Save time and improve the probability of detection in videoscope inspections of wind turbine gearboxes through intelligent illumination, maneuverability, and an oil-clearing tip. The IPLEX™ RX videoscope’s oil clearing tip adaptor uses capillary action to draw oil away from the lens, so gearbox inspections can continue with less loss in time from tip extraction and manual cleaning when the scope tip comes into contact with oil.
Among the most time-consuming and difficult videoscope inspections is checking the inside a wind turbine’s gearbox. Detecting damage is difficult for inspectors due to the combination of the gearbox’s large size, dark conditions, reflective metallic surfaces, and the presence of oil.
Their extreme operating conditions make wind turbine gearboxes particularly vulnerable to damage. A small defect could easily cause gearbox failure or even a turbine fire due to the high speeds and high stresses.
Potential damage can be continuously monitored using measurement tools, such as vibration sensors. However, as shown in Figure 1, only remote visual inspection (RVI) can provide a thorough analysis of the state of a gearbox.
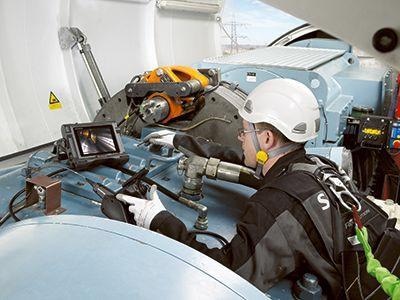
Figure 1: A look in the gearbox. Turbine inspectors use videoscopes as a quick, efficient way to detect gearbox damage. Image Credit: Evident Corporation
Inside a Wind Turbine Gearbox
The gearbox converts the slow rotation of the blades and the low-speed shaft into a fast rotation to drive the generator. As shown in Figure 2, there are a series of transmissions involved in this process. Each transmission must be thoroughly examined during an inspection, including the gear teeth and the bearings that support the shafts.
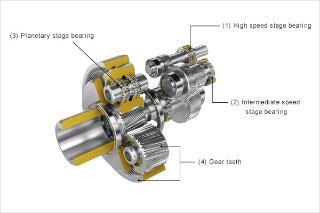
Figure 2: Gearing up. The turbine’s generator is driven by the blades through a series of transmissions. Image Credit: Evident Corporation
There are typically three shafts within a wind turbine gearbox: the low-speed shaft, the intermediary shaft, and the high-speed shaft. Directly driven by the blades, the low-speed shaft only rotates at a speed of between 20 and 30 revolutions per minute (RPM). However, the low-speed shaft must be able to absorb extra stresses caused by strong winds. While the high-speed shaft is better protected against adverse weather, it is still vulnerable between 1500 and 1800 RPM.
Stage bearings surround all three shafts, providing support by preventing lateral motion. From an inspector's point of view, some of these bearings are in difficult-to-access locations, particularly the planetary stage bearings that support the low-speed shaft.
Create Sharp Images with the Oil Clearing Tip Adaptor
All gears and bearings are lubricated with oil during operation, so the tip of the videoscope may come into contact with oil during the inspection, leading to blurred images. When this happens, the tip normally must be retracted and cleaned before being reinserted into the gearbox. An attempt must then be made to try and find its last location. Alternatively, before the inspection is carried out, the oil can be drained from the gearbox. However, this only adds to the overall inspection time.
Evident has developed a dedicated oil clearing tip adaptor for the IPLEX RX videoscope to save time for inspectors. The risk of blurred images is greatly reduced with this tip. Capillary action draws oil through grooves located on the adaptor’s side to draw oil away from the lens without the need for tapping or cleaning while the scope tip is inside the gearbox.
Smart Illumination and Maneuverability with the IPLEX RX Videoscope
Videoscopes need to operate to the best of their capabilities to reach every corner of the gearbox and to take images that provide reliable information about the state of the different components. Illumination is one important capability. When trying to produce images with the optimal brightness and contrast for reliable damage detection, the combination of large, dark spaces and highly reflective metallic surfaces is challenging.
The Evident IPLEX RX videoscope is equipped with PulsarPic™ processing to automatically adjust the light intensity. This addresses the issue of uneven brightness across the field of view of the camera. Light output is provided based on the conditions inside the gearbox using this intelligent illumination processor, producing clearer images with less noise and improving the probability of detection (see figure 3).

Figure 3: In the spotlight. Adaptive illumination improves the probability of detecting flaws in dark spaces. Image Credit: Evident Corporation
Poor maneuverability of the scope tip can slow down the inspection of large systems. A significant amount of time during an inspection is spent maneuvering towards a target. The time required to move the scope tip can be reduced with flexible and fast articulation, meaning that more time could be spent on visual inspection and capturing images.
The TrueFeel power-assisted manual articulation on the IPLEX RX videoscope combines adaptive articulation with an intuitive interface to improve the inspector's hand-eye coordination. It is easy to move through narrow openings without damaging the scope tip thanks to good maneuverability and adaptive illumination.
Summary
The complex challenges of wind turbine gearbox inspections, such as size, complexity, lighting conditions, narrow openings, and the presence of oil, can all be met using videoscopes fitted with an oil clearing tip adaptor. However, several key features of the videoscope, such as adaptive illumination, intuitive maneuverability, and oil resistance, all heavily influence the speed and precision of the inspection. All of these innovations are all available with the Evident IPLEX RX videoscope, helping save time and producing clearer images. These features improve the probability of detection and contribute to wind turbine safety.
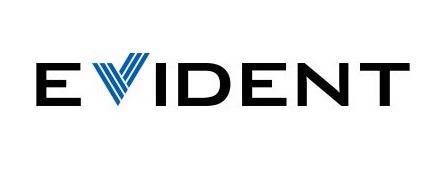
This information has been sourced, reviewed and adapted from materials provided by Evident Corporation.
For more information on this source, please visit https://www.evidentscientific.com/en/