For several testing applications, non-contact measuring extensometers provide significant benefits over traditional, contact-type extensometers. One of their main features is in the name itself, as there is no contact with the specimen and, because of the optical measurement, interaction between the specimen and the measuring instrument is non-existent.
In addition, one of the lesser-known advantages is that optical extensometers enable the entire specimen to be in view, and the cameras display images that yield more information than the strain alone. For example, they allow the break position to be determined automatically or for retroactive adjustment of the initial measuring length, which in turn reduces both the required specimen material and testing time.
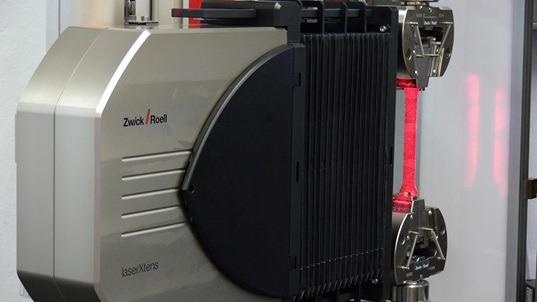
Image Credit: ZwickRoell GmbH Co. KG
Therefore, in many respects, optical extensometers surpass the capabilities of contact-type extensometers. Since there is no physical contact with the specimen, test knife edges and drag forces do not influence test sample behaviour. This eradicates the potentiality of distorted test results affected by the testing instrument itself.
Thus, as a result of decoupling, optical extensometers are better protected from being damaged by the test specimens and are therefore not adversely affected by brittle-fracturing specimens or specimens liable to whipping with high energy at break, such as elastomers, wires and ropes. Furthermore, if contact-type systems lack sufficient room between the test fixtures, small or short specimens can be accommodated by utilizing optical systems.
Measurements in temperature chambers can be carried out via an optically correct glass viewing pane and provide enhanced results in contrast to sensor arm extensometers due to the fact they can be captured in an enclosed system.
ZwickRoell offers various technologies relative to optical, non-contact extensometer solutions. The most renowned technology is the camera-based videoXtens, which encompass an extremely broad range of applications.
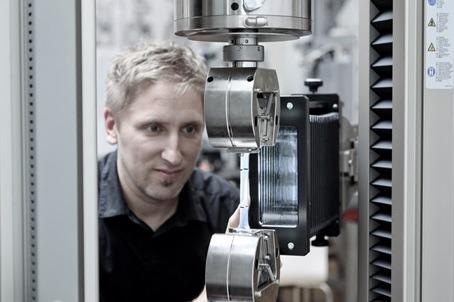
videoXtens instrument and test specimen with gauge length markers. Image Credit: ZwickRoell GmbH Co. KG
A camera with a lens is integrated into the extensometer and, conditional on the rise-height of the lens, there is a small or large field of view that corresponds to the area of the specimen from which the camera records. The required gauge length is achieved by applying gauge marks to the specimen. The testXpert III software then automatically identifies the gauge marks and transmits the initial gauge length into the system.
Throughout the test, the marks are displayed frame by frame as they are tracked. Intelligent algorithms and a novel marking method in the software generate superior measurement accuracy due to all measurement channels being precisely synchronized. The software for the optical extensometers is incorporated into testXpert III, which enables saving and evaluation of all of the test data in a single software. The videoXtens system can be configured according to the required application because of its modular design.
The measurement range needed for the test and the appropriate measurement values determine the specifications necessary for the field of view and the resolution of the lens. There is one correlation that applies here: a lens with a large field of view produces low resolution, and a lens with a small field of view produces high resolution.
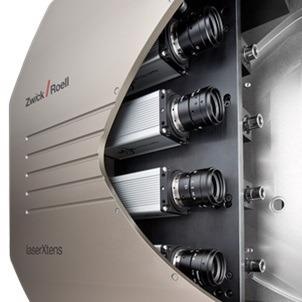
Multiple camera video array technology extensometer. Image Credit: ZwickRoell GmbH Co. KG
In order to generate high resolution over a broad measurement range, ZwickRoell designed its latest array technology by connecting multiple cameras with high resolution lenses in single series. The intersecting fields of view are then amalgamated to form a single large image via internal software, enabling the videoXtens to provide very high resolution images with a large measurement range.
For instance, there is the videoXtens product, which offers a resolution of 0.15 µm in a measurement range of up to 140 mm. It also satisfies the stringent calibration requirements of ISO 527-1 Annex C to ascertain the tensile modulus, even for tests at lowered or raised temperatures in ZwickRoell temperature chambers.
Since the entire specimen or a large portion of the specimen remains within an optical extensometer's field of view, there are several options for acquiring further information via a simple, pure software option upgrade with no intricate hardware upgrade necessary. For example, it is possible to accommodate simultaneous determination of transverse strain and biaxial measurements or multiple measuring points, up to 100, can be placed on the surface of the specimen.
The additional benefits become even more apparent during automatic determination of the break point, through which the initial gauge length can be determined automatically to the break point. Thus, by utilizing testXpert III software and the option of strain distribution, up to 16 equally distributed measuring points are fixed on the specimen. Throughout the test, the single strains between measuring points are tracked and recorded.
The initial gauge length is automatically set at the area with the greatest amount of strain since that is where any type of break would be anticipated. Consequently, the break will automatically appear in the middle of the gauge length. The advantages this offers to the customer are clear as significant amounts of specimen material and test time are reduced since specimens no longer have to be discarded.
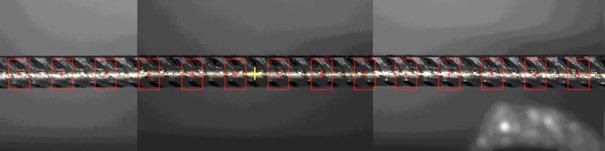
Virtual gauge marks on a ribbed steel specimen. Image Credit: ZwickRoell GmbH Co. KG
The test images can also be saved, and the ‘test re-run’ option utilizes the recorded image series to retroactively change or shift the initial gauge length. Then, a recalculation is carried out in testXpert III software based on the updated initial gauge length to determine the new strain, as well as the associated measured values, which are then saved clearly as a separate test in the software. Therefore, this option can be applied in component testing, when evaluation of local strain at different points is necessary, or in when specimen necking has occurred outside the original initial gauge length in standard tensile tests.
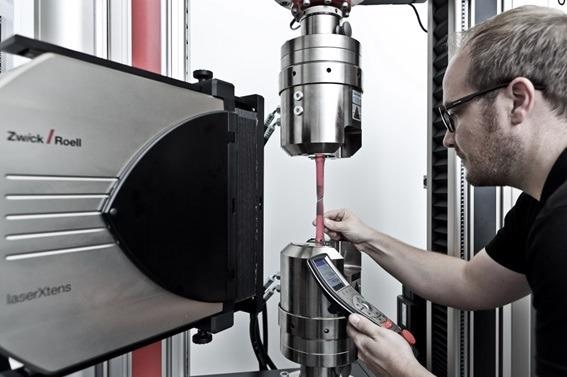
laserXtens extensometer utilizing test sample speckle pattern. Image Credit: ZwickRoell GmbH Co. KG
The ZwickRoell laserXtens is uniquely exceptional since the application of gauge marks are not necessary. This eradicates the necessity for specimen marking and the options can be used even more effiiciently. ZwickRoell array technology makes it possible for the system to provide high resolution (0.07 µm) in a wide field of view (220 mm). The novel, patented system laserXtens is based on the laser speckle correlation method.
Laser beams are scattered into the specimen through natural surface roughness and produce a speckle pattern that offers unique, distinctive features comparable to a fingerprint. Consequently, the testXpert III software allows for virtual gauge marks to be defined as desired and appropriate. A key benefit of such video systems is that the laserXtens’ speckle pattern consistently sustains a constant level of quality over the entire surface of the specimen.
Additionally, each test specimen does not rely on the user to apply the pattern. A solid basis for reliable test results, laserXtens not only features special attributes due to the capacity to test without using gauge marks but for strain-rate controlled tests to ISO 6892-1 Method A1, it is the first non-contact extensometer to be available. If optimal functionality and maximum flexibility are needed, the laserXtens can be used in combination with videoXtens to produce two extensometers in one that incorporates all available options; the perfect choice for research laboratories and universities.
In conclusion, optical extensometers offer added value through additional functions as well as covering standard testing applications when compared with contact-type extensometers.
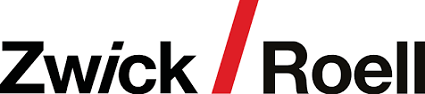
This information has been sourced, reviewed and adapted from materials provided by ZwickRoell GmbH Co. KG.
For more information on this source, please visit ZwickRoell GmbH Co. KG.