A new EU directive transformed the metal recycling industry in October 2011.
Responding to the research carried out by the European Commission, the regulation influenced scrap metal and laid out particular guidelines to establish when steel, aluminum, and iron scrap cannot be classed as waste and can be employed as feedstock for foundries, aluminum refiners, steelworks.
The use of scrap metal rather than raw material helps to solve many environmental challenges, including the increased difficulty and expense of extracting ores and what can be done with the large amounts of waste scrap metal.
The system to remelt scrap uses less energy than the use of raw materials which in turn generates less of the greenhouse gas, CO2.
At the core of the directive is making sure that the waste fulfills the technical needs of the metal producing industry, such as adherence to established legislation on hazardous materials.
The ‘end-of-waste’ scrap must be put through a process of recovery that produces steel, iron, and aluminum that is low in non-metallic compounds and free of hazardous features.
To fulfill the criteria for non-waste, recycling organizations must offer quality information about the metal that has been processed in their system and prove that a reliable quality management system is in use.
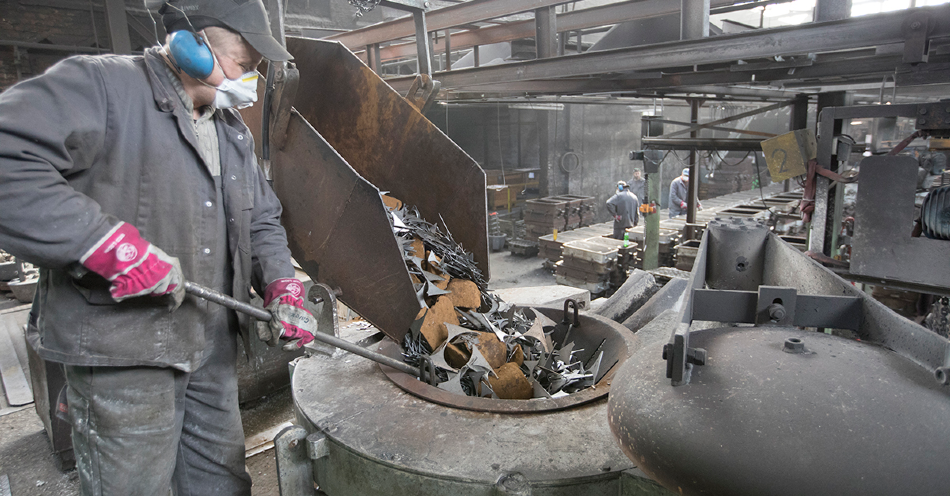
Image Credit: Hitachi High-Tech Analytical Science
Implementing a Quality System for End-Of-Waste Scrap Metal
Steel, aluminum, and iron scrap must be graded in relation to an industry specification, customer specification or to a standard that is appropriate for direct use by foundries or steelworks.
For steel and iron, the total amount of foreign materials can not be greater than 2% by weight, where foreign materials are combustible non-metallic materials, non-ferrous metals, non-conductors of electricity, and residues (for example sludge or dust).
The criteria for aluminum are similar, but the total amount of foreign material can not be greater than 5% by weight.
The quality management system of a recycling facility should cover the following:
- Management of the kind of waste appropriate for classification as non-waste scrap and processing
- Recording of the treatment processes to eliminate substances, such as in ELV processing
- Tracing the quality of the scrap metal, entailing analysis and sampling
- Customer feedback, such as foundries and metals processing facilities
- Keeping a record of results monitoring
- Review of system and employee training
Analysis of Scrap Metal Using the OE750
The OE750 is an innovative new OES spark spectrometer by Hitachi High-Tech. With a degree of detection performance unparalleled in an instrument of this class, the OE750 offers cost-effective metals analysis for scrap metal recycling facilities.
The OE750 can identify all trace elements in steel, aluminum, and iron to the smallest limits of detection for example. This means that it can identify zinc in steel to a degree of 0.5 ppm. It can measure lead and boron in cast iron to less than 10 ppm.
Created to be efficient and simple to use, the OE750 is dense and robust, making sure that it fits easily into existing metals recycling processes and helps the customer to meet the end-of-waste metals standards.
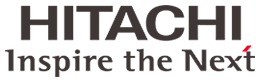
This information has been sourced, reviewed and adapted from materials provided by Hitachi High-Tech Analytical Science.
For more information on this source, please visit Hitachi High-Tech Analytical Science.