When characterizing the strain rate sensitive deformation mechanics of materials, high strain rate testing is essential. Conventionally, in a standard nanoindentation test, a load is applied to the sample surface using a probe tip with sub-micrometer (µm) dimensions.
The material displacement that follows is then analyzed by virtue of being measured to gauge various mechanical characteristics, including strain rate sensitivity. The flow stress and the strain rate produced beneath the indenter can be used to produce this result. However, when it comes to unpredictable material behavior in response to extreme stress, the load-displacement curve predicted from low strain rate testing cannot account for this.
Historically, when assessing the strain rate dependence of materials, nanoindentation techniques were typically limited to constant rate, constant rate of load and hold, constant rate of loading, or strain rate jump testing.
Subsequently, these are restricted to low and intermediate strain rates. These low and intermediate strain rates are unable to test the dynamic flow stress of materials, which is a vital characteristic of materials in a wide range of metalworking and structural engineering applications.
Alemnis has engineered the development of a unique high strain rate module (HSRM) specifically for materials testing at extremely high strain rates. These high strain rates can go up to 10,000 s-1. This article will now explore this nanoindentation high strain rate module in more detail.
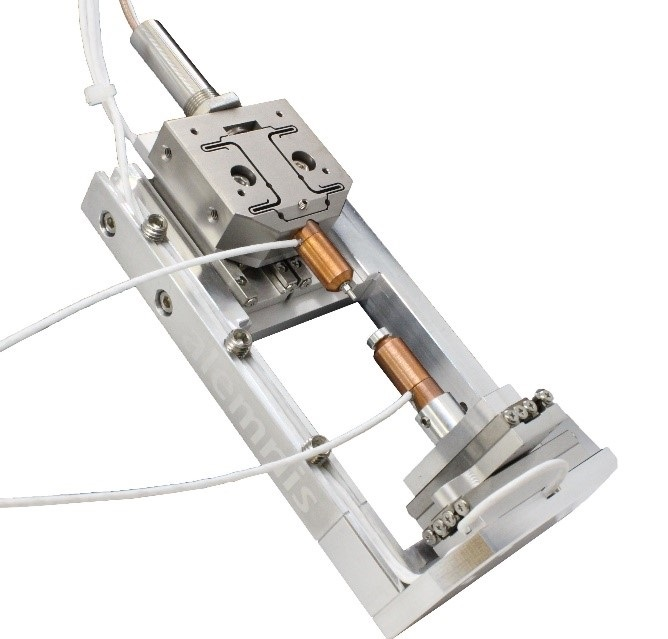
Alemnis Ultra High Strain Rate (UHSR-3-3) module allowing 3-axis actuation and sensing to give controlled strain rate up 10’000 s-1. Image Credit: Alemnis AG
Alemnis High Strain Rate Module
The high strain rate module, at Alemnis, has been developed with the same underlying piezo technology as their standard nanoindenter, but has an increased excitation and sensing range (>10 kHz). These alterations enable actuation across three measurement axes, with an axial of 0.7 µm and an actuation range of 1 µm x-y. Accurate displacement control along all three axes can provide extremely precise nanoscale measurements with extremely high strain rates. It is possible, under certain conditions, to attain strain rates of 10,000 s-1.
Using nanoscale samples, this module helps with the characterization of dynamic deformation characteristics, in response to high strain rates.
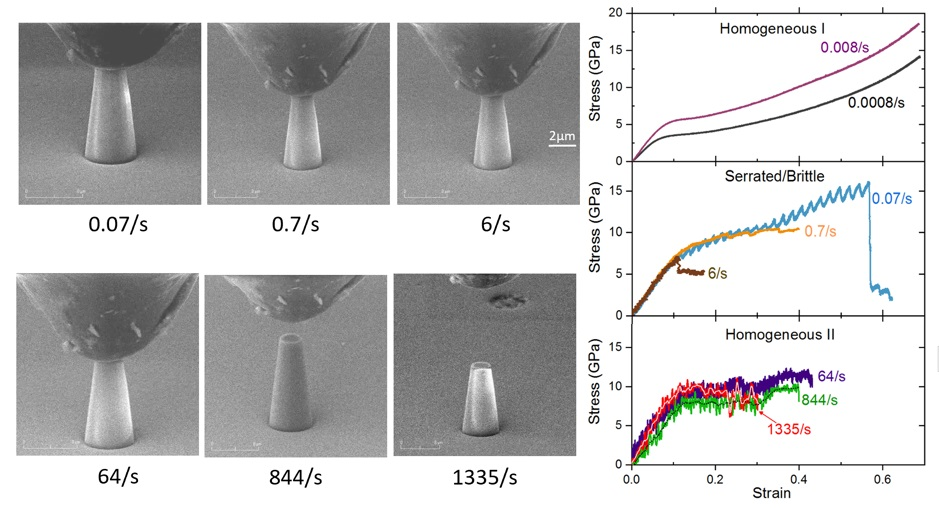
Rate-dependent response of silica micropillars subjected to strain rates from 0.07/s up to 1335/s with their corresponding stress-strain curves from 0.0008/s up to 1335/s which represents 8 orders of magnitude (from R. Ramachandramoorthy et al, Nano Letters 19 (2019) 2350-2359). Image Credit: Alemnis AG
How to Undertake High Strain Rate Testing
Micro-pillar compression is one method that can be used to perform high strain rate testing. Beneath the nanoindentation probe, a microscale column of the sample material is immobilized on the positioning stage. Subsequently, the entire high strain rate module is transported to the chamber of a scanning electron microscope (SEM) whereupon the tip is mechanically aligned using precise servo motors. To compress the micro-pillar and determine various properties like fracture strength and fatigue stress, strain rates of up to 10,000 s-1 can then be applied. The Alemnis Standard Assembly (ASA) fitted with a High Strain Rate (HSR) module provides a unique system capable of spanning up to 8 orders of magnitude of strain rate.
For dynamic testing of strain rate dependent deformation characteristics of materials as varied as ceramics, refractories, composites, polymers, and metal alloys, this is a significant new development which is paving the way for a better understanding of how materials react to strain rates over several orders of magnitude. When coupled with either high or low temperature modules, this is opening the path to a more complete picture of material deformation which was previously not possible by conventional techniques.
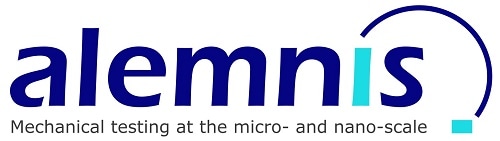
This information has been sourced, reviewed and adapted from materials provided by Alemnis AG.
For more information on this source, please visit Alemnis AG.