Celebrating its 100th anniversary this year, Olympus is a global technology leader that provides innovative nondestructive testing and measurement solutions for a wide range of industries, including steel manufacturers.
Alex Thurston is an expert on Olympus’ X-ray fluorescence (XRF) and X-ray diffraction (XRD) technologies. His knowledge about XRF applications and his expertise in materials science and metallurgy are the basis of this interview where he offers insights into the benefits of steel slag monitoring using handheld XRF.
What is slag analysis?
Slag analysis is performing compositional analysis on metal-processing-derived slag material to determine constituent elements and compounds.
What benefits can slag analysis bring if used efficiently and implemented correctly into applications?
By monitoring slag composition, steelmakers can achieve three benefits: efficient slag creation during their processes, increased efficiency for both material and energy use, and, ultimately, production of cleaner and better quality steel or alloys.
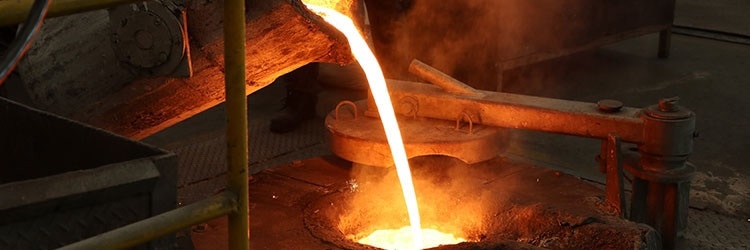
What factors need to be considered for slag analysis and steel slag monitoring?
When using handheld XRF for monitoring slag, your sample presentation is key. If the slag can be ground and pressed into a sample, this is best. However, for quick results at the furnace, a rough crush that is analyzed using an averaging feature on the instrument can yield helpful results for a steelmaker.
Ideally, the user is looking to determine the balance of certain oxides in the produced slag, typically silicon dioxide (SiO2), calcium oxide (CaO), aluminum oxide (Al2O3), and iron oxide (FeO). The ratio between these oxides determines the form and effectivity of the slag created during the process. Producers can help ensure these oxides are balanced by adding material during production. The right balance can help extend the life of the furnace refractory lining, as the slag will not consume material from the lining to constitute the slag.
What role does X-ray fluorescence play in in-process steel slag monitoring? Can you explain further?
Traditionally, slag analysis was conducted by steelmakers on older benchtop XRF equipment in a remote laboratory, if at all. Analysis samples had the potential to stack up over time, and the lag from the time the heat was processed to when the lab results were available was not always conducive to real-time slag analysis. This creates a reactive monitoring cycle.
With advancements in handheld XRF equipment, the same or better lab analysis has been transferred to a portable system, which can be easily carried to the furnace to speed up response time in slag monitoring. This can help the producer make informed, proactive trim additions to the alloy or slag to improve and complete processing of the heat.
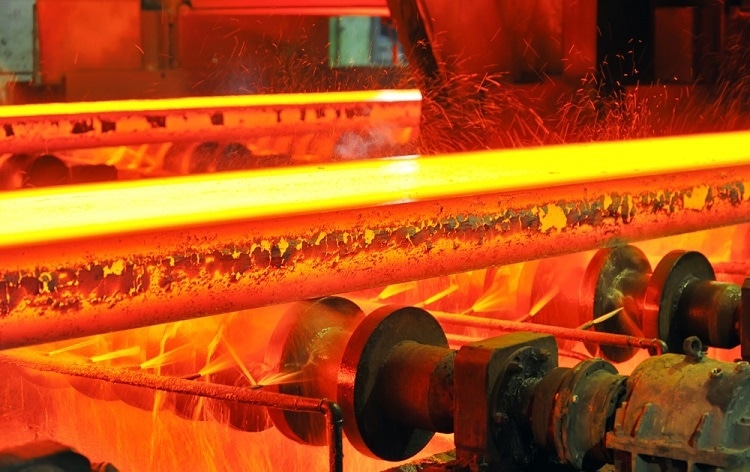
Which applications and industries will benefit most from improvements such as cleaner alloys and prolonged refractory lining life?
Alloy manufacturers and producers alike can benefit from slag analysis from a materials, energy, and quality cost perspective by ensuring their slag composition is optimized.
Handheld X-ray fluorescence analyzers from Olympus can be used as an important part of slag analysis and steel slag monitoring. Can you tell us the features and benefits of HHXRF in slag analysis and steel slag monitoring?
The Olympus Vanta™ XRF analyzer provides onboard, real-time calculations for the oxide content and basicity ratios that are needed for slag analysis. In addition, the performance gains enable users to determine if valuable alloying elements and additions are being drawn into the slag or if they are alloying the in-process metal as intended. The Vanta analyzer’s user-configurable data exporting offers a simple path for analysis results to integrate into a production system.
In addition to slag monitoring, alloy analysis can be accomplished with the same instrument, providing the same high level of accuracy and precision for trace levels of alloying content. Similarly, the instrument can be used to provide incoming inspection of raw materials to ensure that they have been delivered as ordered.
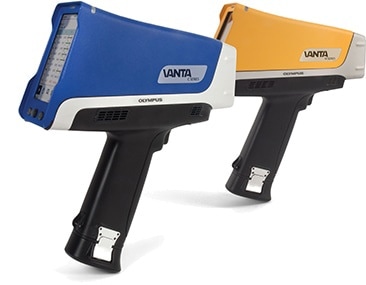
Why are handheld X-ray fluorescence analyzers the chosen method for steel slag monitoring? How do they compare to other methods?
With recent advancements in handheld XRF, the precision and accuracy of the results rival many benchtop systems. These performance gains coupled with the portability of the instrument reduces analysis time and effort for many applications that had to use lab results in the past.
Data analysis in slag monitoring is extremely important. How do handheld X-ray fluorescence analyzers help with this?
With modern features like network folder data export enabled on a handheld XRF instrument, real-time data entry into a production monitoring system is achievable. Quality operations can be strengthened by creating an overall picture of their process, using basicity calculations for heat slags in conjunction with the alloy composition.
Where can our readers go to find out more?
www.olympus-ims.com
https://www.olympus-ims.com/en/insight/aistech-2019-our-latest-for-the-steel-industry/
About Alex Thurston
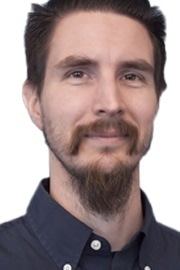
Alex Thurston is an Applications Engineering Manager at Olympus Scientific Solutions, in Waltham, MA, where he leads a team that helps customers develop and institute new uses for XRF and XRD products. Prior to working with Olympus, Alex spent years in the metals manufacturing industry, casting and forging both ferrous and non-ferrous metals. His technical background is in metallurgy and materials science, having earned a master’s degree from Case Western Reserve University.
Disclaimer: The views expressed here are those of the interviewee and do not necessarily represent the views of AZoM.com Limited (T/A) AZoNetwork, the owner and operator of this website. This disclaimer forms part of the Terms and Conditions of use of this website.