Wilhelm Sanders, Product Business Development Manager OES at Hitachi High-Tech explains below which metals analysis method is best at different points during the EAF steelmaking process.
There are more than 3,500 different types of steel and each individual type has to conform to a certain material specification to ensure the finished product performs as it should.
Someone who operates a steel mill will know that getting that specification correct involves analysis at numerous stages of the process, from raw material to final product check – with a number of measurements taken during each cycle to make sure that impurities are sufficiently removed.
There are a number of different analysis technologies to choose from as a steel maker. The choice is dependent on how low the detection limits need to be, the materials you need to test for, and the practicality of taking measurements in a busy production environment.
The EAF process from raw material analysis to final QC is outlined below together with which analyzer type is best at each stage and the reasons why.
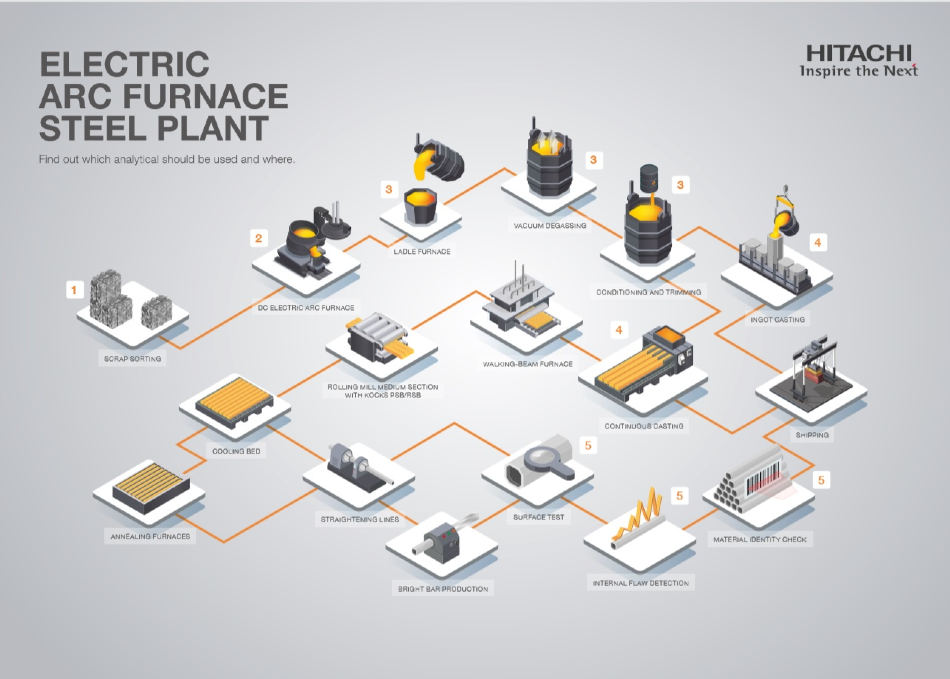
Quick Overview of Analysis Technology
The types of analysis technology which are mentioned in this article are LIBS, XRF, and OES. Below is a simple overview of each one:
Laser-Induced Breakdown Spectroscopy (LIBS)
A small amount of material on the metal surface is heated with a laser which turns part of the solid metal surface into a very small amount of plasma. It emits radiation of a very specific wavelength as the plasma cools. Analysis of these wavelengths indicates which elements are present in the sample.
X-ray Fluorescence (XRF)
A focused beam of X-rays is fired at the surface of the metal. The high energy beam displaces electrons in the atoms and these electrons release a very specific energy signature as they fall back into their natural state, which the instrument can detect.
Optical Emission Spectroscopy (OES)
In principle, this is similar to LIBS, but here the metal surface is heated with electrical spark discharges to thousands of ºC. The energy applied causes the atoms in the material to emit characteristic light, which is analyzed to establish which elements are present in the sample.
Stage 1: Scrap Sorting
The first analysis step is performed in the scrapyard, not the steel mill. The type of scrap for each melt has to be selected carefully to avoid unwanted impurities entering the melt as much as possible as it is the main feedstock for steel.
This means that to meet the melt specification, the scrapyard will choose the right type of scrap. Using analysis, the scrap must be sorted into specific scrap classification classes based on the requirements for the steel grades to be created.
In order to avoid unwanted tramp elements ending up in the melt, it is crucial that impurities are identified at this stage. For instance, scrap with low phosphorus levels must be chosen if low-phosphorus steel is to be produced.
When it comes to scrap analysis, the most vital aspects are speed and portability; the analyzer should be taken to the scrap, not the other way round. Fortunately, today’s mobile and portable analyzers have short analyzing times, are very accurate, and are well within the detection limits for scrap sorting. The choices are outlined below:
Hand-held LIBS (laser-induced breakdown spectroscopy) analyzers are perfect for quick alloy identification. These analyzers, for example, the Vulcan from Hitachi, are truly portable, lightweight, and can identify an alloy grade in seconds. They are ideal for sorting large amounts of scrap.
Yet, if the purpose is to measure low levels of sulfur or phosphorus in steel, then there is a choice of two other technologies, XRF (X-ray fluorescence) or OES (optical emission spectroscopy) which is also known as spark spectrometry. For example, the portable PMI-Master Smart that uses OES, or the X-MET8000 handheld analyzer that utilizes XRF technology.
If you are choosing scrap based on carbon, boron, nitrogen, or other elements that have to be monitored at very low levels such as lead, copper, and tin, then OES technology supplies the most accurate reading.
Stage 2: EAF Melt Composition and Slag Analysis
Next, the melting and refining process in the electric arc furnace itself will be discussed. Bath chemistry analysis is performed after the final scrap charge is fully melted and furnace conditions have stabilized.
The results from this test will establish how much oxygen must pass through during refining. Before passing to the next phase, measurements are also taken at the end of refining.
In this instance, metals analysis is mainly concerned with detecting phosphorus, silicon, sulfur, aluminum, carbon, and manganese as solid impurities, and nitrogen and hydrogen as dissolved gasses.
Multiple measurements may be required during the furnace processing until you have removed impurities, like phosphorus, to the desired level. For rapid analysis and feedback on processes, a dedicated analyzer for EAF melt chemistry analysis is crucial.
OES technology is the ideal choice for EAF melt chemistry due to the low detection limits and element types, as it is the only method capable of measuring most of these elements at the necessary limits.
Unlike the scrapyard example, here it is not crucial that the analyzer be mobile or portable. Stationary OES is perfectly sufficient as a small sample is taken from the melt and taken to the analyzer.
It must be ensured that the chosen OES instrument is able to measure all critical elements in metal to the lowest detection limits possible, depending on your specific melt chemistry.
From low-end instruments to large lab-based spectrometers, there is a wide range of models on the market. Selecting the right one will depend on a user’s requirements and budget. The starting point should be assessing the detection capability of the instrument.
There are two key reasons that slag analysis is important at this stage. Firstly, the slag must be monitored through routine analysis because the basitivity of the slag can adversely influence the refractory lining of the EAF walls.
Secondly, to promote the production of what’s known as ‘foam-slag’. This is where the slag is foamed to enlarge its volume by forming gaseous carbon oxides. This prevents the burning of the steel bath and helps to shield the arc.
This process increases thermal efficiency when it is performed effectively and makes reaching the high temperatures required for melting much easier. EAF slag is usually made up of oxidic components like SiO2, CaO, and Al2O3.
Stage 3: Secondary Processing in Ladle Furnaces
Specific processing in the ladle furnace and the analysis that is needed is dependent on a steelworks’ processing setup. Often, the analysis in secondary processing in ladle furnaces happens after de-slagging, alloying, and vacuum degassing.
The utilization of vacuum technology and purging the material with inert gases is one step which is effective to acquire maximum cleanliness of steel. This technology serves to adjust the carbon content, desulfurization, deoxidation, dephosphorylation and degassing of the liquid steels.
At this stage, slag process control is to remove impurities that have not been removed in the EAF. Slag can be analyzed with XRF instruments and energy dispersive or wavelength dispersive instruments are available.
For instance, the X-Supreme benchtop analyzer in the Hitachi range of energy-dispersive XRF equipment is perfect for slag analysis. This instrument has been optimized for fast analysis of steel slag and has numerous other features that are important for the steel industry.
In a busy production environment high reliability, minimal dust ingress, and ease of use are crucial. Other features, like multi-sample analysis, help to make the analyzer efficient when in use 24/7.
XRF technology is essential for the accuracy needed. It is a powerful X-ray source, a high-sensitivity silicon drift detector (SDD), and can take measurements in helium to decrease the effects of interference from the atmosphere. The XRF equipment manufacturer will be able to confirm if the analyzer is suitable for the analysis of slag compositions for a specific application.
OES is by far the best method for alloy analysis, the exact alloy composition will need to be detected and there are a range of elements involved and the low levels contained. As in EAF melt chemistry analysis, stationary OES is satisfactory and has been well established over decades as the “workhorse” for routine elemental process analysis.
Vacuum degassing is the final process in the ladle furnace that involves analysis. Hydrogen is one of the main elements here. Hydrogen must be controlled to ultra-low levels in certain types of steel and this is where a user will require the capability to measure hydrogen to very low levels.
Gases such as hydrogen, oxygen, and nitrogen are usually analyzed with combustion analyzers but modern OES analyzers can analyze nitrogen at low levels. Yet, even among OES analyzers, there is a variation in performance, and this is particularly true when testing for gases.
For instance, there is a stationary OES analyzer (OE750) that is able to analyze nitrogen at low detection limits. It is worth checking with your own instrument’s manufacturer to see what the detection limits are.
Stage 4: Continuous Casting or Ingot Casting
For continuous casting processes, the composition must be monitored during mixing a new grade or batch. Again, stationary OES analysis is an essential technique. Due to the final applications, today’s specifications for wires, plates, and rods are complex.
Steel wire which is to be used for aerospace or high-performance tires has very specific requirements and OES is the only technology that is able to analyze the entire spectrum of elements involved down to the limits required.
OES is also the technique that should be selected for process control during ingot casting, and the final steel sample is taken during the casting process for analysis.
Stage 5: Final Specification Check Before Shipping
Most robust QC programs will need a final compositional verification check, whether measuring wires, plates, rods, or other products from a continuous casting process or individual components from ingot casting.
The aim of this is to create a final component composition certificate and to avoid the risk of a material mix-up when preparing shipments. Solid, finished components are now being dealt with and, as with the scrap yard situation, it is not convenient to take parts to the analyzer for verification. So there are two choices: in-line automation or mobile analysis.
Automation
Many quality control programs need 100 % material testing before shipping, which is where automation can help streamline your testing process and ensure you maintain a steady throughput in your production and total avoidance of material mix-up.
In order to provide continuous feedback on final product specifications, many OES instruments can be integrated into a production line. Products such as Hitachi’s own TEST-MASTER Pro OES analyzer are designed specifically for high volume testing on conditioning lines.
Mobile Analysis
There is a choice of hand-held XRF analyzers depending on the actual composition of your components, like Hitachi’s X-MET8000, or mobile OES, like the PMI MASTER range, or the TEST-MASTER Pro which is specially designed for continuous operation and 100 % testing.
The XRF hand-held is more portable than the mobile OES and will be ideal for most material verification purposes. Yet, OES is the best technology to use if you need to verify low alloy steels or light elements like boron, carbon, or other low-level elements that hand-held XRF cannot detect.
Conclusion
The most obvious takeaway from this is the requirement to use more than one analyzer and maybe even more than one method over the production process. The OES equipment employed to establish melt chemistry should not be tied up with final QC analysis, where a hand-held XRF instrument could do the job more easily.
Balancing instrument costs with productivity and accuracy to make sure you are producing a high-quality product is crucial, but the analysis shouldn’t cause a bottleneck in your process.
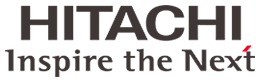
This information has been sourced, reviewed and adapted from materials provided by Hitachi High-Tech Analytical Science.
For more information on this source, please visit Hitachi High-Tech Analytical Science.