating conditions in the normal engine. Yet, if water is present, it can denote coolant (water) leakage. Contamination of water causes oxidation of base oils and hydrolysis of additives leading to a build-up of acidity and increased corrosion and wear.
In addition, the presence of water can cause the base oil to gel and lead to the formation of emulsions that, in turn, can have an impact on oil viscosity and result in engine failure.
Application #4: Checking for Soot
In the case of diesel engines, whenever an air mixture/rich mixture is burned, the partial combustion of fuel results in the formation of soot. The accumulation of soot in the oil can indicate the excitation of the oils drain period or combustion issues.
Dispersants in diesel engine lubricants are designed to suspend and regulate the growth and size of soot particles. If the levels surpass the capacity of the oils to hold them, then oil viscosity will increase and carbon sludge will build up, which would begin to clog passageways and filters.
.jpg)
Figure 4. INVENIO FTIR platform offers higher sensitivity and many productivity tools to enhance routine analysis tasks. A special feature is the transit channel, a second sample compartment.
Conclusion
FTIR is a valid and reliable method for oil analysis. This technique enables users to access plenty of data with a single measurement and also streamlines the process. Infrared spectrometers are available in many different configurations and shapes, and Bruker even provides a specialized used oil analysis kit.
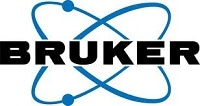
This information has been sourced, reviewed and adapted from materials provided by Bruker Optics.
For more information on this source, please visit Bruker Optics.