All those involved with wastewater pump applications — operations managers, in-house engineers, and consulting engineers — desires that their recently retrofitted station to run dependably and effectively. But all pump retrofit installations meet different issues. For this reason, looking further than the initially stipulated flow rates, and assessing the service history and pump system operation all together prior to replacing equipment with an identical model, can be extremely beneficial in rectifying historical issues and enhancing operational effectiveness.
The following guidelines should be considered for pump replacement alternatives prior and a consultation with a pump distributor/manufacturer with knowledge of the difficulties of wastewater collection and treatment operations should be considered.
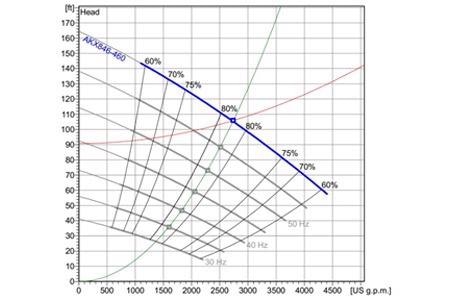
Image Credit: Homa Pump Technology
Innovate — Do Not Just Replicate
If the issue requires an upgrade, emergency replacement, or planned replacement of equipment coming close to the end of its likely service life, it is critical to avoid the desire to order a new pump just by reproducing the specs of the current unit. Despite whether it is difficult to note the exact inflow and system loss curves of a particular application, it is vital to have the largest amount of real-world information as feasible to enhance hydraulic efficiency and enhance consistency.
This is particularly true as pump sizes and their price tags get bigger and if there have been frequent issues because of inadequate application design or performance:
Oversized Pumps
If the current pump was specified in expectancy of community buildout that did not take place, or if reductions in population and manufacturing have cut daily throughputs, stipulating the same pump configuration will not lessen current inefficiencies and energy waste — and can also create additional issues.
Underperformance
Although variable frequency drives (VFDs) can, in particular instances, enhance energy use to volume demands, running them at an overly slow speed can cause further issues with wastewater. Sedimentation, scale, and solids can accumulate in discharge piping due to low-velocity flows.
Performance Factors to Consider
It is often easy to attribute performance problems to a pump, but some investigation can identify additional factors that can be rectified during the retrofit process to prevent a continuation of the same problems. Observations from maintenance personnel closest to the daily function of those pumps can offer vital insight into understanding current operations and creating new design standards for replacement pumps.
Time should be spent evaluating current digital or hard-copy performance documentation or organizing an onsite review and drawdown testing to grasp the individual challenges of the particular pump station. Both of those steps can spare the thousands of dollars of the cost of reworking a flawed installation or to accept inefficient energy use over the life of that installation.
Pinpointing problems outside of general lifecycle wear can show how to identify the new installation to prevent them. The following factors should be considered:
Pump Performance
Was the latest pump breakdown the first or just the most recent in many failures? Have the triggers of failure been the same or different? Have performance problems been linked to pressure or to flow volume? Historical background can help to pinpoint possible triggers and solutions. For example:
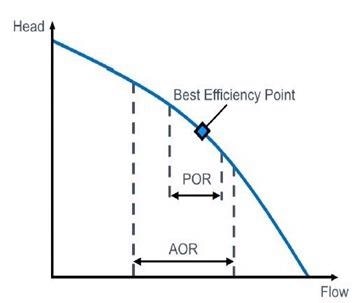
Figure 1. Although the total pump curve for variable speed pump performance covers a wide range of flow rates and head pressures, those pumps should only be operated within the allowable operating region (AOR), which is typically between 50 percent and 130 percent of the best efficiency point (BEP) flow on the curve. Ideally, operations should be concentrated within the preferred operating region (POR), which is between 70 percent and 120 percent of BEP flow (80 percent to 120 percent for higher specific-speed pumps). Image Credit: Homa Pump Technology
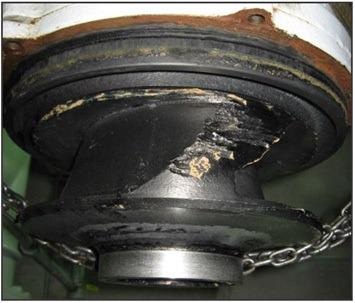
Figure 2. Impeller wear in wastewater pumping can have different causes (e.g., cavitation or the harsh makeup of the wastewater). It is important to discern the reasons for past pump problems and correct them before specifying the retrofit pump. Image Credit: Homa Pump Technology
Vibration: A pump that is operating away from its design duty point or beyond its specified allowable operating region (AOR) may be a victim of disproportionate vibration or recirculation cavitation (Figure 1). When identifying a new pump, a vibration test at the factory should be requested to determine a baseline that can be employed as a reference point for the installation in the future.
Noise: If the noise is cyclical and sounds hydraulic, it may be surface vortex ingestion or submerged vortex ingestion, which can both be simply rectified once recognized. Continuous noise that sounds like the unit is pumping rocks may suggest cavitation or air entrainment (Figure 2).
Air Entrainment: Influent wastewater falling from an inlet pipe high above the surface of a wet well can bring air into the pump and piping. If that air becomes trapped by high spots in the pipeline and there is not sufficient carrying velocity to move it out, it can hinder flow. Employing baffles in the wet well or broadening the inlet piping to under the wet well surface can avoid this problem.
Hydraulic Wear: If an application encounters unnecessary hydraulic wear on the impeller with no cavitation problems, air entrainment, or recirculation present, evaluation of the pumped media may be necessary. Alternate construction materials or coatings that can withstand the composition of the sewage or chemical washdowns being pumped should be found (Figure 2).
Low-Velocity Flows: Softstarters that take an excessively long time to build up to full speed, or VFDs that work too slowly for long periods of time, can create a buildup of sedimentation, solids, and ragging materials because of inadequate fluid velocity to keep them in suspension.
Electrical Problems: If pump output or service life is inadequate, the quality of the power supply should be checked. Various power quality issues can influence motor life and performance.
Design Inflow
The current pump specification and operation should be consistent with the current inflow. If documented SCADA data does not exist, different methods should be sought — like drawdown tests or on/off cycle data — to quantify actual inflow conditions.
Existing Infrastructure
Can the control panel and/or piping be switched out with the pump, or must the new pump work inside the constraints of the current infrastructure? In some instances, altering the piping might allow for new motor possibilities. If that is not feasible, simpler alterations to starters and circuit breakers may allow the employment of a larger motor. A critical element to consider in wetpit installations is the make and model of the current rail system employed to raise and lower the existing pump. It is crucial to ensure that the correct rail adapters will be accessible to match the new pump to the rails (Figure 3).
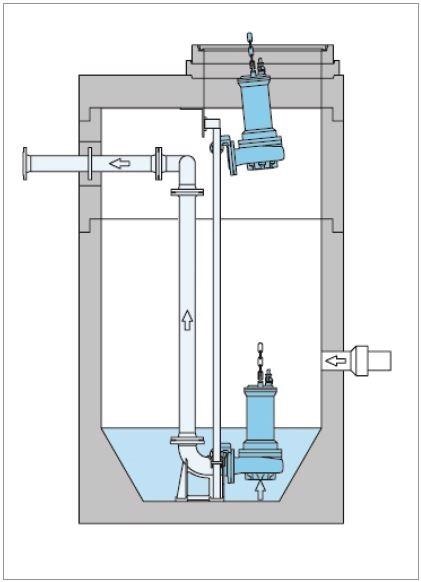
Figure 3. Rail mounting systems that enable a submersible pump to be raised from a wastewater pump station sump for service or cleaning must be matched to the dimensions of the pump with the appropriately sized rail adapters. Image Credit: Homa Pump Technology
The new installation must comply with Hydraulic Institute intake standards, particularly as the stakes increase with larger pumps. Inlet piping must be modified to reduce twists and turns that can create a range of pressure, velocity, or turbulence performance problems. Such problems can affect where the pump operates on its curves or cause recirculation that creates cavitation like damage, vibration, or premature failure.
Proper Support: With dry-pit retrofit applications, neglected problems with pump support and proper grouting of baseplates may cause detrimental impacts on performance. While smaller drypit submersible pumps may employ a fabricated metal ring stand bolted to the concrete floor, bigger pump sizes need concrete stanchions tied into the current rebar in the floor to raise the natural frequency of the structure so that it cannot be excited by pump rotation or blade-pass frequencies, which alter over a potentially wide range when a VFD is employed. In such instances, it is vital to stipulate adequate mass for the concrete support stanchions, and extreme care must be employed with the baseplate grouting technique.
Adequate baseplate mounting and grouting will bind the mass of the pump and the mass of the foundation into a monolithic structure. Leaving jacking nuts on the embedded threaded rod in place following the leveling of the baseplate and simply grouting around them (a frequent practice) will not permit the appropriate stretch on the baseplate mounting bolts, and it will stop effectively tying the mass of the pump and motor to the foundation. Bigger multidiscipline engineering firms frequently stipulate how to do this correctly, but not every firm does — and this detail is frequently left to the installer.
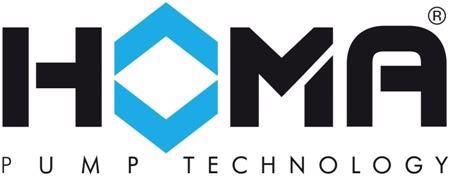
This information has been sourced, reviewed and adapted from materials provided by Homa Pump Technology.
For more information on this source, please visit Homa Pump Technology.