Almost 9,000 satellites were launched from more than 40 countries since the Soviet Union launched Sputnik – the very first satellite - on October 4th, 1957. While satellites were originally used for military reconnaissance missions, they are now extremely common, undertaking essential roles in everyday life across the world.
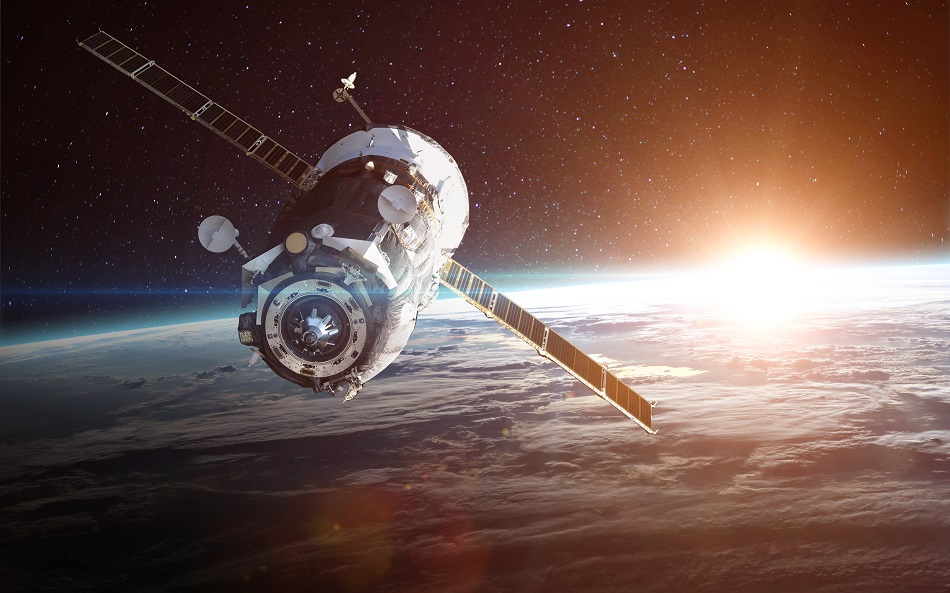
Image Credit: Vadim Sadovski/Shutterstock.com
Satellites are employed in a range of applications, from live broadcasts of sporting events and weather forecasting to uses in archaeology, allowing researchers to view otherwise hidden, ancient settlements that may have been buried for thousands of years.
More and more satellites are launched each year, with an average of 990 satellites expected to be launched annually between 2018 and 2028. This means that around 9,900 satellites will be launched by 2028, increased from 2,300 during the last decade – an increase of 400% - according to Euroconsult in its 2019 edition of ‘Satellites to be Built & Launched’.
Relatively new companies such as OneWeb, SpaceX, Telesat, and Amazon’s Project Kuiper anticipate launching almost 46,000 satellites over the next few years. These companies, as well as traditional manufacturers, are continuing to innovate and develop, meaning that the satellite industry and its designs have also been changing.
Omniseal Solutions is a highly regarded supplier of sealing and polymer solutions within the space industry. It has also adapted its material solutions, matching levels of innovation to meet the industry’s ever-evolving needs.
A growing trend in the satellite industry has been the move toward smaller satellites and lower orbits. In 2018, for example, low earth orbit satellites (LEOs) represented around 51% of worldwide launches, with an increase to over 54% estimated for the following year.
These smaller, lower orbiting and lighter-weight satellites have the potential to provide business services coupled with dependable, high-speed internet access and connectivity in remote locations where the use of fiber-optic cable may not be a viable option. Global communications have become more robust thanks to this developing technology.
Private launch vehicle services have enabled a major decrease in the cost of launching a satellite over the last decade – a reduction from $80,000 USD per kilogram at Space Shuttle time to around $1,000 USD per kilogram currently.
This reduction in cost, coupled with technology that permits the simultaneous launching of multiple payloads, has made the current concept of small satellites and constellations both commercially and technically feasible.
The need for increased numbers of satellites has opened the market to a variety of newcomers – very often agile start-ups that are competing with more established satellite manufacturers - encouraging innovation in an otherwise cautious commercial landscape.
Saint-Gobain Seals' Polymer & Metal Solutions: Connecting Us Every Day With Space Satellites
The Trajectory of Advanced Polymer Solutions in Satellite Systems
Two trends have emerged from this new landscape which have inspired a move to advanced polymers.
Compact satellites need smaller, lighter parts: This requirement for size and weight savings in LEOs has fundamentally altered approaches to materials and design. Additionally, more compact, smaller, lighter-weight LEO satellites are generally more flexible in design, meaning that polymers are often a good fit for parts.
Both traditional developers and newcomers to the industry are looking to innovate. This innovation often includes exploring ways of tightly linking satellite software and hardware, allowing better gathering and transmission of information from space to earth.
This exploration naturally leads to the use of advanced materials in systems, in order to gain a vital competitive edge. It also includes investigating material solutions that are longer-wearing, lighter-weight, and/or chemically compatible.
Advanced polymers provide a high mechanical strength coupled with a low weight. In many cases, these may be a viable alternative to metals. The explicit benefits of using advanced polymers in LEO or other satellite designs include:
- An existing pedigree for satellite applications and the general space industry
- Chemical compatibility with the hypergolic fluids most commonly used in satellite propulsion systems and thrusters
- Low outgassing and resistance to radiation
- Long lifetime of ten to fifteen years essential for GEO satellites
- Thermal and electric insulation capabilities
- Capability to withstand vacuum
Communicating the Many Uses for Polymer Seals and Components in Satellite Systems
Advanced polymers are specifically being used in the following five emerging satellite applications.
Chemical Propulsion Systems
Omniseal® spring-energized seals are commonly used on various types of tanks and valves. It is possible to manufacture Omniseal® polymer seals from a range of PTFE and PTFE-blended sealing materials. These are well known for enduring demanding conditions or hostile environments where elastomer seals are not suitable.
Solar Array Panel Deployment Systems
Rulon® blended PTFE-filled materials provide a low coefficient of friction on microsatellite solar panel arrays as these fold in launch then expand in orbit.
Flight-proven Rulon® J material is ideally suited for this application because it possesses one of the lowest coefficients of friction amongst commercially available blended PTFE materials. It also offers low outgassing, low weight and the possibility of being machined to a tight precision.
Electro-Optic Devices
Omniseal® spring-energized seals are well suited for reconnaissance, surveillance, and earth observation missions. These seals safeguard electronics in plexiglass camera systems, protecting them from potentially harsh outside environments. Over 30% of launched satellites include this functionality.
Omniseal® seals - that have proven applications on helicopters, drones and other aircraft - help to ensure that the system is operating correctly over its lifetime.
Structural and TRIBO Components
Meldin® thermoplastics, Meldin® 7000, and Rulon® high-performance polyimides, and Saint-Gobain HyComp advanced composites are able to replace aluminum, ceramics and other metals as a more lightweight option for the connection of moving components.
A selection of these materials from Omniseal Solutions can be utilized to integrate structural connectors, with tribological function (for example bushings and bearings), depending on specific application requirements.
As well as their potential for weight reduction, Meldin®, Rulon®, and HyComp advanced composite materials possess good mechanical properties, self-lubrication, low friction, and low outgassing.
Electric Propulsion Systems and Hall Effect Thrusters
A large number of companies are transitioning to xenon gas and electrical propulsion as satellites continue to become smaller. Omniseal® spring-energized seals are ideal replacements for elastomers, offering a tighter seal.
While advanced polymers may offer many advantages, metal seals, like those provided by Omniseal Solutions ASE and HTMS, can provide a superior alternative in some cases, when addressing the most rigorous leakage requirements.
In cases where weight and size are less of an issue, and the protection of core electronic systems such as system or altitude sensors is a priority, metal seals may offer a better solution because of their ability to meet strict leakage requirements.
Similarly, tight requirements may also be present in calibration instruments, such as those found in weather satellites. A number of other examples exist in which metal seals may be employed. These include:
- Primary and secondary power supply systems
- Laser systems
- Attitude heading reference systems (gyroscopes)
- Radar-electronics
- Altitude, speed and acceleration measurement systems
- Night-vision devices
Omniseal Solutions has acquired companies with metal sealing technology and expertise, meaning that they can provide both metal and polymer sealing solutions. This has expanded the company’s product portfolio while broadening their customer base within the space industry.
Omniseal Solutions has been working in the space industry for more than 60 years, supporting customers with missions to the moon, Mars and beyond.
Within Earth’s atmosphere, Omniseal Solutions is closely working with major satellite manufacturers as well as space companies seeking to advance them, and the rocket builders that launch them in order to innovate satellite design and performance, advancing communications and lives worldwide.
Acknowledgments
Produced from materials originally authored by Chiara Repetto from Omniseal Solutions.

This information has been sourced, reviewed and adapted from materials provided by Omniseal Solutions.
For more information on this source, please visit Omniseal Solutions.