Refinery samples are combinations of a range of hydrocarbons (aromatic, polycyclic, aliphatic, and more) created from the process of fractionated distillation of crude oil.
Their viscosities, combustion behavior, and boiling intervals are similarly diverse. This makes it complex to verify repeatable analysis results for all types of matrices.
Analysis in horizontal mode with a boat inlet is the only suitable technique to mitigate matrix effects such as incomplete combustion or results that are too low. In contrast to vertical operation, a number of operators dislike horizontal mode as the analysis times are increased, and optimized combustion resp. boat programs must be created for each matrix quantity and type.
The measurement quality is frequently a compromise between desired sample throughput (speed of analysis), the dispersion of the measurement values, and the analysis time. Along with chlorine and sulfur, nitrogen is another crucial parameter that should be measured.
For quality and process control, TN contents over a wide range must be identified. While traces of TN are the focus during the refining process, which can result in undesirable byproducts and can poison catalysts, the analysis of feed materials and product control must cover a broader concentration range.
For matrices like vacuum residues, HC feeds, and crude oil, contents up to the wt% range are prevalent, but this is also the case for high-performance engine oils and lube. The multi EA 5100 is directly designed for the efficient and simple measurement of a wide range of TN contents in complex matrices in horizontal mode.
Combining effective gas purification and drying with the highly sensitive HiPerSens CLD and catalyst-free high-temperature combustion, the direct measurement of nitrogen is achieved at concentrations as high as 10,000 mg/L, all in the same device.
Materials and Methods
Samples and Reagents
Various refinery and related samples (gas oil, lube oil, heating oil, among others) have been investigated.
- Calibration standard kits Nitrogen (Analytik Jena, Art.-No.: 402-889.075, 402-889.162, 402-889.165).
- Isooctane (C8H18), Suprasolv®, GR for gas chromatography (Merck Art.-No.: 1.15440.1000).
- Pyridine (C5H5N), GR for analysis (Merck Art.-No.: 1.09728.0100).
Sample Preparation
If the sample viscosities were less than 10 cSt and the element contents were within the analyzer’s operation range then the samples were directly analyzed.
Samples that did not meet these requirements were diluted with either o-xylene or isooctane to change the element content to the operation range resp. to allow consistent sample supply using the MMS liquids sampler.
Calibration
The analysis system was calibrated in a broad concentration range by using liquid calibration standards based on pyridine (N) in isooctane.
As interfering components are removed before measurement and the combustion process is optimized, matrix-related calibration strategies were not required. The calibration was verified with a range of concentrated standards.
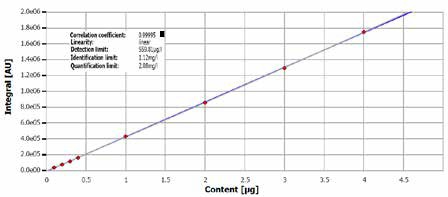
Figure 1. Exemplary calibration for TN upper range, curve including statistics.
Instrumentation
A multi EA 5100 was used to perform the measurements, featuring HiPerSens chemiluminescence detection for the determination of nitrogen.
Sample introduction was performed in complete automation by utilizing the MMS multi matrix sampler supplied with a liquids kit along with the ABD, an automatic boat drive with a cooled sample introduction zone. This provides optimum analysis results and high sample throughput, even for samples with complex composition or higher viscosity.
Horizontal operation mode was used to run the analyses. The samples were injected directly into a quartz sample boat, located inside of the ABD, using the liquids mode of the MMS.
The ABD automatically transfers the loaded boat into the combustion tube’s hot zone after sample injection. The bi-phasic, catalyst-free combustion procedure is performed at temperatures up to 1050 °C.
In the first phase of the process, pyrolysis of the heavier sample components and the evaporation of volatile components occurs in an inert gas stream. The formed gaseous products are then combusted in an oxygen-rich environment.
In the second stage, pure oxygen is used to quantitatively oxidize the heavier, non-volatile sample components along with the formed pyrolysis products. The flame sensor technology makes sure that every component of the sample matrix receives uniform evaporation and quantitative combustion.
This effectively prevents system contamination, incomplete combustion, and low-quality analysis results (scattering, or too low results). Ideal conditions are produced for the measurement of any type of matrix, even unknown ones, independent of the introduced quantity.
Horizontal operation is particularly recommended for high element contents, unknown samples, vigorously reacting samples, or dissimilar materials (polymers, residue, for example). It is also suited for any samples that are easy-to-handle and have lower element contents.
The featured Auto-Protection system provides optimal operational safety, such as an aerosol and particle trap, and a total transfer of the formed NOx into the CLD after the reaction gases have been sufficiently dried. The multi EA 5100 offers a lower detection limit as small as 10 µg/L N.
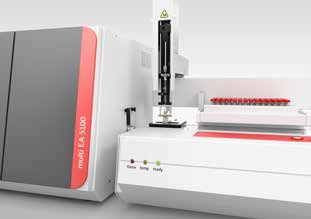
Figure 2. multi EA 5100 with ABD and MMS in horizontal operation mode.
Method Parameters
For all measurements, an approved method from the analyzer’s method library was utilized. It is suitable for the analysis of samples and liquids with boiling points above 400 °C or increased viscosity.
Optimal analysis results can be achieved in the quickest time without increasing maintenance effort through the use of horizontal mode with flame sensor control.
Adequate dilution with an appropriate solvent (such as xylene) can optimize syringeability to provide a higher processing speed for samples that are too viscous for the syringe inlet, or a wide-bore needle could be employed. The parameter settings for the combustion process are summarized in the following table.
Table 1. Process parameters multi EA 5100 in horizontal mode with flame sensor technology.
Parameter |
Specification |
Furnace temperature |
1050 °C |
Cooling time (boat) |
240 s |
Second combustion |
60 s |
Ar flow (first phase) |
200 mL/min |
O2 main flow |
200 mL/min |
O2 flow (second phase) |
200 mL/min |
Draw up |
2 µL/s |
Injection volume |
40 µL |
Injection |
3 µL/s |
Evaluation Parameters
Regular method settings were used. The following table summarizes the parameter settings.
Table 2. Detection parameters CLD.
Parameter |
Specification |
Max. integration time |
600 s |
Start |
1.9 ppb |
Stop |
2.0 ppb |
Stability |
7 |
Results and Discussion
The analyzed samples are final products and process intermediates from the petrochemical industry and refineries. Table 3 presents results that are averages of three replicate analyses of test standards and samples. An injection volume of 40 µL was utilized for all samples respective of the test standards and their dilutions.
Table 3. Results of the total nitrogen determination in different refinery samples and standards by means of double furnace technology.
Measurement |
TN |
SD |
Dilution |
Diesel oil |
57.0 mg/L |
±0.52 mg/L |
- |
Heating oil C |
257 mg/L |
±1.51 mg/L |
- |
HCC feed |
1.38 g/kg |
<0.01 mg/kg |
1 in 116 |
Coker oil |
1.40 g/kg |
<0.01 mg/kg |
1 in 122 |
Vacuum oil |
5.37 g/kg |
±0.05 mg/kg |
1 in 100 |
TN Standard (c = 5.00 mg/L) |
5.00 mg/L |
±0.10 mg/L |
- |
TN Standard (c = 1,000 mg/L) |
999 mg/L |
±0.92 mg/L |
- |
Typical measuring curves for a range of samples and standards are shown in Figures 3 to 6.
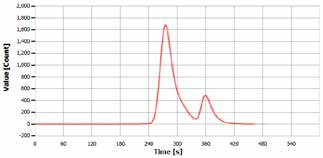
Figure 3. Analysis curve of “HCC feed” (dilution).
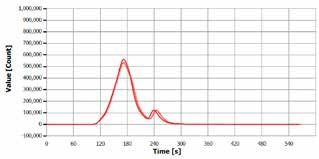
Figure 4. Analysis curve of “Diesel oil”.
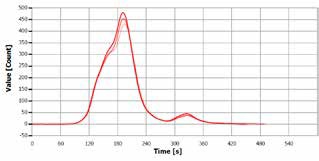
Figure 5. Analysis curve of “TN standard 5 mg/L.
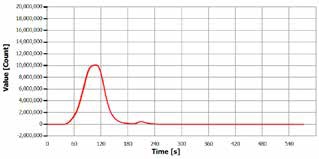
Figure 6. Analysis curve of “TN standard 1,000 mg/L”.
A threefold determination is enough to gain results much less than 3% RSD. This significantly influences the time taken to process the sample which enables a higher sample throughput. The results from the analysis and their reproducibility demonstrate the efficacy of the digestion process.
The analysis system’s total performance was verified by measuring standard materials with known nitrogen contents. These results are presented in Table 3.
If desired, additional time savings can be gained by decreasing the quantities of the sample for sample matrices with a higher concentration. The same detection and process parameters can be used.
Conclusion
The multi EA 5100 used in combination with the ABD offers an efficient and dependable solution for the accurate measurement of a broad range of nitrogen contents, even in samples that are challenging.
The flame sensor technology ensures that optimal results can be acquired for any matrix in the most efficient time, regardless of their combustion characteristics or nitrogen content. This allows daily routine work to be simplified and helps to drastically improve sample throughput while decreasing maintenance and operation demands.
Due to the HiPerSens technology, a measurement range of up to 10,000 mg/L starting at a detection limit as low as 30 µg/L of nitrogen can be easily attained.
The effective sample digestion and the fast Auto-Protection system, along with a high-capacity membrane drier, provide superior reproducibility, irrespective of the digestion characteristics and composition or the TN concentration of the sample matrix to be analyzed.
The MMS liquids sampler with 112 positions makes high sample throughput easy to achieve, which can also be used with vertical along with horizontal sample introduction methods. A possible alternative for applications that require lower throughput is the use of boat injection (ABD) to manually introduce the samples.
If required, the analysis system can be upgraded to analyze further types of matrix such as solids and gases, or for the determination of further parameters and elements (such as chlorine, sulfur, TOC, carbon, EOX, AOX) simply by adding a suitable detection or sampling system.
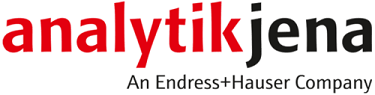
This information has been sourced, reviewed, and adapted from materials provided by Analytik Jena US.
For more information on this source, please visit Analytik Jena US.