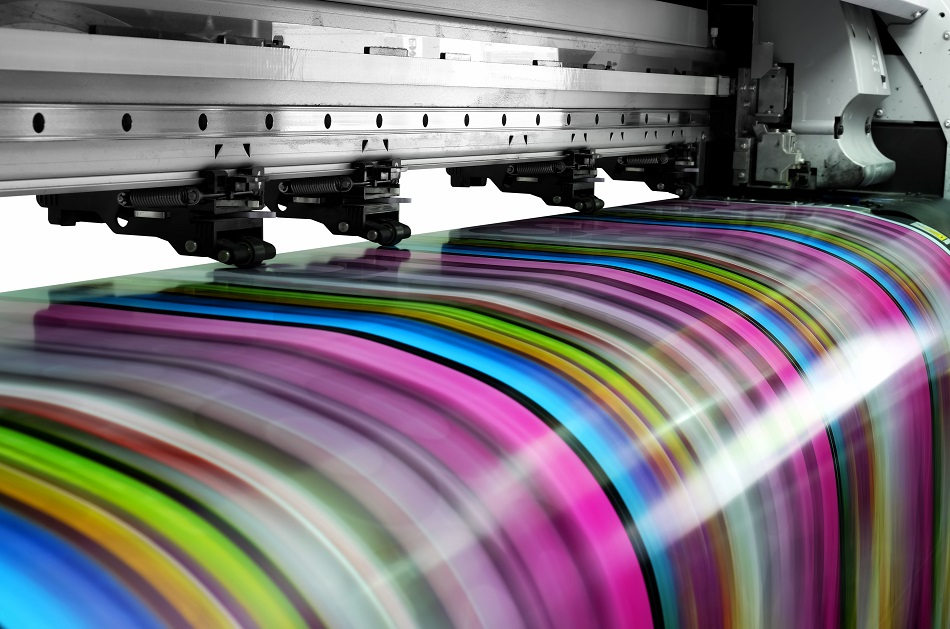
Image Credit: KOKTARO/Shutterstock.com
Today’s manufacturers are under myriad new pressures related to gaining a competitive edge in the modern marketplace which is ever-growing in complexity and evolving with technology and the changing needs of the consumer. For many companies, their major focus for standing out amongst their competitors lies within the packaging of their products. Packaging has evolved greatly over the years, and it is now a major point of distinction from competitors and fundamental in communicating key information to consumers, such as product quality; reliability; brand identity; how much the brand observes key ethical issues; whether the product meets certain regulations and standards; and with food and drink products, it communicates key nutritional information that is becoming increasingly important.
To deal with these new demands related to packaging needs, manufacturers' requirements on printing processes to create their packaging has changed. Conventional printing processes were set up to replicate a single design, often over long print runs, with little option for making amendments without occurring the cost of setting up an entirely new print run. However, modern manufacturers require the convenience of agility, responsiveness, and flexibility with their printing methods.
Because of this change in demands the digital printing market has expanded rapidly, with older printing methods such as screen and lithographic printing becoming increasingly less popular. This is because digital methods give printers the opportunity to make amends to print runs much easier than analog printing techniques.
Advancements are continuing to be made in the digital printing space to continue to help manufacturers meet their packaging needs. One technology that is changing the face of the market – offering speed, reliability, endurance, quality, and flexibility – is Inline Digital Printing (IDP).
What is ‘Inkless’ Inline Digital Printing?
IDP printing was designed to help manufacturers meet the new challenges presented by modern consumer markets. It merges together the technologies of laser-reactive materials and multi-laser arrays. With IDP, specialized coatings that are designed to change their color once exposed to a light source (laser-reactive materials) are combined with multi-laser array technology that uses specialized print heads to create the images that will be printed with the laser-reactive materials.
The combination of these two technologies to form the IDP method allows manufacturers to overcome the current challenges of printing product packaging, such as the need for high-speed production, high-quality print outcomes, and reliability and endurance of the printing system. IDP technology can print monochrome images as fast as 197 ft/min, and produce resolutions of 300 dpi. In addition, the lasers used are recognized as being one of the most long-lasting in the industry.
Chemical Technology
The laser-reactive coating used by IDP is applied directly to the material to be used as packaging. The coating is specially selected depending on what color it needs to be and what substrate it is being printed on. The converter applies the coating onto the substrate and it is then dried or cured. The coating appears white or colorless until it goes through the optical process.
Optical Technology
Multi-laser arrays are then used to create the images. The substrates that have the laser-reactive coating applied onto them are exposed to a laser beam, which creates the images by specifically shining light only on the areas where the color is to be exposed. The lasers pulse on and off, moving around the substrate to create the image. This could be monochrome by using a coating that turns black under light exposure and incorporating it with whitespace. These images can also be colored depending on the coating that is selected.
Sources and Further Reading
Disclaimer: The views expressed here are those of the author expressed in their private capacity and do not necessarily represent the views of AZoM.com Limited T/A AZoNetwork the owner and operator of this website. This disclaimer forms part of the Terms and conditions of use of this website.