What are the differences between nanoscale and bulk phases? What are the viscoelastic properties in an interphase or next to an interface? What is the impact of these properties on load transfer, as a function of temperature? Quantitative nanoscale viscoelastic measurements that can answer these questions have long been a goal for AFM.
Monitoring the tip-surface interaction in AFM offers substantial opportunities to sense viscous drag and sample stiffness. However, conventional AFM methods have been hampered by the use of irrelevant frequencies, non-linearities in measurements, unaccounted adhesion effects, and further need to “recalibrate” the results. For the first time, AFM-nDMA avoids all these problems and offers results directly matching those from indenter-based nano-DMA and bulk DMA.
In developing an effective technique for the nanoscale measurement of viscoelastic properties (AFM-nDMA), there are some important considerations that need to be integrated into the methodology.
Firstly, the interaction of AFM tip-sample must be operated at low, well-controlled loads. The modulation must take place in the linear tip-sample interaction regime, requiring even smaller perturbations in force exerted on the sample by the tip.
Finally, deformation of the sample needs to be at well-defined, rheologically relevant frequencies. This means it has to be at the low-frequency regime of 0.1 Hz to 100 Hz, rather than the kilohertz and megahertz regime where atomic force microscopes typically operate.
Being at such a low frequency, the AFM-nDMA measurements can take some time. Therefore, it is preferable to locate the region of interest with a more rapid method of imaging that also provides mechanical property contrast. Particularly well suited to this function is PeakForce QNM® due to the fact it provides maps of modulus, dissipation, deformation, and adhesion relatively quickly and with high resolution.1
Probes that are adequate for AFM-nDMA also tend to work well with PeakForce QNM on the same materials, so it is not necessary to switch probes between measurements. Once identified as the region or feature of interest (Figure 1a), single-frequency images of viscoelastic moduli images can be obtained through FASTForce Volume™ (FFV), as illustrated in Figure 1b.
In this case, the storage modulus was mapped at 100 Hz (frequencies of 50 Hz or greater are recommended for reasonable acquisition times). Frequency sweep measurements (Figure 1c) were then carried out with a ramp scripting routine that utilized a series of segments to control relaxation, preload, modulation, and calculation of contact radius.
.jpg)
Figure 1. Comparison of mechanical property maps of a four-component polymer blend composed of COC (red), PP (blue), LLDPE (green), and elastomer (yellow) generated with PeakForce QNM (a) and AFM-nDMA (b) at 100 Hz, and spectra at selected points on the sample (c). The spectra show that COC grows in stiffness most rapidly with frequency, followed by PP, LLDPE, and elastomer. This PeakForce QNM 512x512 image (2 μm scale bar) was collected in about 10 minutes, while the 100 Hz AFM-nDMA 70x70 map took 30 minutes. Each spectrum took about 10 minutes to collect.
Spanning many orders of magnitude, the frequency range available with AFM-nDMA varies from 0.1 Hz to 20,000 Hz. Due to the lowest frequency measurements being relatively slow, it is recommended they be used only for those studies that really require properties to be measured in this frequency space.
Measurements above 300 Hz require an additional actuator (HFA) to extend the range of frequencies that are accessible. The HFA provides Z modulation that is independent of frequency and easily reproducible, enabling the wide spectrum DMA measurements.
The initial step in the AFM-nDMA spectroscopy measurement process is to bring the tip into contact with the sample and then exert a preload of a known force set by the user (see A portion of Figure 2).
Once contact has been initiated, modulation occurs at a low amplitude and well-defined frequencies (see C and E) to preserve a linear tip-sample interaction regime. Amplitudes and frequencies are set by the user. Finally, the tip is then pulled away from the sample and the measurements of the adhesion and full retract curve is to be taken (see D).
.jpg)
Figure 2. Typical AFM-nDMA spectroscopy force (orange) and Z position (blue) data. The tip is brought into contact and a preload is applied (marked A); the system waits for creep relaxation (B); low-amplitude modulation occurs at various frequencies, including reference frequencies (C and E); and the tip is retracted from the sample (D). Inset shows the key parameters to be extracted from the modulation segments: the deflection amplitude, D1, the Z amplitude, Z1, and the phase shift between Z and deflection (ϕ - ψ ).
The sample deformation will continue to increase for the full duration of the measurement on viscoelastic samples, thus causing the contact area to increase slowly. Lessons have been taken from the dynamic nanoindentation community to address this in three ways. Firstly, after the preload has been applied, a segment is included to enable sample relaxation (see B portion of Figure 2).
Secondly, reference segments at a given frequency are periodically captured throughout the measurement as well as right before the tip is pulled away from the sample. This allows for later estimation of the contact radius throughout the measurement (see two E segments). Finally, shuffling the frequency order of the measurements is done to avoid misinterpretation of property variation with contact time as a frequency dependence.
Spectroscopy measurements may need several minutes to adjust to obtain a single point measurement, depending on the frequencies involved.
In single-frequency mapping, the measurement at each point is kept simple to reduce the total time of acquisition, and only three segments are included: approach, modulate, and retract.
AFM-nDMA Data Analysis
It is possible to analyze the amplitude and phase of the cantilever deflection and Z-piezo motion collected during modulation segments like those shown at C in Figure 2 to acquire the sample viscoelastic properties at the modulation frequency.2,3 The Z-piezo motion is expressed by
.jpg) |
(1) |
while the deflection of the cantilever can be expressed by
.jpg) |
(2) |
If extracting the amplitude ratio (D1/Z1) and phase shift (ϕ-ψ) as illustrated in Figure 2, inset, one can determine the complex “dynamic stiffness” or force divided by deformation:
.jpg) |
(3) |
Therefore, detaching the real and imaginary parts of equation three results in the storage stiffness (real) and loss stiffness (imaginary) components. The loss tangent (tan δ) is basically the ratio of the two:
.jpg) |
(4) |
.jpg) |
(5) |
.jpg) |
(6) |
The correlation between dynamic stiffness and the storage and loss modulus can be put as:
.jpg) |
(7) |
When determining the contact radius (ac) from the final step in either the FFV ramp or the ramp script, the tip is pulled away from the sample (see D in Figure 2). This segment is adapted with an adhesive contact mechanics model such as DMT or JKR to acquire the contact radius at the beginning of the retract.
Calibration and Probes
Quantitative nanomechanical measurements with AFM have struggled for a long time with the requirement for accurate probe and system calibrations, specifically the tip shape, cantilever spring constant, and detector sensitivity.
Bruker now offers probes that have been pre-calibrated with rounded, well-defined tips, delivering reliability in their shape and dimensions.4 These tips come equipped with spherical apices that have radii of either 33 nm or 125 nm (individually measured via SEM), providing a controlled contact area for indentation depths up to 100 nm or 500 nm, respectively.
The tip shape is of utmost importance for measurements on heterogeneous samples where a constant load will result in variable indentations on the different components based on the components' material properties.
It is possible to calculate the contact area for a wide range of indentation depths using these probes. The rounded geometry of the probe shape aids linear deformation mechanisms, which are the only ones accounted for in elastic models.5
Additionally, each probe’s spring constant is pre-calibrated with a laser Doppler vibrometer (LDV), providing a precise measurement of this integral cantilever parameter, eliminating user error from this step. These probes are available in an assortment of spring constants from 0.25 N/m to 200 N/m, suitable for a wide range of sample stiffness.
Table 1 lists the pre-calibrated probe types that are available along with nominal spring constant, tip radius, and the suggested range of storage modulus to be measured. Note, however, that AFM-nDMA is not restricted to the probe choices listed in this table.
Probe Type |
Spring Const.
(N/m) |
Tip Radius
(nm) |
min E'
(MPa) |
max E'
(MPa) |
SAA-HPI-DC-125 |
0.25 |
125 |
0.1 |
10 |
RTESPA150-125 |
5 |
125 |
2 |
200 |
RTESPA300-125 |
40 |
125 |
20 |
2,000 |
RFESPA-40-30 |
0.9 |
33 |
0.8 |
80 |
RTESPA150-30 |
5 |
33 |
4 |
400 |
RTESPA300-30 |
40 |
33 |
40 |
4,000 |
RTESPA525-30 |
200 |
33 |
200 |
20,000 |
Table 1. AFM-nDMA optimized probes and the corresponding storage modulus ranges for which these probes are best suited. These probes are supplied with pre-calibrated spring constants (via LDV) and tip radii (via SEM). Note that AFM-nDMA is not limited to the probe choices listed here.
The 125 nm tips render improved signal-to-noise level over the 33 nm tips, lowering the chance of plastic deformation, while the sharper tips offer better resolution for samples with small features.
By scanning the QR code on each cantilever box, the pre-calibrated parameters are read directly into the system, which contains the spring constant, tip radius, quality factor, resonance frequency, and tip half-angle for each cantilever. Once the QR code is scanned, adjustment or “fudging” of the parameters is not necessary, and there is no need of a sample of known stiffness.
Finally, a few calibration parameters that are system-dependent cannot be pre-calibrated. Utilizing a thermal tune, or by conducting a force curve on a stiff sample such as sapphire, the photodiode deflection sensitivity can be calibrated.
It is also necessary to calibrate the amplitude and phase of the Z position, since the phase can depend on the probe and probe (or sample) mounting. These parameters are calibrated on sapphire by running the identical AFM-nDMA or force volume script with the same probe as is used to measure the sample.
Results
AFM-nDMA has been designed to measure viscoelastic properties that have been localized as a function of temperature or frequency on heterogeneous samples. The first step in the measurement is to image the sample with a standardized AFM imaging technique such as PeakForce QNM.
Figure 1a presents a PeakForce QNM image of a four-component polymer blend where it is easy to differentiate all the components. Taking ten minutes to render, this 512x512 image provides a good overview of areas of interest for future investigation. A FASTForce volume AFM-nDMA map was then collected at 100 Hz (the resulting storage modulus map is shown in Figure 1b).
While these maps can be collected at the same frequencies as those obtainable in ramp scripting measurements, frequencies less than about 50 Hz are impractical for image acquisition because of the amount of time needed and the risk of drift when taking the measurement.
This 100 Hz 70x70 map was acquired over 30 minutes. Finally, over a wide range of frequencies, single points were selected for individual ramp-scripting measurements, as shown in Figure 1c. This process was for the storage modulus plotted as a function of frequency in the range of 0.1 to 200 Hz.
The blend was made up of polypropylene (blue), cyclic olefin copolymer (indicated with a red circle), elastomer (yellow) and linear low-density polyethylene (green). Comparison of the spectra shows that COC has greater storage modulus followed by PP, LLDPE, and elastomer. The storage modulus of the COC and LLDPE is almost twofold the frequency range measured, while the other components differ less dramatically.
To inspect the consistency between methods, viscoelastic measurements by AFM-nDMA were contrasted with bulk DMA, the industry standard for such measurements.
Figure 3 compares the storage modulus (E’) and loss modulus (E”) of polydimethylsiloxane (PDMS) as measured by three methods: 1) bulk tensile strain modulation DMA (green lines); 2) an instrumented nanoindenter (light blue ‘x’); and 3) AFM-nDMA in a Santa Barbara lab (dark blue ‘○’) and 4) AFM-nDMA in a collaborator’s lab (orange ‘∆’) (using a different AFM system than the one at the Santa Barbara lab, with a different probe and different AFM operator).
.jpg)
Figure 3. Storage modulus (E’) and loss modulus (E’’) spectra of polydimethylsiloxane at 25 °C. The green dashed and solid lines are storage and loss modulus as measured with bulk DMA. The light blue ‘x’ were from an instrumented nanoindenter, while the dark blue ‘○’ and orange ‘Δ’ used AFM-nDMA in either the Santa Barbara lab or in a collaborator’s lab.
There is very good agreement among all these methods for both E’ and E”: only about 5% RMS divergence between bulk and AFM-nDMA for E’, and about 25% for E’’. Notably, it is important to observe the difference in frequency ranges accessible by the two methods. While it is typical for DMA and indenter methods to only measure moduli at frequencies up to around 200 Hz, the AFM-nDMA method facilitates measurements at up to 20,000 Hz with the addition of an external actuator.
As discussed above, master curves are vital tools for polymer scientists to explore viscoelastic properties over a wide range of frequencies and temperatures. The first step towards creating a master curve is to collect a series of viscoelastic spectra at different temperatures.
Figure 4 shows the storage modulus (blue) and loss tangent or tan δ (orange) acquired via AFM-nDMA over a temperature range from 25 °C to 130 °C and a frequency range of 0.1 to 100 Hz on fluorinated ethylene propylene (FEP).
With the increase in temperature, the material becomes pliable as demonstrated by a lowering of the storage modulus. The 90°C peak in the loss tangent is due to the material's glass transition temperature (Tg). As expected, the peak in loss tangent and softening occur at higher temperatures when the measurement is conducted at higher frequencies. Therefore, in shifting the series of curves from Figure 4, a master curve for FEP loss tangent is then generated.
.jpg)
Figure 4. AFM-nDMA storage modulus (left axis) and loss tangent (right axis) of fluorinated ethylene propylene. The blue squares are storage modulus versus temperature plots at 0.1, 1, 10, and 100 Hz (darkest to lightest blue respectively), while the brown circles are the loss tangent plots at 0.1, 1, 10, and 100 Hz (darkest to lightest brown).
Figure 5a illustrates that the loss tangent master curve from the AFM-nDMA data (blue ‘○’) compares favorably with bulk DMA (green ‘∆’). These master curves cover an exceptionally wide range of frequencies of about 24 decades. Consequentially, the calculation of activation energy is enabled due to the shift factors used to generate the master curves (Figure 5b). The activation energy from the AFM-nDMA master curve (490 kJ/mol) replicates particularly well to that from the bulk DMA master curve (489 kJ/mol).
.jpg)
Figure 5. Time-temperature superposition analysis of FEP: (a) losstangent master curves from AFM-nDMA (blue ‘○’) compared to that from bulk DMA (green ‘Δ’); (b) TTS shift factor versus 1/T plot for Arrhenius activation energy analysis. Linear fits give activation energies from bulk DMA and AFM-nDMA of 489 and 490 kJ/mol, respectively.
One of the most promising applications of AFM-nDMA is the ability to probe viscoelastic properties of highly localized spatial domains, a capability that is vital to many kinds of materials, including blends and nanocomposites.
A blend of polypropylene (PP) matrix with a 1 µm diameter domain of cyclic olefin copolymer (COC) can be seen in Figure 6. The progression of the viscoelastic properties of these two materials as a function of temperatures from 25 °C-175 °C is demonstrated in the series of 100 Hz AFM-nDMA storage modulus and loss tangent plots.
Both materials start at equivalent E’ values at ambient conditions, but quickly diverge as temperature increases and two materials move towards their respective thermal transition points. The loss tangent images exhibit inversion of relative loss tangents between the two materials at 175°C. E’ and tan δ values were calculated from their respective domains in the image and plotted in the corresponding graphs adjacent to the maps as a function of temperature.
.jpg)
Figure 6. Storage modulus (top row) and loss tangent (bottom row) of a PP-COC blend: (a) 100 Hz AFM-nDMA maps with increasing temperature (500 nm scale bar); (b) plots of storage modulus and loss tangent at 0 Hz versus temperature. Blue circles were measured within the COC domain and red triangles were from the PP matrix.
Conclusions
It is now possible to obtain quantitative viscoelastic property measurements of nanoscale domains in heterogeneous polymeric materials. AFM-nDMA directly conveys the frequency and temperature dependence of viscoelastic properties in the rheologically relevant range, evading any potential pitfalls of traditional AFM imaging modes.
As demonstrated in the PDMS test case, E’ and E’’ the values contrast very well with bulk DMA measurements from 0.1 to 200 Hz (and can be extended to 20,000 Hz using an external actuator). Full TTS analysis of FEP results over a reliable range of temperatures and frequencies in agreement with bulk DMA and produces the expected Arrhenius activation energy.
Additional measurements on a blend of PP and COC can demonstrate viscoelastic property mapping and the importance when taking into consideration the temperature and frequency to understand even qualitative material behavior.
AFM-nDMA adds a robust, quantitative capability for measurement of viscoelastic properties, which compares well with tried and tested techniques established over time while enabling investigations of the microstructure as well as bulk properties of heterogeneous polymers.
Watch the Webinar
AFM | Measuring Nanoscale Viscoelastic Properties with nano-DMA | Bruker
References
- B. Pittenger, N. Erina, and C. Su, “Quantitative Mechanical Property Mapping at the Nanoscale with PeakForce QNM,” Bruker Application Note AN128, doi: 10.13140/RG.2.1.4463.8246, 2010.
- M. Radmacher, R. W. Tillmann, and H. E. Gaub, “Imaging viscoelasticity by force modulation with the atomic force microscope,” Biophys. J., vol. 64, no. 3, pp. 735–742, Mar. 1993.
- T. Igarashi, S. Fujinami, T. Nishi, N. Asao, and K. Nakajima, “Nanorheological mapping of rubbers by atomic force microscopy,” Macromolecules, vol. 46, no. 5, pp. 1916–1922, Mar. 2013.
- B. Pittenger and D. G. Yablon, “Improving the Accuracy of Nanomechanical Measurements with Force-CurveBased AFM Techniques,” Bruker Application Note AN149, doi: 10.13140/RG.2.2.15272.67844, 2017.
- M. E. Dokukin and I. Sokolov, “On the Measurements of Rigidity Modulus of Soft Materials in Nanoindentation Experiments at Small Depth,” Macromolecules, vol. 45, no. 10, pp. 4277–4288, May 2012.
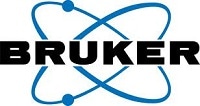
This information has been sourced, reviewed and adapted from materials provided by Bruker Nano Surfaces. For more information on this source, please visit Bruker Nano Surfaces.