Wastewater lift stations accumulate a wide variety of debris, including t-shirts, wipes, boards, rocks and other odd materials that can end up in the wet well. Items do not get through the pump meaning numerous operators have been pulling a clogged pump during Super Bowl Sunday to get rid of stringy rag balls or further debris. In serious instances, sanitary sewer overflows cause regulatory fines.
Grinder Pumps as a Solution
Grinder pumps are created to manage solids, diminishing their size enough to go through the pump and force main. Grinder pumps for municipal and industrial employment are created for low-flow, high-head environments. Not every grinder pump is alike; in fact, the incorrect grinder pump might need a lot of the operator’s time for upkeep and unblocking tasks. This article details some points to consider when selecting a grinder pump.
Cutting Technology
Debris should be cut down to around 5 millimeters (about 0.2 inches) prior to expulsion to the force main. The expelled debris requires being easily passed through a two-inch diameter main. If the debris field is overly fine, solids may settle out in the force main. Certain grinder pumps macerate the waste to appropriate sizes. The macerating ring is composed of multiple teeth on the open-air diameter of a rotating component. Grooves between the teeth fill with debris, minimizing their efficiency and ultimately clogging.
Such units require frequent modification to make sure the cutting tolerance is preserved. Cutting or slicing debris into minor bites is more efficient than grinding or chewing. A grinder pump with a dual action cutter system should be obtained. For instance, HOMA’s design is comprised of two cutter blades on the outer pump and two on the inside. These cutters are established at a set tolerance and do not require adjustments.
The motor runs at 3450 RPM, meaning the lower blades create 6,900 cuts per minute, followed by 6,900 cuts per minute with the upper blades. The ensuing 13,800 cuts per minute offer the appropriate debris field for a minute force main. The close tolerance of the cutters avoids admittance of bigger items, like a two-by-four, into the pump. The cutters will, however, take “bites” from a big rag until it can move through the pump.
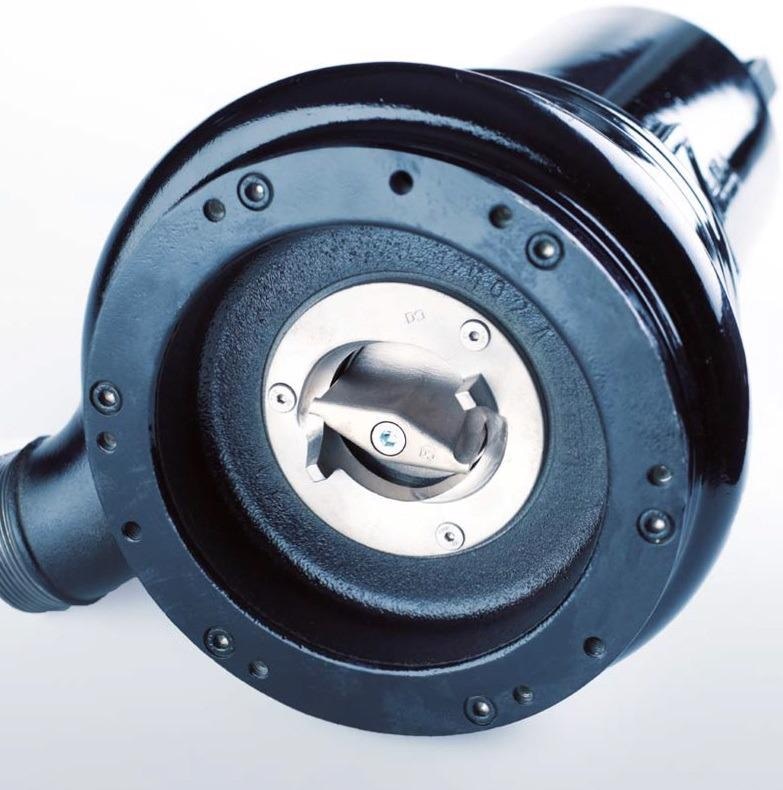
Image Credit: Homa Pump Technology
Grinder Pump Design
Float systems are the most popular means of beginning and halting a pump. When the sewage achieves a precise level in the wet well, the pump starts. Following pumping down to the desired level, the pump turns off. Certain grinder pumps are created so that following the pump being turned off, all debris being cut remains inside the macerating ring. When the pump is restarted, the unit needs to fight through rags that were dragged into the pump. Such units are more prone to develop blockages.
Further pressure on the pump and motor may create the need for further maintenance or shorten life span. HOMA Pump’s rotating and stationary cutters offer just two contact points compared with continuous contact with the waste. The initial set of cutters is situated outside the pump, under the impeller. As such, when the pump stops, debris falls away from the cutters rather than being pulled halfway through the pump. Once the pump restarts, no debris is trapped within the pump.
Grinder Pump Durability
Sand and grit frequently appear in sewage, which can create wear and increase the tolerance between the suction cover and impeller. The employment of high-quality materials guarantees endurance of the cutters. HOMA’s cutter system is created out of stainless steel alloyed with cobalt, vanadium, and molybdenum. The cutters are hardened to a minimum of a Rockwell® C-55 level to guarantee a lengthy life. The GRP Series possess the same major casting as every HOMA pump. The motor housings, volutes, and impellers are constructed Class 40 cast iron.
This is a finer finish than employed in multiple pumps. It is a slicker, thicker material, less likely to be affected by abrasives. Such high-quality materials guarantee a lengthy service life and lessened maintenance expenses.
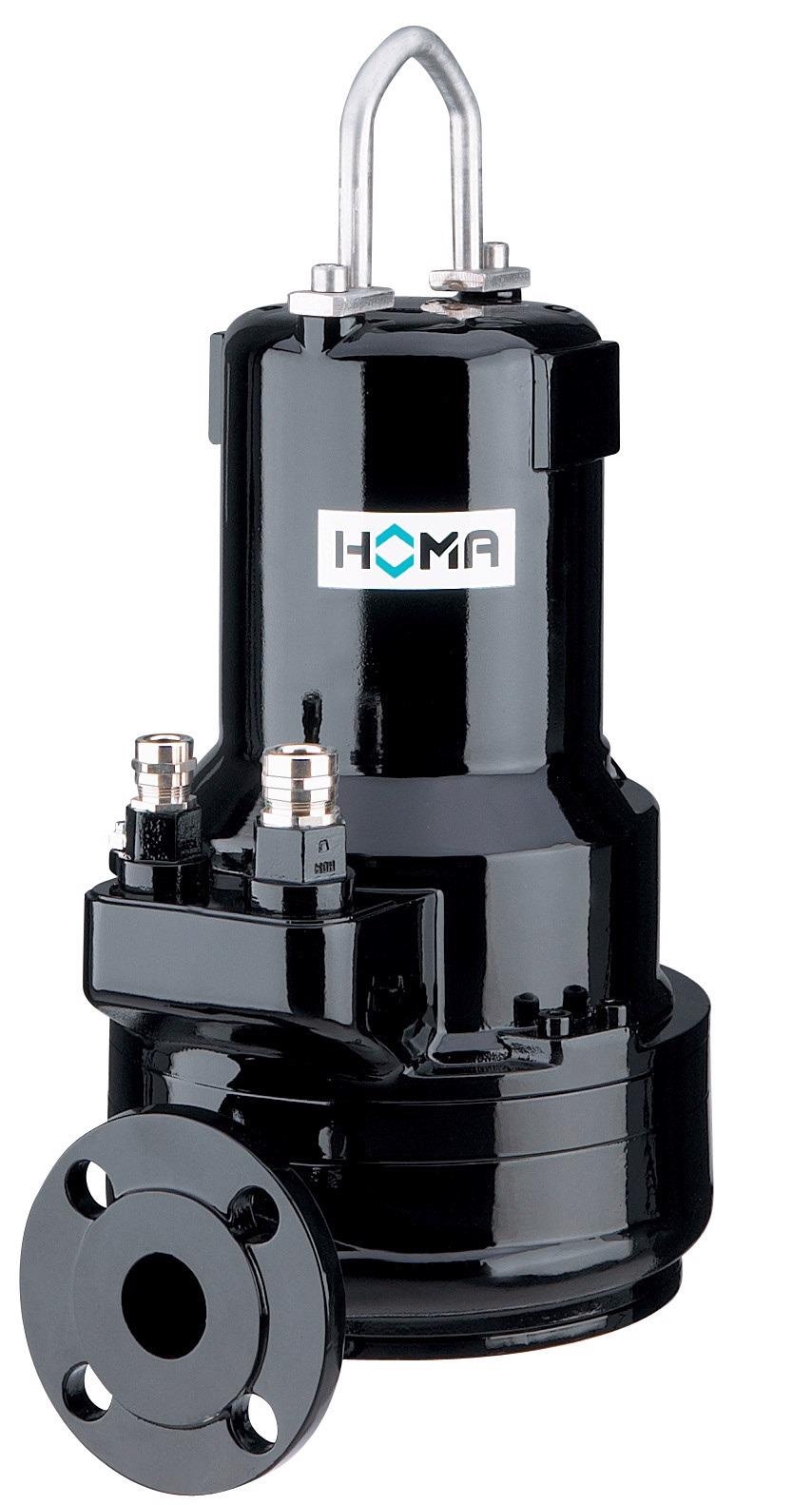
Image Credit: Homa Pump Technology
Pump Performance Range
Employing a product with a broad range of performance is beneficial for utilities with many pump stations. It is additionally vital that the cutter design is constant for each size pump. HOMA’s concentrated areas are municipal and industrial, but they additionally offer residential pumps. Their wide variety of products include single and three-phase grinder pumps of 1 to 13 horsepower. Every GRP Series pump possesses an identical cutter design and high-quality production.
A distinctive application supplied by HOMA’s grinder pumps arises in mountainous areas. Rather than building two lift stations — one at the base and one halfway up the mountain — HOMA offers a tandem assembly. By piggybacking one pump to the other, head pressure is doubled. Both pumps are constructed as one unit and may be elevated and dropped as one. Employing the biggest pumps, this application can surpass 450 feet of pressure.
Replacement Parts and Service
Lift station pumps are vital infrastructure, and as such, guaranteeing accessibility of spare parts is a priority for operators. HOMA employs non-proprietary mechanical seals and bearings for each pump. Such parts are accessible locally when required instantaneously in the field. HOMA additionally supplies more than $10 million in accessible pumps and parts inventory in their Connecticut factory. With a big inventory and a wide variety of pump designs and sizes, HOMA is frequently requested to provide replacement pumps. They have a broad variety of guide rail adapters for other manufacturers’ pumps. This means HOMA’s pumps can be dropped into a wet well with only a small amount of downtime. HOMA possesses its own guide rails for new stations or for enhanced stations with new piping.
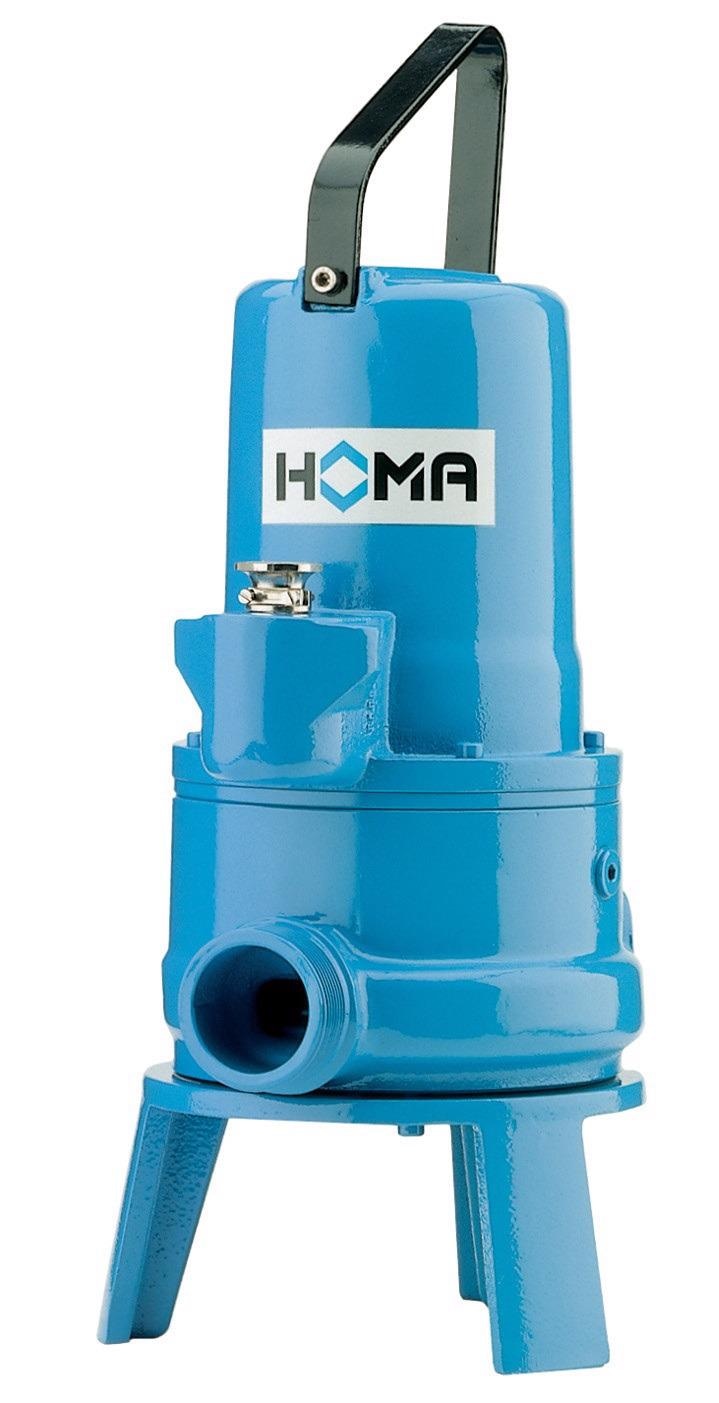
Image Credit: Homa Pump Technology
Protecting the Environment and Saving Costs
Just a single clogged pump can cause sanitary sewer overflows, personnel costs, and maybe fines or bad publicity. By selecting the right grinder pump, those problems can be eradicated. HOMA’s grinder pumps offer a long service life. They need zero routine modification and have low downtime in the field. The outcome is smaller costs, fewer issues, and an improved environment.
Acknowledgments
Produced from materials originally authored by Ryan Sura, Senior Application Engineer HOMA Pump Technology, Inc.
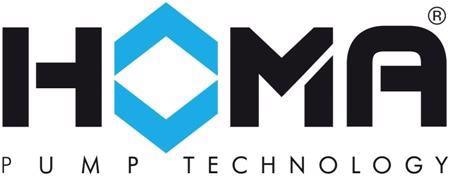
This information has been sourced, reviewed and adapted from materials provided by Homa Pump Technology.
For more information on this source, please visit Homa Pump Technology.