Many optical systems include mirrors as a component. They are used to direct and focus light, combine wavelengths, and reject specific wavelengths in imaging and a host of other applications. Multiple factors should be evaluated when choosing a mirror.
Materials
Metallic Mirrors offer a combination of reflectance and absorbance (along with transmittance if they are sufficiently thin).
They can be used as wide wavelength-range reflectors, neutral beamsplitters, or neutral density filters. The type of metal used determines its spectral characteristics. These mirrors are commonly applied outside of angle-of-incidence.
Dielectric Mirrors consist of intricate layers of materials that are non-absorbing (usually oxides and fluorides), which differ in their refractive index.
The thickness and composition of the layers are arranged to produce transmittance or reflectance in wavelength ranges required by the customer or application.
Little to no light is absorbed by these materials which means dielectric mirrors are often used as dichroic mirrors (where light of a specific color can pass through while different colored lights are reflected). Both the wavelength range and the angle-of-incidence should be calculated at the design stage.
Function
Imaging - Requires a flatness of λ/10 or more to decrease distortion of the image. Non-imaging, beam-steering applications do not require stringent flatness specifications.
Wavelength combining - Dielectric dichroic mirrors are used to combine various laser beams onto a single axis. A flatness of 1/4λ per inch or greater is required by this application.
Wavelength splitting - Target wavelengths can additionally be reflected by using dielectric dichroic mirrors. Applications include hot-mirrors that reject NIR and IR light, reflect excitation light, and transmit emission light while determining other wavelength bands with multiple detectors.
The transmitting and reflecting wavelengths must be well defined for this type of application. These are frequently used at a 45° angle of incidence.
Wavelength rejection – The exclusion of specific wavelengths from the system may be desired by researchers in some cases.
Some examples are hot mirrors (which reflect NIR or IR), cold mirrors (where shorter wavelengths are reflected while longer wavelengths are transmitted, commonly used in lamp assemblies) and order-sorting filters (where undesired wavelengths are reflected).
From an operational perspective, these are dichroic mirrors which are used for a different purpose. They are commonly employed at near-normal to normal incidence.
Angle of Incidence
The majority of mirrors are constructed to be used at a specific angle of incidence. Hot mirrors are usually employed at zero or near zero degrees AOI, whereas dichroic mirrors are often utilized at 45°.
The system’s optical design determines the AOI. Variations in polarization should be evaluated if the AOI is greater than approximately 25°.
Physical Environment
Durability requirements should be determined in the context of the physical surroundings in which the mirror will be used.
Temperature cycling is essential for space applications. For outdoor applications, humidity and temperature cycling, salt fog, abrasion resistance, and condensation may be factors to consider.
Radiative flux is where the filter is placed into a highly intense or energetic beam. This may result in its performance decreasing over time. In a protected laboratory instrument or air-conditioned laboratory spaces, the environmental requirements are smaller.
Wavelength Range
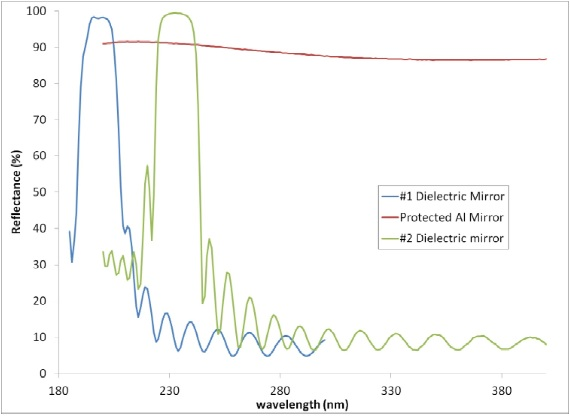
UV (180-400 nm) While traditional metal mirrors function throughout a broad range of wavelengths, different metals may have a superior performance over specific wavelength ranges. First-surface aluminum mirrors shielded with Magnesium Fluoride are usually recommended below 430 nm.
Omega has also created dielectric mirrors specific to this range that consist of intricate layers of transition metal oxides or lanthanide fluorides, silicon dioxide, and magnesium fluorides for the lower wavelengths.
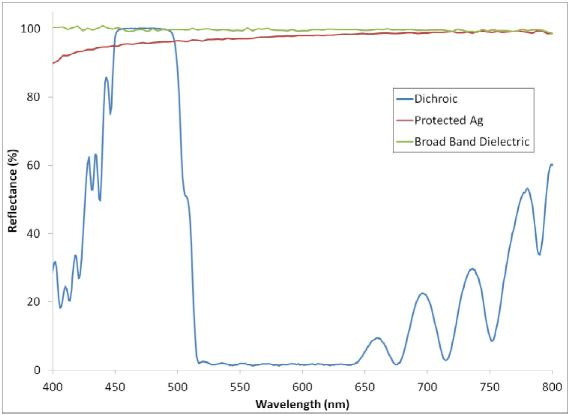
Visible (400-700 nm) Visible mirrors are conventionally created from silver on the top side (the first surface) or the backside of a piece of glass. They are often protected with a plastic material that is not transmissive (for the back surface) or an additional layer of silicon dioxide (for the first-surface).
Dielectric mirrors consist of non-absorbing materials in alternating layers and are created to increase reflectance at specific angles and wavelengths while rejecting others. Enhanced metal mirrors utilize both metal and dielectric layers to maximize reflectivity.
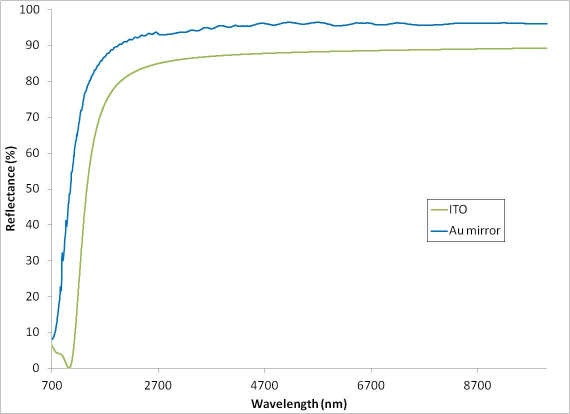
NIR – IR (700 nm - 10 micron) In the NIR and IR, gold mirrors are frequently used. They absorb light in particular visible wavelengths but also offer a high reflectance (more than 95% above 1,500 nm).
A transparent conductive oxide mirror (for example ITO) is an alternative choice which provides high reflectivity at longer wavelengths and transparency at shorter (visible) wavelengths.
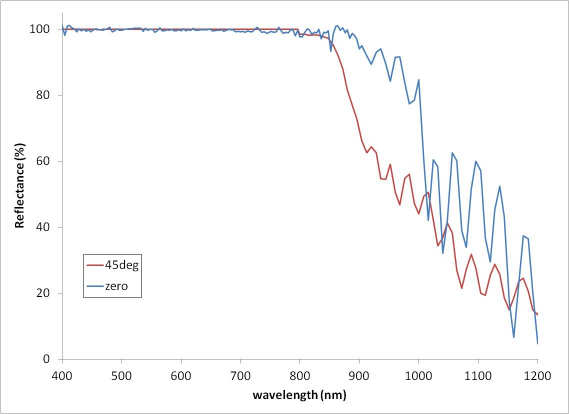
Broadband - High reflectivity across a wavelength range that covers most of those mentioned earlier may sometimes be required by an application. These applications include hyperspectral imaging, astronomy, and solar photothermal or photovoltaics.
For the highest and flattest reflectivity response, dielectric mirrors can be created (the same as the Ultra Broadband Dielectric Mirror).
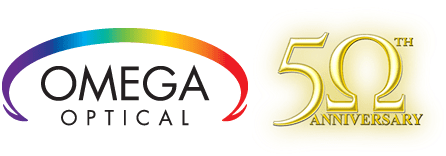
This information has been sourced, reviewed and adapted from materials provided by Omega Optical, Inc.
For more information on this source, please visit Omega Optical, Inc.