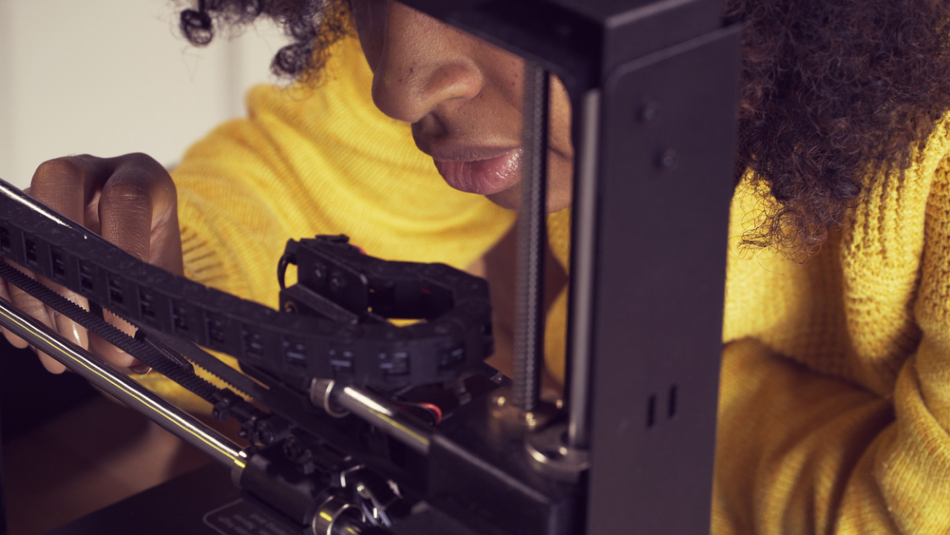
Image Credit: Made360/Shutterstock.com
Composites of continuous carbon fibers and thermoset polymers can now be made using a new 3D printing technology. Such composites are strong and lightweight and may find applications in many industries from aerospace to automobiles.
3D printing is fast developing as a quick and simple method for making a variety of different components. Various materials, such as polymers, metals, and biological materials have been used for 3D printing. The process, also known as additive manufacturing, involves building complex 3D shapes by depositing material layer by layer and then fusing all the layers.
Polymer composites, which comprise polymers mixed with other filler materials, have properties that are generally far better than the single polymer itself. Adding fillers, such as metal particles, inorganic particles, and fibers, improves mechanical properties while still keeping the weight of the composite low.
3D printing has been used to make parts from polymer composites. However, only thermoplastic polymers, polymers that soften upon heating, have been used successfully until now, along with disjointed fillers.
Thermoset polymers do not soften once they are cured. Common methods for making parts from thermoset polymer composites are laying polymer tape and placing or winding fibers in the shape of the part. The entire composite structure is then cured. This process requires molds for each part and many process steps until the cured part is ready.
Although 3D-printed thermoplastic polymer composites have been demonstrated, they do not have good mechanical properties, as the fillers in them are not continuous. Therefore, it is expected that if continuous fillers were used in 3D printing, in addition to enabling the use of thermoset polymers, the properties of the polymer composite would be excellent.
LITA 3D Printing Process
A team of researchers from the University of Delaware has developed a 3D printing method that allows the use of thermoset polymers and continuous carbon fibers for preparing polymer composites. They call the technique localized in-plane thermal assisted (LITA) 3D printing.
The technique uses the wicking or capillary action of liquid polymers to fill the spaces between carbon fibers. The carbon fibers are laid down so that there is a gap between neighboring fibers, which allows the liquid polymer to wick into the fiber structure and surround the fibers. If the fibers are also porous, the polymer can infuse into the fibers.
A heater moves over the carbon fibers and creates a temperature gradient that allows the polymer to cure once it has flown into the space between the carbon fibers, forming a 3D structure. Heating also decreases the viscosity of the polymer, changing its physical properties, and helps the polymer flow easily. Heating also helps the polymer to completely wet the fibers without forming voids.
Read more: 3D Printers and 3D Printing Equipment, Materials and Accessories
Since the polymer does not need any further curing after the LITA 3D printing, and the part is ready as soon as the 3D printing is done, this could save significant energy used for curing the thermoset polymers in typical processes.
The researchers designed a robotic system to perform the LITA 3D printing. The robotic system has a printing head and an automated robotic arm. The printing head features a nozzle for dispensing the resin, a dispenser for the carbon fibers, and a Joule heater. The fiber is fed continuously via a spool of carbon fibers. The robotic arm controls the movements of the printing head.
Potential Applications of LITA 3D Printing
Polymer composites made from continuous carbon fibers and thermoset polymers are important to develop strong lightweight components in industrial applications such as bridges and airplanes.
Using the robotic system, the researchers printed components on substrates or in free space. According to the authors, LITA 3D-printed parts using industrial-grade carbon fibers and liquid epoxy had the best tensile strength among 3D printed polymer composites reported so far.
The authors demonstrated different types of parts, such as shapes on a 2D substrate, a 3D star, and conformal printing on a cylindrical rod.
The LITA 3D printing process can be easily integrated into current composite manufacturing processes and can be used with many thermally cured polymers. In addition, carbon fibers and other heat-conducting fibers can be used.
Since the process does not use an additional curing step, which could take several hours, there are tremendous energy savings. The LITA 3D printing process is also much faster than current processes. Another advantage of the process is its reliability and repeatability in making complex shapes.
The authors also say that the LITA 3D printing process could reduce labor and tooling costs, while it could also produce shapes with very little defects.
The LITA 3D printing process is much cheaper than current processes for making thermoset polymers composites because of the significant energy savings and the elimination of many conventional steps. Therefore, the technology has great potential to be used in polymer composite manufacture, leading to the fabrication of complex shapes simply and cheaply.
References and Further Reading
Shi, B. et al. (2020) Dynamic Capillary-Driven Additive Manufacturing of Continuous Carbon Fiber Composite. Matter. https://doi.org/10.1016/j.matt.2020.04.010
New Technology to 3D Print Flexible Fiber-reinforced Polymer Composites [online] Available at: https://omnexus.specialchem.com/news/industry-news/3d-print-polymer-composite-000222302?lr=iom20081958 (Accessed on 14 August 2020).
Disclaimer: The views expressed here are those of the author expressed in their private capacity and do not necessarily represent the views of AZoM.com Limited T/A AZoNetwork the owner and operator of this website. This disclaimer forms part of the Terms and conditions of use of this website.