Microalloyed steels, often called High-Strength Low-Alloy steels (HSLA), are a group of materials that are strengthened by adding “micro” alloy concentrations to low-carbon mild steel.
Microalloying technology includes elements titanium (Ti), vanadium (V), and niobium (Nb) added either in combination or on their own, and sometimes in combination with different strengtheners such as copper (Cu), chromium (Cr), boron (B), nickel (Ni), and molybdenum (Mo) to attain desired mechanical properties.
The elements’ strengthening effects make microalloyed steels especially appropriate for high-strength applications by the facilitation of grain hardening and refinement.
Microalloyed steel development began over half a century ago and represents an important steel category that makes up approximately 12% of the world’s total steel production.
A variety of parts of the world use microalloyed steels in every major steel market sector. Their development has had a significant role in the growth of particular key industries.
Microalloyed steels can be found in industrial applications such as:
- Heavy equipment
- Bridges/suspension components
- Building structures
- Shipbuilding/Naval vessels
- Pressure vessels
- Automotive industry
- Offshore/platforms
- Oil & Gas line pipe
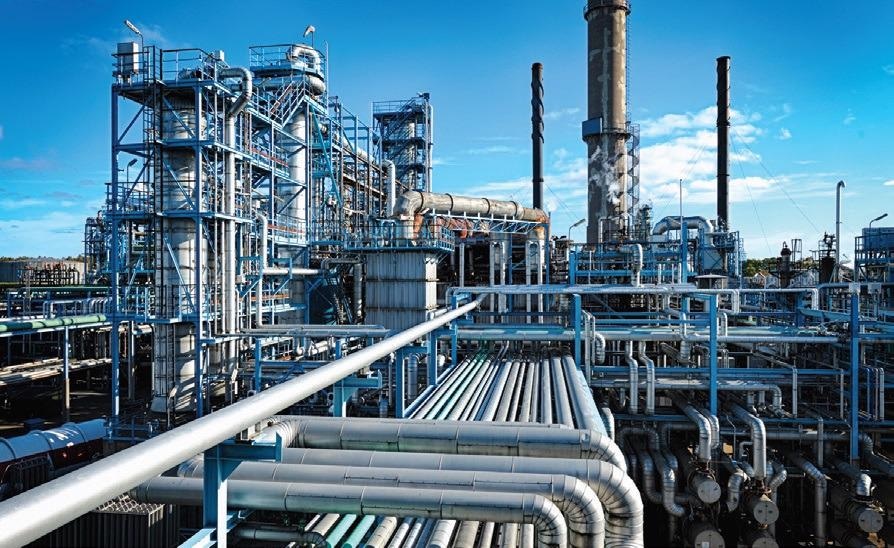
Image Credit: Thermo Fisher Scientific - Elemental Analyzers and Phase Analyzers
The most popular material for use in construction is hot-rolled plain carbon steel. Its strength can be amplified by increasing the carbon content and is proportional to the carbon equivalent (CE). Essentially, CE is the combined effect of the manganese and carbon content in a steel based on the formula [CE = %C + %Mn/6].
Raising the carbon content and resulting carbon equivalent improves strength, but it also diminishes some other properties like weldability, ductility, and toughness. Higher yield strengths are able to be achieved with a large reduction in carbon content via the strengthening mechanisms of microalloying elements Ti, V, and Nb.
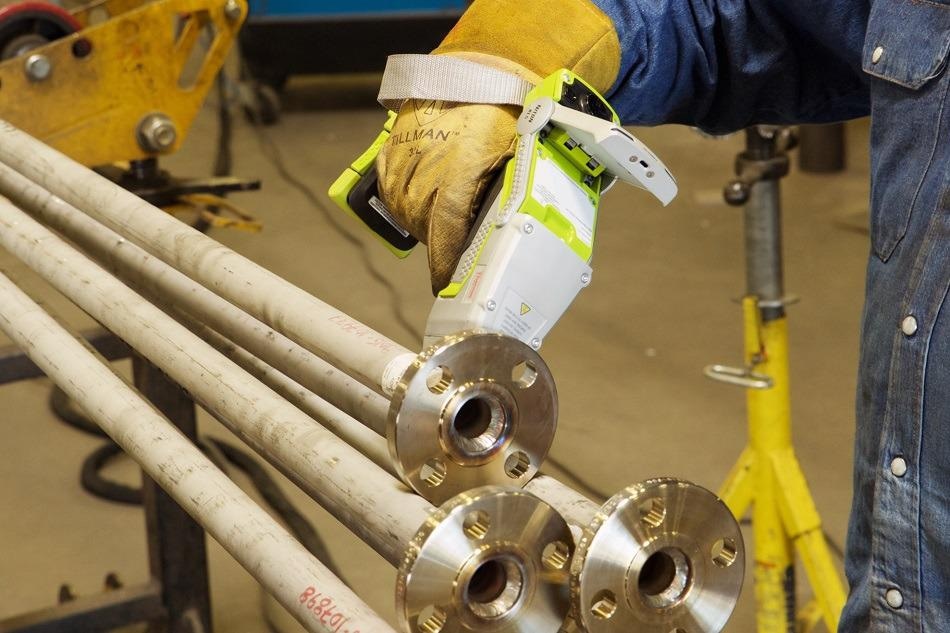
An inspection is conducted using the handheld Thermo ScientificTM NitonTM XL5 Plus Analyzer. Image Credit: Thermo Fisher Scientific - Elemental Analyzers and Phase Analyzers
Weldability is greatly improved and the risk of cracking for specific applications such as pipelines, bridges, and buildings is reduced by this low-carbon content.
Some noteworthy benefits of the use of microalloyed steels are:
- Heat treatment and susceptibility to cracking are minimized by lower carbon equivalent (CE)
- Weldability and weldment toughness is improved by reduced carbon content
- Weight reduction by more than 25% compared to hot-rolled carbon steel
- Increased pumping capacity inline pipe enables operational savings
- Lower fabrication costs from weight savings in transport and handling
The Pipeline and Hazardous Material Safety Administration (PHMSA) issued advisory bulletin ADB-09-01 in 2009 to operators and owners of hazardous liquid pipeline and natural gas pipeline systems that an integrity issue had been discovered in regard to microalloyed high-grade line pipe.
Tests conducted on line pipe installed in pipeline systems showed that not all the material met the American Petroleum Institute (API) Specification for Line Pipe API 5L requirements.
Pipe joints made from the same heat showed variable mechanical and chemical properties by as much as 15% below the values stated by the pipe manufacturer-produced mill test report, including microalloying elements Ti, V, Nb, and others.
Operators or owners need the assurance that the increasing number of large diameter, high pressure hazardous natural gas and liquid pipelines are constructed to the best standards and fully tested with the best technology available in order to conform to safety guidelines and lessen susceptibility to failure.
Portable X-ray fluorescence (XRF) is an ideal option for material chemistry verification. The new Niton XL5 Plus Analyzer enables precise, accurate, and fast analysis of microalloying elements in steel and other elements in the field.
Niton XL5 Plus Handheld XRF Analyzer
The new Niton XL5 Plus Analyzer is the lightest and smallest high-performance XRF metal analyzer on the market. The small size and light weight of the Niton XL5 Plus Analyzer enables access to more test spots and reduces operator fatigue.
Compact measurement geometry and a new powerful 5W X-ray tube offer the best sensitivity and highest performance for the most demanding applications, for example, residual element measurement.
The Niton XL5 Plus Analyzer offers these key benefits:
- Rugged housing, dustproof and waterproof for use in harsh environments
- Small spot analysis and an integrated camera for accurate image capture and sample positioning
- The flexible user interface allows easy optimization and custom workflow solutions for specific applications. The sum of the microalloying elements can be automatically calculated using the Niton XL5 Plus Analyzer's pseudo-element feature
- Confident results each time with unparalleled chemistry and metal grade identification accuracy
- Excellent microelement detection (Nb, V, Ti) for reliable and fast microalloyed steel analysis
The Niton XL5 Plus Analyzer is the latest offering in our market-leading family of Niton handheld XRF analyzers. The Niton XL5 Plus Analyzer is specially designed for high accuracy, fastest analysis time, and low detection limits for microalloying elements like Ti, V, and Nb.
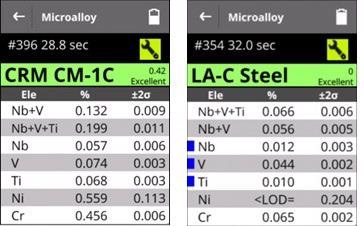
Niton XL5 Plus Analyzer's pseudo-element feature enables automatic calculation of the sum of microalloying elements. Analyzer screens featured correlate to repeatability study results, next page: left screen to Table 1; right screen to Table 2. Image Credit: Thermo Fisher Scientific - Elemental Analyzers and Phase Analyzers
Test Method and Results
Certified reference standards and samples were analyzed with a handheld Niton XL5 Plus XRF Analyzer after making sure that the surface was clear of contaminants.
When exposed to atmospheric conditions, carbon steel alloys oxidize easily. When carrying out an XRF analysis, this oxide coating can alter the reading’s accuracy. In order to ensure an accurate reading, it is crucial to get rid of any corrosion.
As well as oxidation, there can often be grease, oil, or paint on the surface. All surface contamination needs to be removed from the area so it can be analyzed.
Data quality objectives dictate the minimum analysis time used and the requirements for sample preparation. Using a total measurement time of 30 seconds, ten individual XRF readings were collected.
The objective of the microelement analysis is to determine whether the delivered material consists of the correct levels of microalloying elements Ti, V, and Nb as certified by the corresponding Material Test Report (MTR).
Further, the sum of these elements can be verified to meet the acceptance criteria and not surpass restrictions prescribed in the purchase order or material specification.
Currently, the limit on the combined microalloying content Ti+V+Nb is 0.15 percent for steels with a yield strength above 60 ksi.
Table 1 and Table 2. These tables represent the data collected from a repeatability study conducted with carbon steel samples using the Niton XL5 Plus Analyzer. Ten individual tests were conducted for 30 seconds each in two sample rounds. The Niton XL5 Plus Analyzer's Average Result is shown for each round. The one sigma standard deviation was calculated using the ten individual results from each round. As shown by the test results, an agreement between laboratory results and the Niton XL5 Plus Analyzer is consistent. Source: Thermo Fisher Scientific - Elemental Analyzers and Phase Analyzers
Repeatability Study Results of Microalloy Elements in Carbon Steel Samples
Round #1 Results Using the Niton XL5 Plus Analyzer |
Run Number |
Nb |
V |
Ti |
Nb+V |
Nb+V+Ti |
1 |
0.063 |
0.072 |
0.068 |
0.135 |
0.203 |
2 |
0.058 |
0.075 |
0.068 |
0.134 |
0.202 |
3 |
0.060 |
0.073 |
0.069 |
0.133 |
0.202 |
4 |
0.064 |
0.075 |
0.070 |
0.139 |
0.209 |
5 |
0.063 |
0.073 |
0.069 |
0.136 |
0.205 |
6 |
0.063 |
0.074 |
0.073 |
0.137 |
0.210 |
7 |
0.058 |
0.073 |
0.072 |
0.131 |
0.203 |
8 |
0.057 |
0.068 |
0.069 |
0.125 |
0.194 |
9 |
0.060 |
0.073 |
0.067 |
0.133 |
0.200 |
10 |
0.061 |
0.073 |
0.070 |
0.134 |
0.204 |
Material Test Report |
0.054 |
0.073 |
0.066 |
0.127 |
0.193 |
Niton XL5 Plus Average Result |
0.061 |
0.073 |
0.070 |
0.134 |
0.203 |
Repeatability Study of Microalloy Elements in Carbon Steel Samples
Round #2 Results Using the Niton XL5 Plus Analyzer |
Run Number |
Nb |
V |
Ti |
Nb+V |
Nb+V+Ti |
1 |
0.012 |
0.043 |
0.010 |
0.055 |
0.065 |
2 |
0.013 |
0.041 |
0.012 |
0.054 |
0.066 |
3 |
0.016 |
0.042 |
0.009 |
0.058 |
0.067 |
4 |
0.017 |
0.040 |
0.011 |
0.057 |
0.068 |
5 |
0.015 |
0.046 |
0.010 |
0.061 |
0.071 |
6 |
0.014 |
0.043 |
0.011 |
0.057 |
0.068 |
7 |
0.012 |
0.044 |
0.010 |
0.056 |
0.066 |
8 |
0.015 |
0.041 |
0.010 |
0.056 |
0.066 |
9 |
0.016 |
0.042 |
0.010 |
0.058 |
0.068 |
10 |
0.015 |
0.041 |
0.010 |
0.056 |
0.066 |
Material Test Report |
0.013 |
0.045 |
0.010 |
0.058 |
0.068 |
Niton XL5 Plus Average Result |
0.015 |
0.042 |
0.010 |
0.057 |
0.067 |
Table 3. Limits of detection (LODs) for the Niton XL5 Plus Analyzer are listed in Table 3. LODs are calculated as three standard deviations (99.7% confidence interval) for each element at several different measurement times; limit of detection improves as a function of measurement time. Source: Thermo Fisher Scientific - Elemental Analyzers and Phase Analyzers
Niton XL5 Plus Analyzer Limits of Detection |
Measured Time, SecondsPlus |
Ti |
V |
Nb |
SUM |
15 |
0.0036 |
0.0036 |
0.0012 |
0.0084 |
30 |
0.0025 |
0.0025 |
0.0008 |
0.0058 |
60 |
0.0018 |
0.0018 |
0.0006 |
0.0042 |
Conclusion
Excellent agreement with the material test reports is demonstrated by results achieved using the Niton XL5 Plus Analyzer.
The Niton XL5 Plus Analyzer offers outstanding trace and microelement sensitivity and precision for the analysis of microalloyed steel. Given appropriate sample preparation, the analyzer can reliably and quickly verify whether the microalloying element levels agree with the mill test report and reach the chemical composition requirements per specification.
Microalloyed steels owe their accomplishment to complementary strengthening mechanisms, specifically precipitation hardening and grain refinement, developed by adding the key elements titanium (Ti), vanadium (V), and niobium (Nb).
Over the last few decades, technologies for the manufacture of microalloyed steels have progressed rapidly because of the demands from the line pipe arena in areas such as gas and oil extraction, transportation, and construction.
When the highest sample throughput or low detection limits are crucial, the mixture of software, hardware, and direct industry experience from Thermo Fisher Scientific offers the perfect solution for the most difficult analytical requirements.
The enhanced analytical capability for trace quantities of Ti, V, and Nb, and other unique abilities make the Niton XL5 Plus Analyzer the perfect tool for microelement analysis.
In addition to residual elements, the Niton XL5 Plus Analyzer is able to rapidly provide positive material identification (PMI) and full chemical analysis for a wide range of alloy grades used in the gas and oil industry.
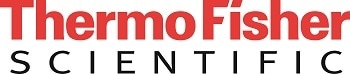
This information has been sourced, reviewed and adapted from materials provided by Thermo Fisher Scientific – Handheld Elemental & Radiation Detection.
For more information on this source, please visit Thermo Fisher Scientific – Handheld Elemental & Radiation Detection