Stainless steels can be found in all areas of modern society. They are manufactured into plates, sheets, wires, tubing, and bars to be designed into every possible type of equipment and material.
It can be challenging to ensure that the correct grade is deployed for the desired purpose. With over 100 individual grades of stainless steel available, all of which look similar, how can one be sure that the right grade is used for the intended purpose?
The Need for Testing
Quality Control (QC) and Positive Material Identification (PMI) instruments have become essential pieces of equipment for robust material verification programs.
These tools assist in verifying that the appropriate grade of stainless steel is used in the right place at the right time. Using an incorrect grade can have results that are as basic as monetary loss, or as damaging as the loss of life.
Explosions in chemical and petrochemical plants are strong reminders of the risks of utilizing the wrong alloys. The majority of industries work to confirm the quality of products by analyzing the raw materials employed throughout the system of production.
The Mill Test Report (MTR) is one material verification method among others that can be used to verify goods.
In some examples, the MTR can be incorrect or untrustworthy as a result of confusion in the labeling process. It is best practice to carry out a second validation of the MTR to approve goods.
Any issues can be caught early at the forefront of inspection by utilizing elemental analysis. This avoids the expensive issue of finding out that goods have been produced out of specification after value has been added to them during the fabrication process. In many circumstances, the resulting goods must be completely disposed of.
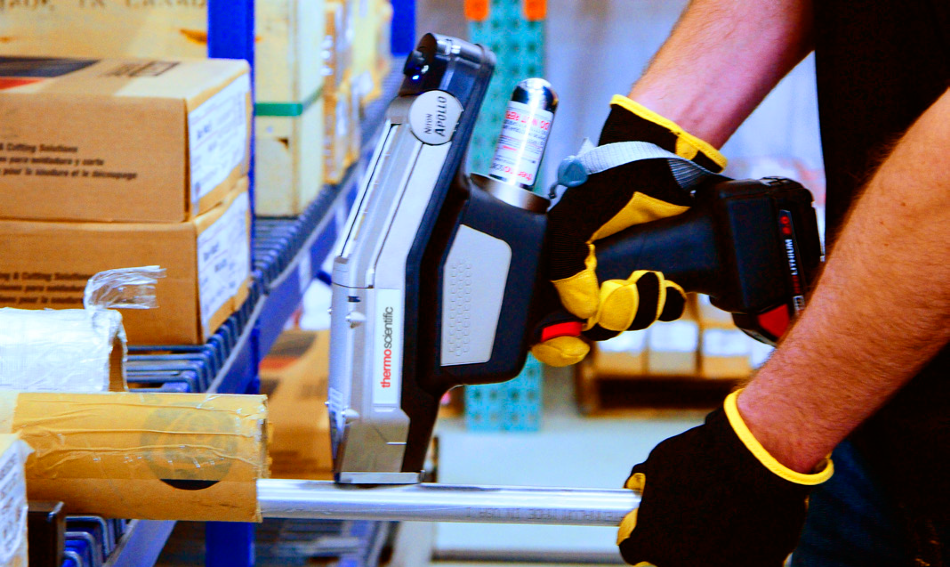
Figure 1. The Niton Apollo in use, validating a Mill Test Report (MTR) prior to fabrication.
Material verification is not only used for planned inspections. QC managers and supervisors have to verify that the right materials are utilized throughout the process of production.
Best practice requires elemental analysis – often for regulatory compliance. Testing may follow the part, assembly, or equipment right through to a
final validation before shipping.
An incoming inspection is commonly carried out again once the goods have been received by the customer. Inspections continue along the path to the final use. Inspections can ensue right up to the installation stage, particularly in critical processes.
In installations made before the emergence of the inspection process (such as thirty-year-old refineries), an operating refinery may be shut down so that in-process materials can be tested, which may not have had sufficient testing when first installed.
Test Equipment Challenges
Both OES (optical emission spectroscopy) and XRF (x-ray fluorescence) have been used in the past to perform the elemental validation of materials.
When testing was first established, the extensive instrumentation needed to verify materials was only found in laboratories. In-process and in-field testing are now possible with the miniaturization of laboratory technologies.
Carbon (C) is a significant alloying element that is introduced to stainless steel to enhance its strength and hardness. The analysis of carbon has been difficult to date. The most commonly used material verification technique, handheld x-ray fluorescence (XRF), is unable to identify carbon content.
While Optical Emission Spectroscopy (OES) can identify carbon, it is only supplied in bulky, large carts, which makes it challenging to use in awkward field surroundings (such as tight spaces, ditches, catwalks, ladders, and more).
Carbon content can vary between 0.005% to 1.2% according to the grade of stainless steel. A high carbon content is not sought after in particular kinds of stainless steel, specifically in welding because of the risk of carbide precipitation.
Due to these reasons, the identification of carbon is crucial for thorough verification of grade and to ensure risk-free operation for the long term.
Niton Apollo Handheld LIBS Analyzer
There is a new tool available to professionals performing material analysis. The Thermo Scientific™ Niton™ Apollo™ handheld LIBS analyzer uses Laser Induced Breakdown Spectroscopy (LIBS) to perform material inspection during the fabrication process.
With a weight of only 6.4 lbs. (2.9 kg.), the Niton Apollo is designed to analyze carbon content in a portable, convenient form factor. In many cases, the requirement for large Optical Emission Spectroscopy (OES) carts is removed.
Showcasing a powerful laser and a high purity argon purge, the Niton Apollo can verify MTRs, remove the dangers related to the welding of incompatible alloys, and can even discriminate between similar alloy grades.
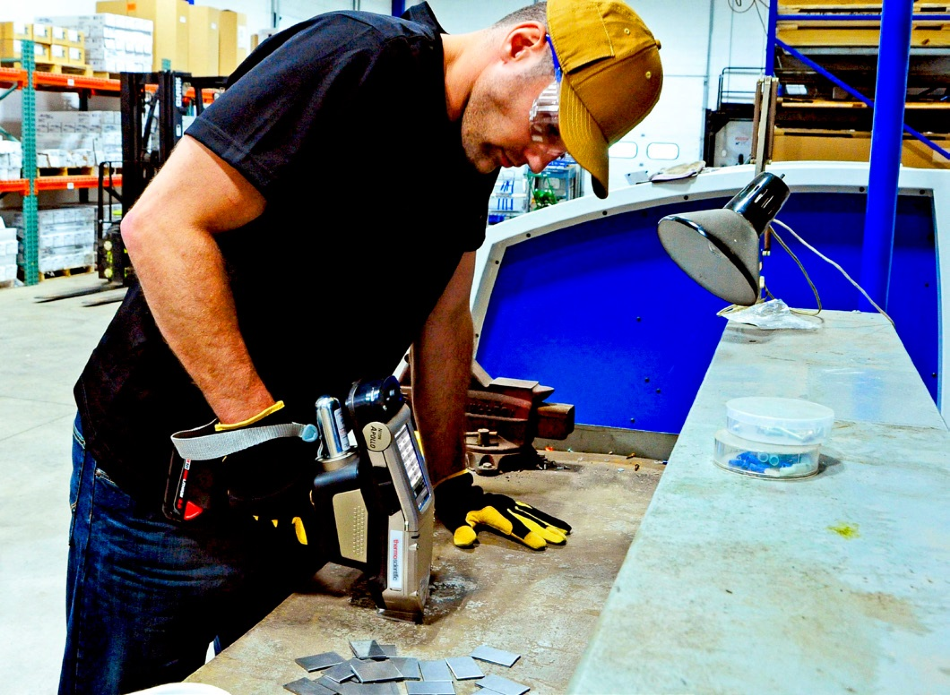
Configured to offer high-quality results, the Niton Apollo can quantify low carbon levels in L grade stainless steel of an estimated 100 to 300 ppm (parts per million).
For example, this sensitivity allows the Niton Apollo to distinguish the amount of carbon in 304L with ~300 ppm or ~0.03% carbon, from the ~0.06% level in a 304 grade.
Alternative examples of the requirement to test for carbon are 316 vs. 316L or 316H, and 317 vs. 317L. To date, low levels of carbon in stainless steel while in the field have only been quantifiable by large, bulky OES analyzers until recently.
Conclusion
The Niton Apollo handheld LIBS analyzer can be utilized to establish the concentration of carbon for quality control (QC) in the fabrication industry. Its handheld form factor allows users to safely and conveniently carry out material verification directly in the field with laboratory-quality results and accuracy.
The main advantage of this forward-thinking design comes from its optimized repeatability, long-term stability, and accuracy. Thus making the Niton Apollo an essential tool for stainless steel material verification.
Acknowledgments
Produced from materials originally authored by Jim Pasmore from Thermo Fisher Scientific.
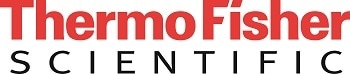
This information has been sourced, reviewed and adapted from materials provided by Thermo Fisher Scientific – Handheld Elemental & Radiation Detection.
For more information on this source, please visit Thermo Fisher Scientific – Handheld Elemental & Radiation Detection.