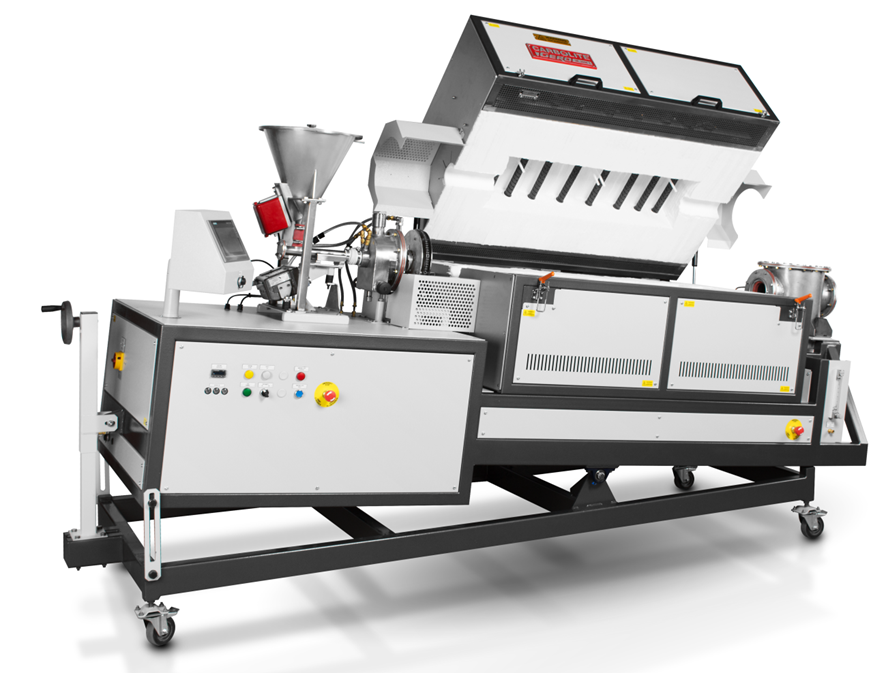
Although industrial furnaces have been used since the beginning of the industrial revolution, it is only in the 20th century that great strides have been made in the technology behind the heating and the movement away from fuel-driven systems. Carbolite Gero is a global manufacturer of electrically heated ovens and furnaces and they have been at the forefront of this technology for the past 80 years.
The First Furnaces
Carbolite was first founded in 1938 in Sheffield, England, taking its name from the silicon carbide heating elements that were just coming into use1. This was the novel technology of the time, and this approach to innovation can be seen in the way the company conducts its business to this day.
The original furnaces built in Attercliffe were designed for testing coal and coke used in Sheffield’s steel industry, but as the company quickly developed a reputation for quality, they were soon building furnaces for the precious metals sector, as well as ash fusibility furnaces for sample testing. It was this diversity and ability to offer custom solutions that set them apart from other manufacturers who have adopted a more “one size fits all” approach.
Carbolite Gero’s Furnaces Today
Carbolite Gero has since grown into a major worldwide producer of furnaces, with an annual turnover approaching £30m2. Producing over 1,000 ovens and 4,000 furnaces every year at their facilities in Hope, Sheffield and Neuhausen, Germany. Between these two sites, there are 200 scientists, academics and highly trained staff, who oversee the research and development of the company’s extensive product range and ensure that they remain at the cutting-edge.
This includes products such as the GPCMA/174 Retort Furnace, the design of which has recently been overhauled3. This furnace offers heat treatments up to 1150 °C, and is ideal for any number of applications, from laboratory research up to industrial-scale production. Delivering superior results for a low cost, it is perfect for use in rapid prototyping, as well as the fabrication of one-off components.
Custom furnaces are also a significant source of revenue for Carbolite Gero, who fulfil bespoke orders for organisations around the world. Among the many customers who have commissioned one-of-a-kind solutions are metal component manufacturers, university research departments, start-up battery companies and aerospace clients requiring compliance to exacting Nadcap standards.
Modern Solutions
As well as improving the operational capabilities of the furnaces, user interaction is also considered. The CC-T1 touch-screen controller is now available for many of the furnaces in the current product range4. This provides a touch-screen interface that allows the user to access a comprehensive menu including the selection and editing of program profiles; scheduling of programs, and data logging of custom points. The CC-T1 series also has memory for up to 10 unique program profiles for operators that are not just running a single procedure.
It is not just the furnaces that have seen modernization. Recently Carbolite Gero’s insulation manufacturing facility has been upgraded with a robotic machining cell. As well as cutting production times down, it has improved the accuracy of the machining process, leading to a reduced amount of excess material and a cleaner manufacturing environment in the facility.
References and Further Reading
- Pelissier, K., Chartier, T. & Laurent, J. M. Silicon carbide heating elements. Ceram. Int. 24, 371–377 (1998).
- Heating up the market. Manufacturing Today
- GPCMA/174 Retort Furnace for Powder Metallurgy & Additive Manufacturing. Available at: https://www.carbolite-gero.com/news/news-details/news_detail/gpcma-174-retort-furnace-for-powder-metallurgy-additive-manufacturing.
- CC-T1Touch Screen Controller. Available at: https://www.carbolite-gero.com/products/control-options/cc-t1-controller/function-features/.
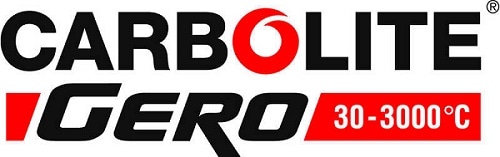
This information has been sourced, reviewed and adapted from materials provided by CARBOLITE GERO Ltd.
For more information on this source, please visit CARBOLITE GERO Ltd.