Phenolic resins are frequently created for paper impregnation and gluing. They have exceptional product features in regards to material resistance and toughness, but can additionally cope with challenging production environments because of its reaction process.
One of the key physical characteristics of a polymeric or resin solution is its molecular weight, which directly corresponds to its viscosity.
This makes it possible to observe a resin manufacturing process and the reaction is terminated when the desired viscosity is attained.
Sofraser has produced a process viscometer that can control, monitor, and detect the many phases of the polymerization process. It is ideally suited to the varied requirements of the chemical industry.
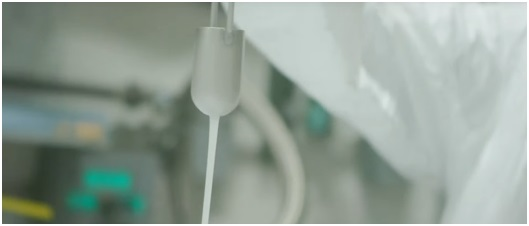
MIVI Viscometer: An Indirect but Efficient Means to Measure the Molecular Mass of Polymers
Polymers are high molecular mass molecules made up of repeating units known as monomers that are linked through covalent chemical bonds.
The batch has a low viscosity and is primarily composed of monomers at the beginning. The polymerization process begins once a catalyst and/or heat has been introduced. This causes the viscosity and molecular weight of the chains to increase.
As phenolic resins have exothermic reactions that are temperature-sensitive, the viscosity value should be closely observed. The MIVI viscometer offers immediate information that manages the stages of reaction.
If the reaction is too slow, the duration of manufacturing increases which results in low productivity and increased consumption of energy. If the reaction is exothermic and/or too fast, the result can be hardening, defective, and heterogeneous.
A resin with unappropriated consistency and viscosity can result in delivery delays and labor overhead. It may also require the replacement of equipment which is highly expensive.
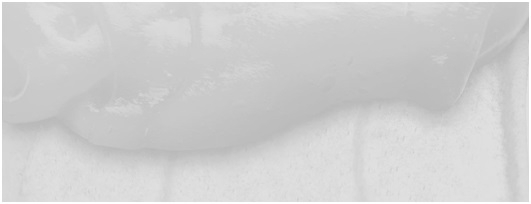
A Reliable Viscosity Instrument in Phenolic Resin Processes
Issues with viscosity in batch process polymerization can occur in reaction start detection, raw material control, reaction end-point detection, polymerization speed control, and end-product quality control.
Sofraser has innovated a direct insertion viscometer able to observe the intermittent process of the resin reactor, which offers enhanced protection and mitigates the issues of accidental hardening.
The high full-scale range and high sensitivity at low viscosity offered by the MIVI online viscometer makes it the ideal tool for monitoring viscosity in phenolic resin processes. This sensor decreases solidification to zero and can simply be installed by insertion, on a bypass loop, or on a reactor wall due to the immersion tube.
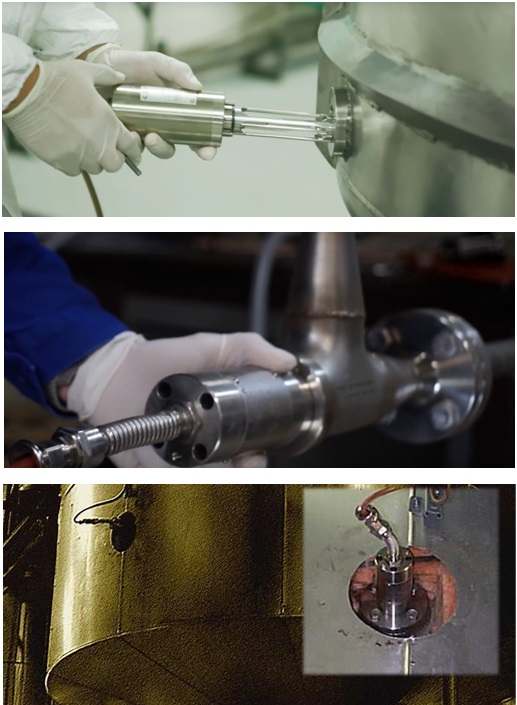
Key Product Characteristics
Sofraser has developed the first vibrating process viscometer which operates at resonance frequency. The needle’s vibration at its resonance frequency is testament to the high sensitivity of the measure, along with a broad operational range.
The use of proofed parts and the lack of moving parts throughout manufacturing justifies the decades of lifetime and the absence of drift.
Suited to the most challenging environments, the Sofraser MIVI viscometer provides the strongest performance on the market. It fits a range of installation configurations to enable the most effective measurement of fluids. MIVI is the only sensor that can offer the maximum level of sensitivity over a broad measurement range.
MIVI viscosity sensors are tailored to the needs of the end-user thanks to the range of choices available.
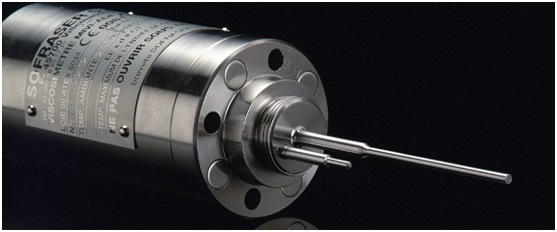
MIVI viscometers are applicable in a broad range of industrial applications, from very low viscosity, less than 1 mPa.s, to high viscosity, up to 1.000.000 mPa.s. This can be attained at temperatures up to 300 °C and pressures up to 1.400 bars.
The controller or electronics lets the operator observe, in real-time, the temperature and vicosity values and to ensure accurate and safe batch process operations.
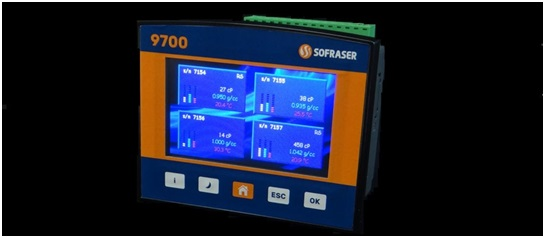
Enhance Safety and Process Performance
Thanks to the MIVI’s accurate viscosity measurement, the quality of the end-product along with process security and safety are enhanced, while solidification is prevented.
The MIVI sensor prevents rejected batches, removes the need for a new reactor and/or instrumentation, and reduces cleaning time. Post-installation savings in a phenolic resin batch polymerization factory normally delivers ROI in around one year.
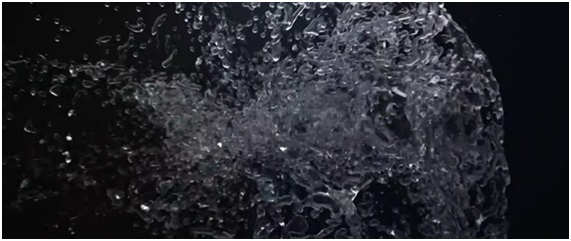
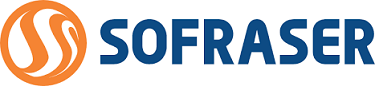
This information has been sourced, reviewed and adapted from materials provided by SOFRASER.
For more information on this source, please visit SOFRASER.