In this interview, AZoM talks to Richard Holland, Managing Director at TRB Lightweight Structures, about TRB's recent advances in composite manufacturing and potential future avenues for the field.
Could you give our readers an overview of TRB Lightweight Structures and the solutions you provide?
TRB Lightweight Structures designs, engineers and manufactures lightweight components for transportation, we are committed to lightweighting. We have been on that journey for quite some time, aggressively trying to get our products as light as possible. Essentially, when you look at the global CO2 challenge, it is obvious to try to remove the combustion engine and all of the problems associated with it. With this comes changing to a cleaner power solution.
The second, less well-known part of the issue is that power consumption is growing exponentially. There is a need to solve power consumption. Our small part of that journey is to make things lighter and reduce power usage. We have developed high volume composite components at a very comparable cost to aluminium to try and help solve that.
What is the history of the company's lightweight composite components and what type of sectors have these been used in?
Historically, the company was set up as part of Ciba-Geigy back in the 1950s. Back then they developed aluminium honeycomb that was used in the manufacturer of aircraft to make them more lightweight and TRB was set up to produce M and F boards, or as they are known today TRB’s Cellite range.
The fundamental roots of the business are driven towards lightweighting transport for trains, buses, trucks, and cars. We have historically been very involved in trains.
Recently in the last four or five years, we have been radically developing new solutions and technology to do a far better job at getting very lightweight solutions, specifically focusing on composites and how to deliver products at a high volume
How does manufacturing innovation fit in with the environmental values of TRB Lightweight Structures?
Reducing the weight of vehicles means less energy consumption and allows electric vehicles to travel further on one charge. We believe composites are the way to achieve this. When you look at carbon fibre and composites, that has historically been a low volume, formula one style product. It is handmade, expensive, high-tech, and very light. The product is great, but the challenge for everyone is how do you get that into mainstream transportation at very high volume. You cannot get the amount that is required by hand-making it and secondly, it is too expensive. It needs to be far more competitively priced.
We have been investing and building our own machines, technology and science in order to vertically integrate the supply chain within the same company. Through making our own machines, we have managed to come out with new technology that allows us to solve the very manual nature of composites. We have managed to create automated lines that can build parts for people.
How does this new manufacturing process revolutionize the composites industry? What does this mean for TRB?
It essentially allows us to make composite components at much higher rates and far more competitive costs. This means we can significantly increase the number of components on a vehicle that we can produce, in composites, to volume and competitively priced.
The composite industry has been growing year-on-year now for quite some time. The U.K. government has selected it as one of six industries that they are focused on developing, and through the Catapult centres around the country, they are supporting the composite industry technically.
By increasing the ability to be competitively priced and to hit volumes, the growth of the industry will carry on. And we are seeing growth. This year, even during the COVID crisis, we have built a new factory in the U.S, installed an automated line in the U.S. to support factory production over there. The new facility in the U.S. is in conjunction with Toyota Tsusho. I can only see this growth continuing.
Could you give us some examples of the environmental applications lightweight composite components are used in?
Our composites are important in the move to electrification, whether that is battery, hybrid or hydrogen vehicles. The range of vehicles is really important, whether it is an aircraft and its flight time, or it is an electric truck, bus or car and the distance it can travel between charges.
Weight has a massive impact on that. Our technology is helping, and we are working with a whole host of companies to help them further reduce weight in their vehicles and increase distance.
Some of the reticence that the public will have around electric vehicles is all about range and the fear of what range is possible. So the more range we can get, the faster that we can move towards electric vehicles.
What are the benefits of lightweighting in terms of energy efficiency?
You improve the consumption by 0.6 kilowatts per 100 kilometres, with every 100 kilograms of vehicle mass. For every kilogram, you improve range by roughly half a kilometre.
How do the composite materials from TRB Lightweight Structures differ from other suppliers?
In the last two years we have developed our own pre-preg. We have had to do that because the applications, particularly battery applications, have structural and thermal properties that we have to meet.
We have put significant time and effort into this. We have installed our own labortory within the building to do all of our own testing. We are continuously trying to develop materials to get anywhere up to 1,000 or 1,200 degrees C in terms of its tolerance.
Everyone understands the game structurally. But we have been working on the thermal properties as well as electrical properties. Mostly, we have gone further in developing materials that can cope with the very high thermal runaway events that happen within batteries.
What is TRB Lightweight Structures' vision for the future?
We would love to support the electrification of transport and do our bit to help lower the energy consumption rate. We have one high volume line that has been installed in the U.S. and we are currently installing our second in the U.K for this purpose
As we grow with our customers, supporting their power solutions, we hope to continue to solve some of the earth’s environmental challenges. Our next mission is to make a fully recyclable product.
About the interviewee
Richard Holland has been MD of TRB since 2014 and a lean practitioner since 1995. Since becoming the MD, TRB has tripled in size from £5m - £15m in sales, doubled their workforce which has resulted in winning significant contracts with major international OEM’s. As part of the growth, TRB has multiple locations in the UK and has opened a new factory in the US, in late 2019 as part of a joint venture with one of the large Automotive OEMs.
In the last few years, Richard has spearheaded the focused on lightweight structures for the sustainable transportation industry and particularly driven development in high volume carbon fiber products that provide high strength and lightweight whilst driving cost down through high automation.
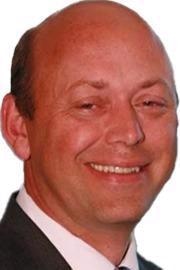
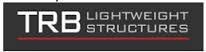
This information has been sourced, reviewed and adapted from materials provided by TRB Lightweight Structures Ltd.
For more information on this source, please visit TRB Lightweight Structures Ltd.
Disclaimer: The views expressed here are those of the interviewee and do not necessarily represent the views of AZoM.com Limited (T/A) AZoNetwork, the owner and operator of this website. This disclaimer forms part of the Terms and Conditions of use of this website.