Cleaning employees aboard a Boeing 787 aircraft observed smoke in the rear cabin on January 7th 2013. Further inspection by a mechanic found the presence of a fire starting from the lid of the APU battery case.
Luckily, none of the 183 passengers and 11 crew were hurt as the plane was stationed at Logan International Airport, USA at the time.
On January 16th 2013, nine days later, a Boeing 787 had to make an emergency landing at Takamatsu Airport, Japan, because of an issue caused by the primary lithium ion battery.
The Federal Aviation Administration (FAA) as a result, grounded the complete 787 ‘Dreamliner’ fleet, waiting for an investigation by the NTSB (National Transportation Safety Board).
A Serious Issue Overlooked
The NTSB investigation discovered that the most probable source of the fires was an internal short circuit inside of a cell within the lithium ion battery.
This short circuit results in a ‘thermal runaway’ which causes the heating of nearby cells, creating excessive fire, heating and possibly even an explosion.
Boeing’s 787 aircraft were the first to utilize huge lithium ion batteries and discovered some of the challenges the hard way.
The final conclusion was that FAA, the battery manufacturer, and Boeing did not entirely comprehend the dangers related to lithium ion batteries.
It is not the first occurrence where lithium ion batteries have created issues on an aircraft. Only this year, the FAA published a list online that outlines 258 distinct events involving explosion, extreme heat, fire, or smoke from lithium ion batteries from March 1991 to May 22nd 2019.
The International Civil Aviation Organization has put stringent rules in place regarding the air transportation of LiB since April 2016 and the US has followed its example this year.
Why do lithium ion batteries involve so much risk? What can manufacturers do to reduce this risk?
What Causes LiBs to Overheat?
The NTSB investigation discovered that an internal short circuit inside of the cell of the battery was the source of the fires.
The short circuit results in too much current flow, which heats the cell in a way that causes it to ignite. It is commonly now thought that fine metal particles from contaminants inside of the cell are what initiates the short circuiting. This can occur through one of two processes:
- Chemical Short
Very small metal particles of 20 to 50 µm inside of the electrolyte close to the cathode ionize in this case.They are attracted towards the anode due to the positive charge of the ionized atoms. As they travel near the anode, they enter the cell separator which results in a short circuit from cathode to anode side.
- Physical Short
If large metal particles are present in the cathode electrolyte, for example more than 100 µm, then they are big enough to make a hole in the separator and transport the current specifically from the cathode through the anode side, which again causes a short circuit.
To make sure operations are safe, battery component providers and battery manufacturers must identify and decrease metal contaminants in production. The following are some areas where contamination must be kept to a minimum:
- Conducting enhancer
- Slurry formation process
- Anode and cathode material
- Drying and coating process
Establishing the density and size of metal particles in these areas will assist in avoiding in-the-field failure of the kind that grounded the whole fleet of Boeing 787s.
Introducing the EA8000 X-Ray Particle Contaminant Analyzer
Hitachi High-Tech has created an X-ray particle analyzer especially for the identification and analysis of metal contaminants inside of lithium ion batteries.
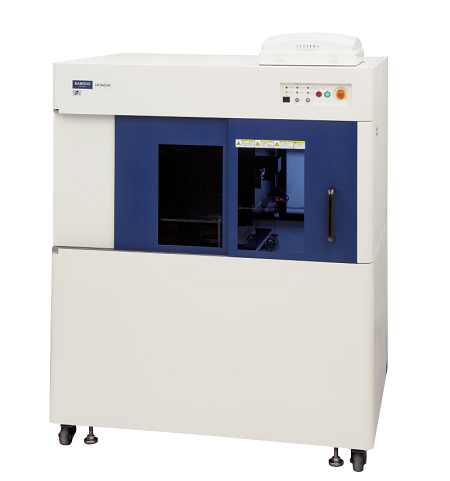
With high precision and accuracy at incredibly efficient measurement times, the EA8000 can be utilized to uphold quality throughout the production of lithium ion batteries.
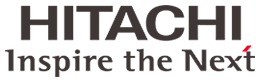
This information has been sourced, reviewed and adapted from materials provided by Hitachi High-Tech Analytical Science.
For more information on this source, please visit Hitachi High-Tech Analytical Science.