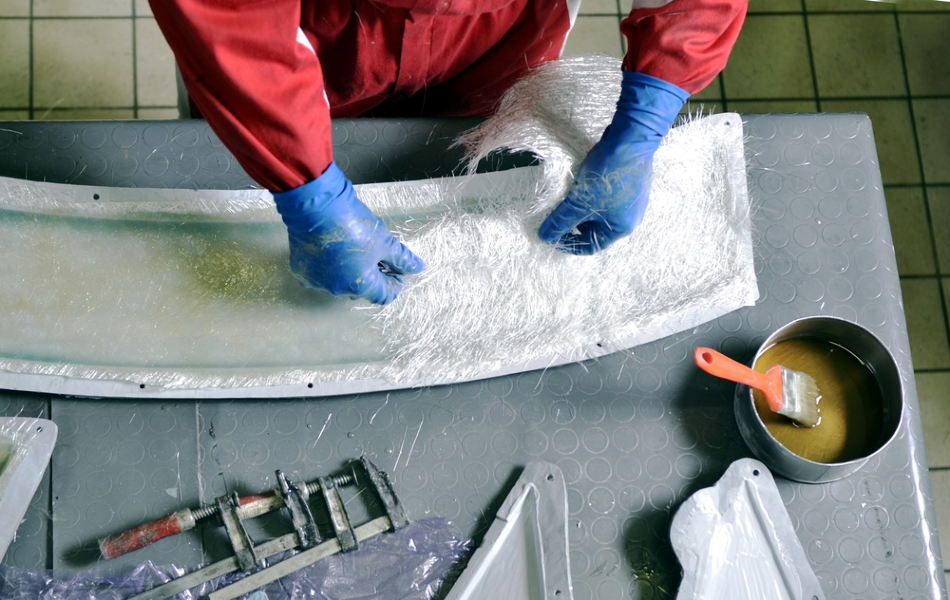
Image Credit: faboi/Shutterstock.com
The automotive industry is the third-largest consumer of polymer materials after the packaging and construction industries. By using engineered plastics with recycled content, automotive companies around the world are becoming less dependent on the consumption of finite resources.
In response to that demand, LANXESS, a leading global supplier of specialty chemicals and polymer materials based in Cologne, Germany, working in close collaboration with leaders in the automotive industry, has developed a range of recycled glass-fiber polyamides suitable for manufacturing of automotive components.
New Technological Developments for More Efficient Manufacturing
With the growing concerns about climate change, environmental degradation, and rising prices of raw materials, sustainability has become a strategic priority for automotive companies. Through engineering and innovation, the companies in the sector continue to develop new technologies to combat these problems.
Additive manufacturing technology enables more material-efficient component designs along with the utilization of advanced 3D printing materials that are highly-reusable and lower the environmental impact of the final product.
However, in mass production, additive manufacturing is currently much less implemented compared to injection molding, which is the most commonly used manufacturing process for automotive plastic components. The significant initial investment of energy and resources associated with the mold design and fabrication process, combined with the plastic waste in the form of gates and flash (excess material filling technological cavities and openings in the mold) which must be removed from the finished parts and recycled, present a significant obstacle for a sustainable injection molding manufacturing.
Injection Molded Plastic Components with Reduced Environmental Impact
As one of the major suppliers of composite materials to the global automotive industry, LANXESS is very well-positioned to offer solutions that can alleviate high environmental costs and carbon footprints.
Calling on the long-established technological know-how of LANXESS' High Performance Materials business unit, the company has extended its Durethan® range of polyamide-based reinforced composites to include reinforced recycled glass fiber products.
Polyamides are one of the most versatile engineering thermoplastics widely used in the automotive industry, consumer goods manufacturing, and in a range of electrical and electronics applications. Polyamide materials offer excellent high temperature and electrical resistance, while their partially crystalline structure makes them resistant to chemicals.
The Durethan® range of glass-reinforced polyamides is so resilient that the material can be used as a replacement of the traditional metal alloys. These properties allow the reinforced polyamides to be used in components that might sustain significant impacts and have to ensure a safe impact energy dissipation, such as radiators, headlight housings, and other structural components for the front-end assembly of a car.
What sample preparation or laboratory testing equipment is available on the market today?
Sustainable Polyamides for the Automotive Industry
The new Durethan® range of recycled glass-fiber polyamides includes three products, designated ECOBKV30H2.0, ECOBKV35H2.0 and ECOBKV60XF, that incorporate 30 wt%, 35 wt% or 60 wt%, respectively, of reinforcing glass fibers sourced from post-industrial recycling (leftovers from glass fiber manufacturing). These products are based on the polyamide 6 resin (also known as Nylon 6 or polycaprolactam), one of the most extensively used polyamides for the automotive industry, that is synthesized by ring-opening polymerization of caprolactam (a cyclic organic compound containing carboxyl and amine groups).
According to Dr. Guenter Margraf, a global product manager at LANXESS' High Performance Materials, the new highly-reinforced and easy-flowing compounds retain their strength, stiffness, and processability, allowing the Durethan® recycled glass-fiber polyamides to be processed using the existing facilities and injection molding equipment as their non-recycled counterparts.
This means that manufacturers do not have to sacrifice any of the components' characteristics while enjoying a more sustainable and cost-effective manufacturing process.
Recycled Glass-Fiber Polyamides Contribute to the Circular Economy
To offer polyamide composites with recycled content that have characteristics identical to those of virgin quality materials, LANXESS employs the mass balance approach, where the recycled raw materials are incorporated into the production cycle together with the virgin feedstocks, commonly used otherwise, and then arithmetically allocated to the finished product.
This approach resulted from an initiative launched by the non-profit Ellen MacArthur Foundation and is employed by manufacturers around the world for recycling of post-industrial and post-consumer waste.
The use of recycled glass fiber waste was carefully examined by the independent inspection company Ecocycle. The new range of recycled glass-fiber polyamides was awarded an Ecoloop certificate following ISO 14021:2016, ensuring that the Durethan® ECO range makes a contribution to the circular economy through the use of waste-based raw materials.
Commitment to Global Climate Security
In line with the company's ambitious goal of becoming climate neutral and to eliminate its greenhouse gas emissions by 2040, LANXESS is planning to broaden its range of ECO products certified following the mass balance method.
The plans include the launch of a new polyamide 6 with a recycled glass fiber content of 30 wt% and a reduced carbon footprint. At the same time, the company is planning to start using waste glass fibers from end-of-life components (or post-consumer recycling), that are regarded as particularly sustainable raw material for use in the manufacturing of recycled reinforced polyamide composites.
References and Further Reading
LANXESS (2020) New Durethan ECO polyamide product range featuring fibers from waste glass. [Online] www.lanxess.com Available at: https://lanxess.com/en/Media/Press-Releases/2020/06/New-Durethan-ECO-polyamide-product-range-featuring-fibers-from-waste-glass (Accessed on 19 August 2020).
Materials Today (2020) Materials incorporate recycled glass fibers. [Online] www.materialstoday.com Available at: https://www.materialstoday.com/ (Accessed on 19 August 2020).
S. Moore (2020) Recycled Glass Fibers Boost Sustainability of Polyamide Compounds. [Online] www.plasticstoday.com Available at: https://www.plasticstoday.com/sustainability/recycled-glass-fibers-boost-sustainability-polyamide-compounds (Accessed on 19 August 2020).
Packaging Europe (2020) LANXESS announces new polyamide range featuring fibre from waste glass. [Online] https://packagingeurope.com/ Available at: https://packagingeurope.com/lanxess-announces-waste-glass-polyamide-range/ (Accessed on 19 August 2020).
LANXESS (2019) LANXESS to become climate neutral by 2040. [Online] www.lanxess.com Available at: https://lanxess.com/en/media/press-releases/2019/11/lanxess-to-become-climate-neutral-by-2040 (Accessed on 19 August 2020).
Disclaimer: The views expressed here are those of the author expressed in their private capacity and do not necessarily represent the views of AZoM.com Limited T/A AZoNetwork the owner and operator of this website. This disclaimer forms part of the Terms and conditions of use of this website.